The temperature of an induction furnace is a critical parameter that varies depending on the type of furnace, its design, and the materials being processed. Induction furnaces, particularly those using IGBT (Insulated Gate Bipolar Transistor) technology, are widely used in industries for melting metals and alloys due to their efficiency and precise temperature control. The temperature range of an induction furnace can vary significantly, typically from a few hundred degrees Celsius to over 2000°C, depending on the application and the material being melted.
Key Points Explained:
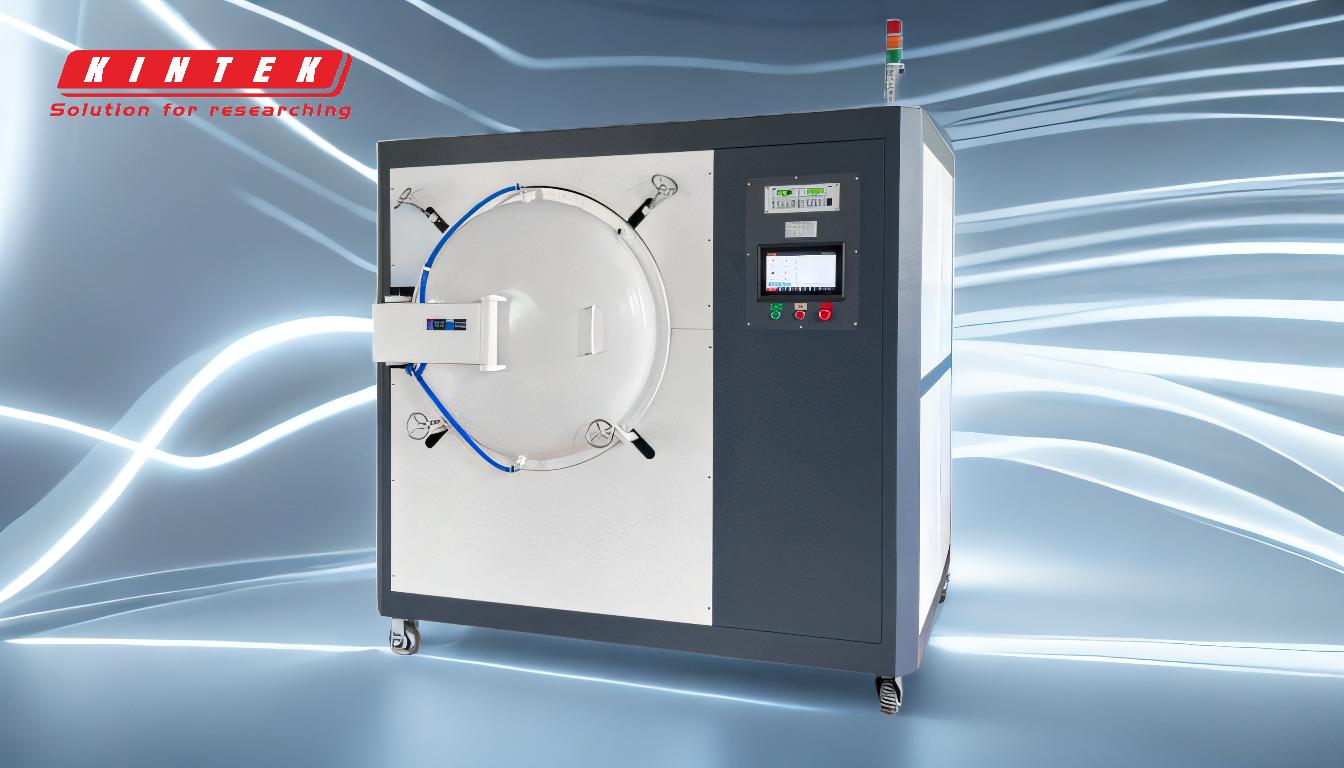
-
Temperature Range of Induction Furnaces:
- Induction furnaces can achieve a wide range of temperatures, typically from 500°C to over 2000°C.
- The exact temperature depends on the type of material being melted. For example, aluminum melts at around 660°C, while steel requires temperatures above 1500°C.
-
IGBT Induction Furnace Technology:
- IGBT induction furnaces are known for their high efficiency and precise temperature control.
- These furnaces use advanced power electronics to regulate the induction heating process, allowing for consistent and accurate temperature management.
-
Factors Influencing Temperature Control:
- Material Properties: The melting point of the material being processed directly influences the required furnace temperature.
- Furnace Design: The design of the furnace, including the coil configuration and cooling systems, affects its temperature capabilities and stability.
- Operational Parameters: Factors such as power input, frequency, and cooling efficiency play a significant role in maintaining the desired temperature.
-
Temperature Control Challenges:
- Chemical and Physical Influences: Over time, the temperature control in furnaces can be affected by chemical reactions and physical changes in the materials being processed.
- Soiling and Deposits: Residues from fired objects, such as ceramics, alloys, and soldering materials, can accumulate and affect the furnace's performance and temperature stability.
-
Applications of Induction Furnaces:
- Induction furnaces are used in various industries, including metallurgy, foundries, and dental laboratories.
- In dental applications, furnaces are used for firing ceramics and melting alloys, requiring precise temperature control to ensure the quality of the final product.
-
Maintenance and Calibration:
- Regular maintenance and calibration are essential to ensure the accurate and consistent performance of induction furnaces.
- Cleaning the furnace and removing deposits can help maintain optimal temperature control and extend the furnace's lifespan.
In summary, the temperature of an induction furnace, particularly an IGBT induction furnace, is highly variable and depends on the specific application and material being processed. Understanding the factors that influence temperature control and maintaining the furnace properly are crucial for achieving consistent and high-quality results.
Summary Table:
Aspect | Details |
---|---|
Temperature Range | 500°C to over 2000°C, depending on material and application. |
Material Influence | Aluminum melts at ~660°C; steel requires >1500°C. |
IGBT Technology | High efficiency and precise temperature control. |
Key Influencing Factors | Material properties, furnace design, and operational parameters. |
Applications | Metallurgy, foundries, dental labs (ceramics, alloys). |
Maintenance | Regular cleaning and calibration ensure consistent performance. |
Need precise temperature control for your applications? Contact our experts today to find the right induction furnace for your needs!