Pyrolysis is a thermochemical process that decomposes organic materials at high temperatures in the absence of oxygen, converting them into valuable products such as oil, gas, and char. A pyrolysis plant is designed to handle this process efficiently, particularly for biomass and waste materials like tires. The technology involves several key components, including feeding, pyrolysis, discharging, and emission cleaning systems. The process is highly efficient, environmentally friendly, and cost-effective, making it suitable for large-scale industrial applications. It also ensures safety through automated systems and emission control mechanisms. Pyrolysis technology is versatile, capable of processing various organic wastes into usable products, contributing to waste management and resource recovery.
Key Points Explained:
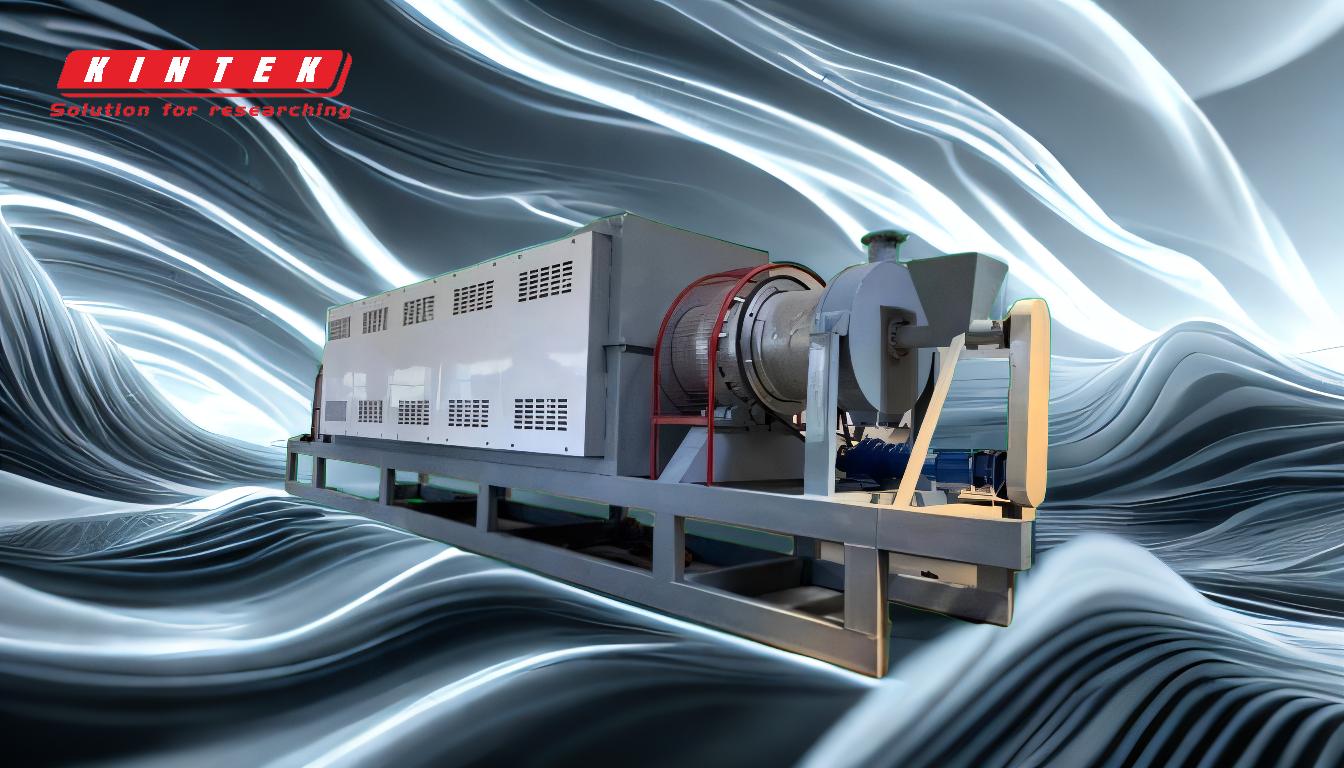
-
Components of a Pyrolysis Plant:
- Feeding Line: Automatically delivers raw materials (e.g., biomass, tires) to the reactor in a sealed manner to prevent contamination and ensure efficiency.
- Pyrolysis Reactor: The core component where high-temperature decomposition occurs. It includes a driving device, base, main furnace, and casing, all essential for operation.
- Discharging Line: Transports solid residues like carbon black into storage tanks, often equipped with cooling systems to manage heat.
- Emission Cleaning Line: Ensures environmentally friendly operation by purifying gases and particulates to meet emission standards.
-
Pyrolysis Process:
- Thermal Decomposition: Organic materials are heated in the absence of oxygen, breaking down into gas, liquid (oil), and solid (char) products.
- Continuous Operation: In a pyrolysis plant, the process is continuous, ensuring high efficiency and scalability for industrial use.
- Cooling and Recycling: Generated oil gas is cooled through a multi-step system to extract oil, while non-condensable gases are recycled to heat the reactor, enhancing energy efficiency.
-
Applications and Advantages:
- Waste Management: Pyrolysis is ideal for processing biomass, tires, and other organic wastes, reducing landfill dependency.
- High-Quality Products: The oil produced is of high quality and can be sold directly or refined further. Char and gas are also valuable by-products.
- Environmental Benefits: Advanced emission control systems, such as de-dusting and hydroseal, ensure minimal pollution, making the process eco-friendly.
-
Safety and Automation:
- Fully Automated Design: Modern pyrolysis plants are equipped with automatic anti-tempering devices and gas filtration systems, ensuring safe operation.
- Energy Efficiency: Rotary running mechanisms ensure uniform heating, reducing energy consumption and operational costs.
-
Industrial Scalability:
- Cost-Effective: Low production costs and high profitability make pyrolysis plants an attractive investment for large-scale industrial applications.
- Versatility: The technology can process a wide range of organic materials, making it adaptable to different industries and waste streams.
In summary, pyrolysis technology is a sustainable and efficient solution for converting organic waste into valuable resources. Its modular design, environmental benefits, and economic viability make it a key player in waste management and renewable energy production.
Summary Table:
Key Aspect | Details |
---|---|
Components | Feeding line, pyrolysis reactor, discharging line, emission cleaning line |
Process | Thermal decomposition, continuous operation, cooling, and recycling |
Applications | Waste management, high-quality products, environmental benefits |
Safety & Automation | Fully automated design, energy efficiency, emission control systems |
Industrial Scalability | Cost-effective, versatile, and adaptable to various organic materials |
Learn how pyrolysis technology can transform your waste management—contact us today for expert guidance!