The temperature of a porcelain furnace typically ranges between 600°C to 1200°C, depending on the specific application and type of porcelain being processed. This temperature range is significantly lower than that of graphitization furnaces, which operate at much higher temperatures (2500°C to 3000°C) due to the need to transform carbonaceous materials into graphite. Porcelain furnaces are designed to sinter or fuse porcelain materials, which require precise temperature control to achieve the desired properties such as strength, density, and aesthetic finish.
Key Points Explained:
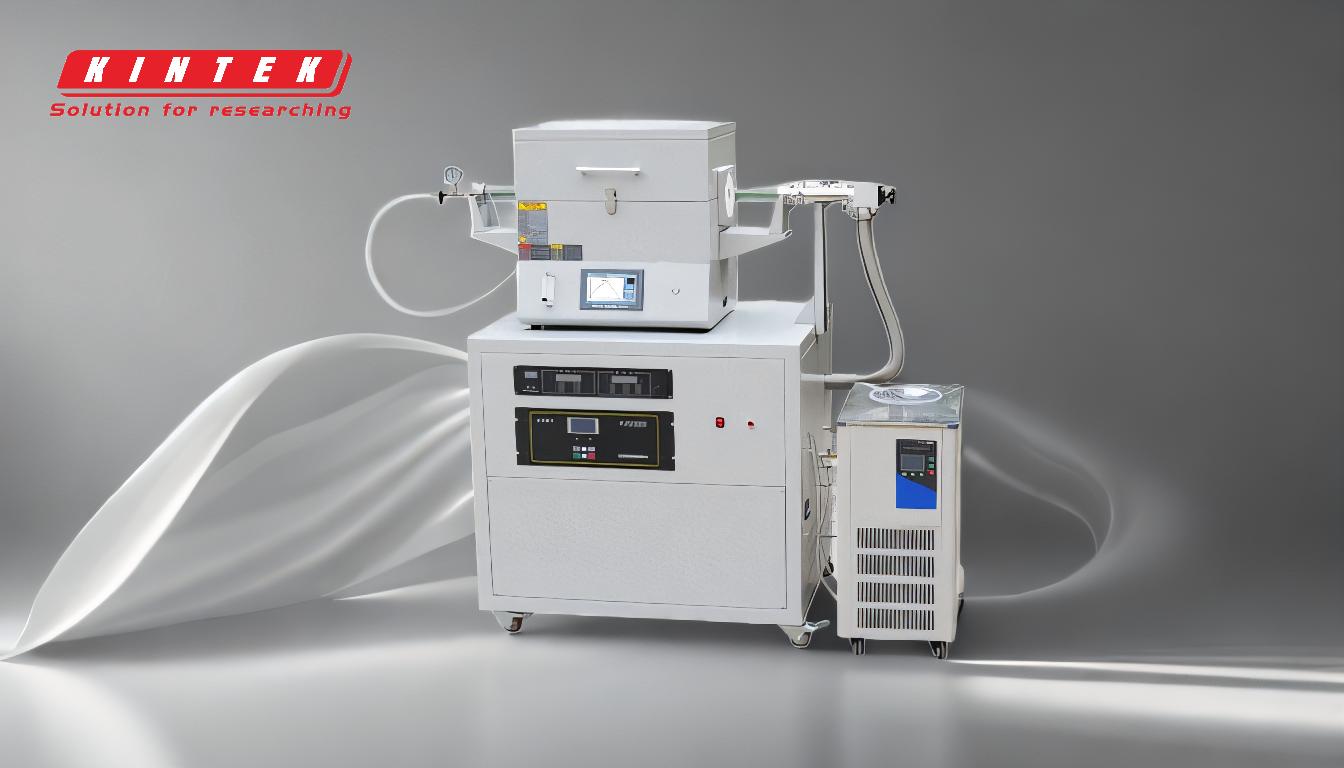
-
Temperature Range of Porcelain Furnaces:
- Porcelain furnaces generally operate between 600°C to 1200°C. This range is suitable for sintering and fusing porcelain materials, ensuring proper bonding and densification without causing thermal damage.
- The exact temperature depends on the type of porcelain and the specific application, such as dental ceramics, artistic porcelain, or industrial components.
-
Comparison with Graphitization Furnaces:
- Graphitization furnaces operate at much higher temperatures (2500°C to 3000°C) because they are designed to convert carbonaceous materials into graphite. This process requires extreme heat and an inert atmosphere to prevent oxidation.
- Porcelain furnaces, on the other hand, operate at lower temperatures because porcelain materials do not require such extreme heat for sintering or fusing.
-
Importance of Temperature Control:
- Precise temperature control is critical in porcelain furnaces to ensure the material achieves the desired properties, such as strength, translucency, and color consistency.
- Overheating can lead to warping, cracking, or other defects, while insufficient heat may result in incomplete sintering or weak bonding.
-
Applications of Porcelain Furnaces:
- Dental Ceramics: Used to create dental crowns, bridges, and veneers. The temperature is carefully controlled to match the specific requirements of dental porcelain.
- Artistic Porcelain: Used by artists and craftsmen to create intricate porcelain pieces. The temperature is adjusted based on the type of glaze and desired finish.
- Industrial Components: Used to manufacture high-strength porcelain parts for technical applications, such as insulators or laboratory equipment.
-
Factors Influencing Temperature Settings:
- Material Composition: Different porcelain formulations may require varying temperatures for optimal results.
- Firing Cycle: The rate of heating and cooling, as well as the duration of the firing process, can influence the final properties of the porcelain.
- Furnace Design: Modern porcelain furnaces often feature advanced controls and programmable settings to ensure precise temperature management.
In summary, the temperature of a porcelain furnace is tailored to the specific requirements of the porcelain material and its intended application. While it operates at significantly lower temperatures compared to graphitization furnaces, precise control is essential to achieve the desired results.
Summary Table:
Aspect | Details |
---|---|
Temperature Range | 600°C to 1200°C, depending on the application and type of porcelain. |
Comparison | Graphitization furnaces operate at 2500°C to 3000°C for graphite formation. |
Key Applications | Dental ceramics, artistic porcelain, industrial components. |
Importance of Control | Ensures strength, density, and aesthetic finish; prevents defects. |
Influencing Factors | Material composition, firing cycle, and furnace design. |
Need a porcelain furnace tailored to your specific needs? Contact us today to learn more!