Fast pyrolysis is a thermal decomposition process of biomass conducted in the absence of oxygen, typically at moderate temperatures ranging from 400°C to 600°C. The process is characterized by high heating rates (10–200°C/s or higher) and short residence times (0.5–10 seconds). The primary goal of fast pyrolysis is to maximize the production of bio-oil, which can yield 50–70 wt% on a dry biomass basis. The temperature range is critical as it determines the distribution of products: bio-oil dominates at intermediate temperatures, while biochar and gases are favored at lower and higher temperatures, respectively. Optimal conditions for fast pyrolysis include a temperature of around 500°C, rapid heating rates, and quick quenching of vapors to condense bio-oil.
Key Points Explained:
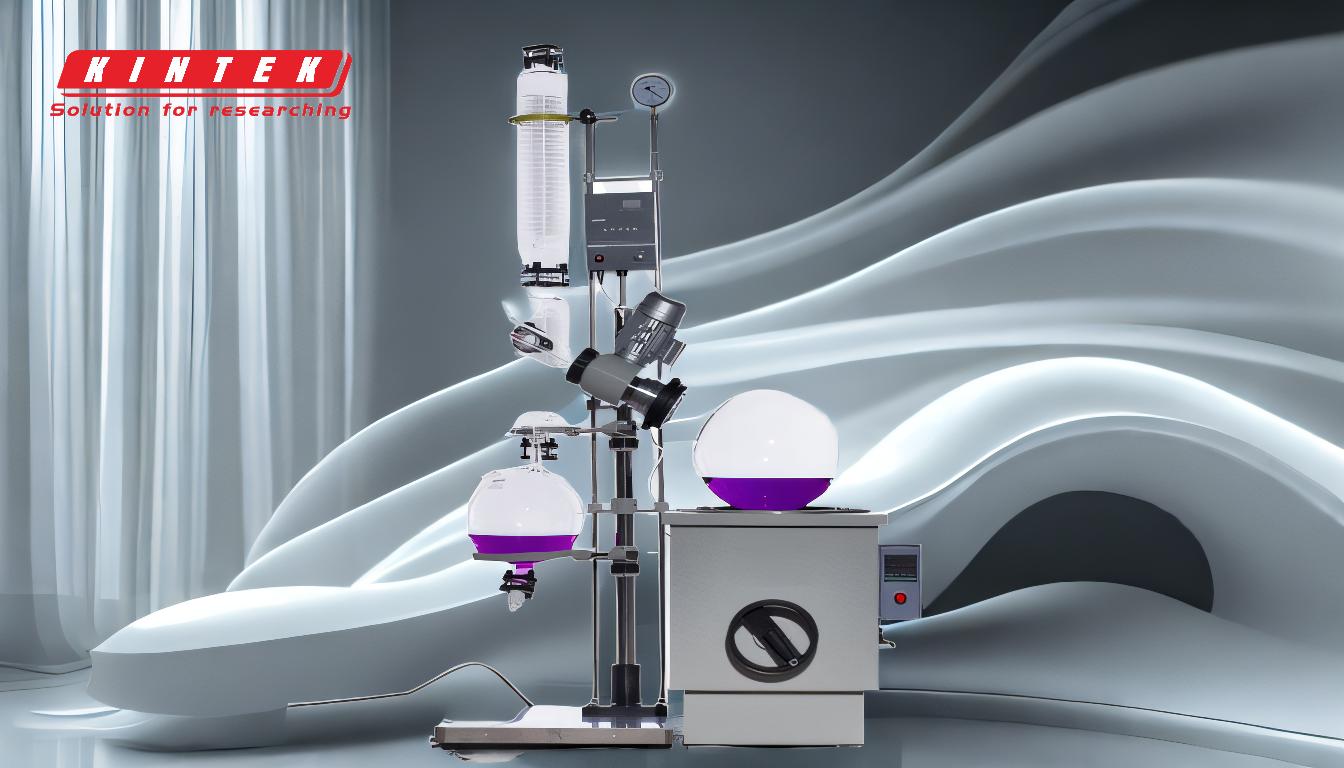
-
Temperature Range for Fast Pyrolysis:
- Fast pyrolysis operates within a moderate temperature range of 400–600°C.
- This range is optimal for maximizing bio-oil production, which is the primary target product.
- Temperatures below 450°C favor biochar formation, while temperatures above 800°C favor gas production.
-
Heating Rates:
- Fast pyrolysis requires high heating rates, typically between 10–200°C/s or even higher (e.g., 500–1000°C/s).
- Rapid heating ensures that biomass decomposes quickly, minimizing secondary reactions that could reduce bio-oil yield.
-
Residence Time:
- The residence time of biomass in the reactor is very short, typically 0.5–10 seconds.
- Short residence times prevent further decomposition of bio-oil into gases or char, ensuring high yields of the desired liquid product.
-
Product Distribution:
- At 400–600°C, the primary product is bio-oil, with yields ranging from 50–70 wt%.
- Secondary products include biochar (15–25 wt%) and syngas (10–15 wt%).
- The temperature directly influences the product distribution:
- Low temperatures (<450°C): Biochar is the dominant product.
- High temperatures (>800°C): Gases become the primary output.
-
Optimal Conditions for Bio-Oil Production:
- The optimal temperature for fast pyrolysis is around 500°C.
- High heating rates (e.g., 1000°C/s) and short residence times (<1 second) are critical.
- Rapid quenching of pyrolysis vapors is necessary to condense bio-oil and prevent its degradation.
-
Comparison with Other Pyrolysis Types:
- Slow Pyrolysis: Operates at lower temperatures (<450°C) with slow heating rates, producing mainly biochar.
- Flash Pyrolysis: Similar to fast pyrolysis but with even higher heating rates (10³–10⁴ °C/s) and shorter residence times (<1 second).
- Gasification: Occurs at very high temperatures (>800°C), primarily yielding syngas.
-
Practical Implications for Equipment Selection:
- Reactors for fast pyrolysis must withstand high temperatures (up to 600°C) and provide rapid heating.
- Systems must ensure short residence times and efficient vapor quenching to maximize bio-oil yields.
- Equipment should be designed to handle the corrosive nature of bio-oil and the abrasive properties of biomass feedstock.
-
Importance of Temperature Control:
- Precise temperature control is crucial to achieve the desired product distribution.
- Deviations from the optimal range can lead to suboptimal yields or undesired by-products.
- Advanced monitoring and control systems are recommended for maintaining consistent pyrolysis conditions.
By understanding these key points, equipment and consumable purchasers can make informed decisions about the design and operation of fast pyrolysis systems, ensuring optimal performance and product yields.
Summary Table:
Parameter | Details |
---|---|
Temperature Range | 400–600°C (optimal: ~500°C) |
Heating Rates | 10–200°C/s (up to 1000°C/s for optimal results) |
Residence Time | 0.5–10 seconds (shorter times maximize bio-oil yield) |
Primary Product | Bio-oil (50–70 wt%) |
Secondary Products | Biochar (15–25 wt%), syngas (10–15 wt%) |
Key Requirement | Rapid quenching of vapors to condense bio-oil |
Equipment Needs | High-temperature reactors, rapid heating, and efficient vapor quenching |
Optimize your fast pyrolysis process with expert guidance—contact us today!