Biomass pyrolysis is a thermal decomposition process that occurs at specific temperature ranges, each yielding different primary products. The temperature of biomass pyrolysis typically ranges from below 200°C to over 800°C, depending on the desired end product. At lower temperatures (less than 450°C), the process primarily produces biochar, while intermediate temperatures (around 500-600°C) favor bio-oil production. High temperatures (greater than 800°C) with rapid heating rates result in the production of gases. The temperature also influences the breakdown of biomass components like hemicellulose, cellulose, and lignin, which decompose at specific temperature ranges. Fast pyrolysis, aimed at maximizing bio-oil yield, requires moderate temperatures (around 500°C), rapid heating, and short residence times.
Key Points Explained:
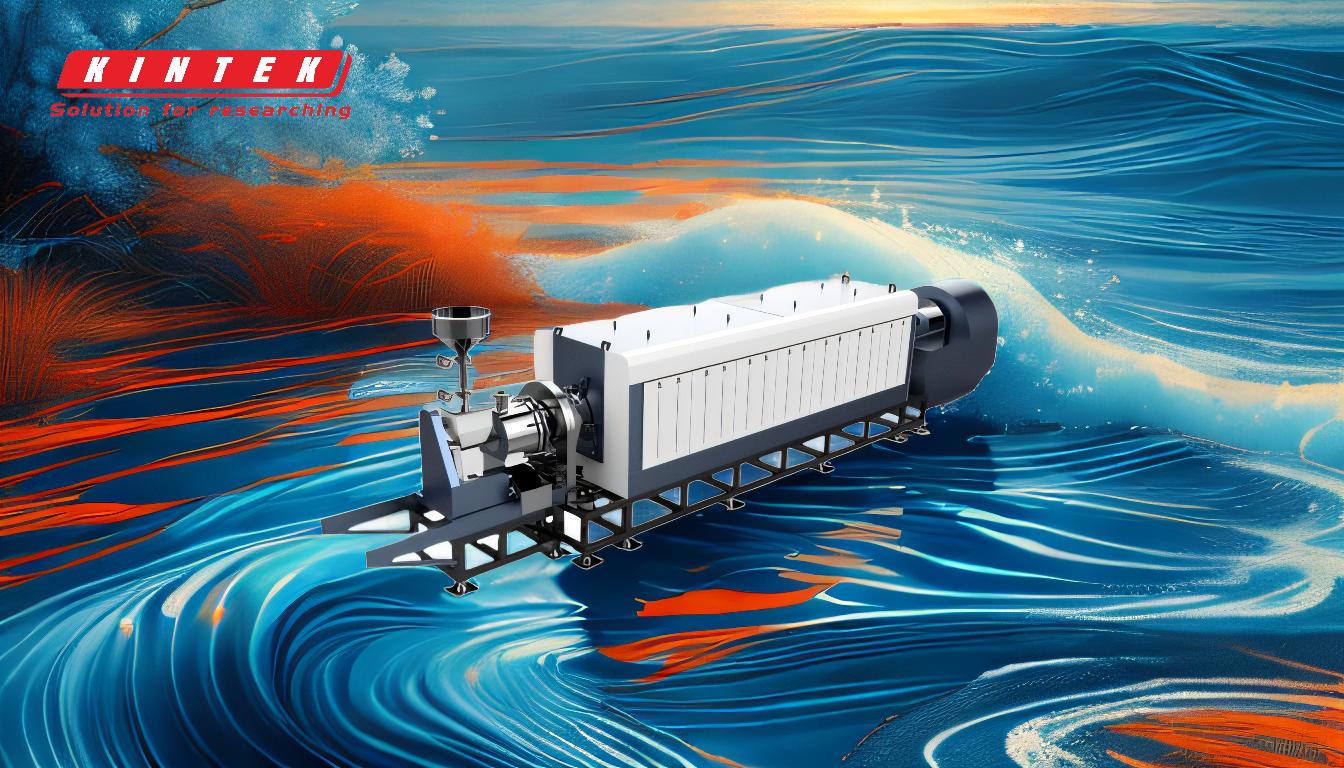
-
Temperature Ranges and Primary Products:
- Low Temperatures (<450°C): At these temperatures, pyrolysis primarily yields biochar, especially when combined with slow heating rates. This is due to the incomplete decomposition of biomass, leaving behind a solid carbon-rich residue.
- Intermediate Temperatures (450-600°C): This range is optimal for bio-oil production, particularly around 500°C. Fast pyrolysis techniques are often employed here to maximize bio-oil yield by ensuring rapid heating and short residence times.
- High Temperatures (>800°C): At these temperatures, pyrolysis mainly produces gases. Rapid heating rates further enhance gas production by breaking down biomass into smaller, volatile molecules.
-
Breakdown of Biomass Components:
- Below 200°C: Moisture content in the biomass evaporates, preparing the material for further thermal decomposition.
- 200-300°C: Hemicellulose, a major component of biomass, begins to break down, producing syn gases and bio-oil.
- 250-350°C: Cellulose decomposes, contributing to bio-oil production and initiating biochar formation.
- 300-500°C: Lignin, the most thermally stable component, breaks down, leading to significant biochar production.
-
Fast Pyrolysis for Bio-Oil Production:
- Optimal Temperature: Around 500°C is ideal for fast pyrolysis to maximize bio-oil yield.
- Heating Rate: Rapid heating of biomass particles is crucial to achieve the desired decomposition before secondary reactions occur.
- Residence Time: Short residence times for pyrolysis vapors help in preserving the bio-oil quality by minimizing further decomposition.
- Quenching: Fast quenching of pyrolysis vapors is necessary to condense the bio-oil efficiently, preventing its degradation into gases.
-
Economic Considerations:
- Bio-Oil Yield at 500-600°C: This temperature range not only maximizes bio-oil production but also reduces overall production costs, making it economically favorable for industrial applications.
-
Environmental and Process Control:
- Inert Atmosphere: Conducting pyrolysis in an inert atmosphere or vacuum helps avoid side reactions like combustion or hydrolysis, improving the recovery of desired byproducts.
- Exhaust Gas Treatment: De-dusting and cleaning exhaust gases are essential steps to reduce harmful substances and ensure environmental compliance.
By understanding these temperature ranges and their effects, purchasers of pyrolysis equipment and consumables can make informed decisions tailored to their specific production goals, whether for biochar, bio-oil, or gas.
Summary Table:
Temperature Range | Primary Product | Key Characteristics |
---|---|---|
<450°C | Biochar | Incomplete decomposition, carbon-rich residue |
450-600°C | Bio-oil | Optimal for fast pyrolysis, rapid heating, short residence |
>800°C | Gases | Rapid heating enhances gas production |
Biomass Breakdown | ||
<200°C | Moisture evaporation | Prepares biomass for decomposition |
200-300°C | Hemicellulose breakdown | Produces syn gases and bio-oil |
250-350°C | Cellulose breakdown | Contributes to bio-oil and biochar |
300-500°C | Lignin breakdown | Significant biochar production |
Ready to optimize your biomass pyrolysis process? Contact us today for expert guidance!