Physical Vapor Deposition (PVD) coating is a process used to apply thin films of material onto a substrate, and the temperature during this process is a critical factor. The temperature of the substrate during PVD coating typically ranges between 200°C to 600°C (392°F to 1112°F), depending on the specific material and application. This range is significantly lower than other coating methods like Chemical Vapor Deposition (CVD), making PVD suitable for heat-sensitive materials. The temperature is carefully controlled to ensure the coating adheres well without damaging the substrate or altering its properties. Below is a detailed explanation of the key points related to PVD coating temperatures.
Key Points Explained:
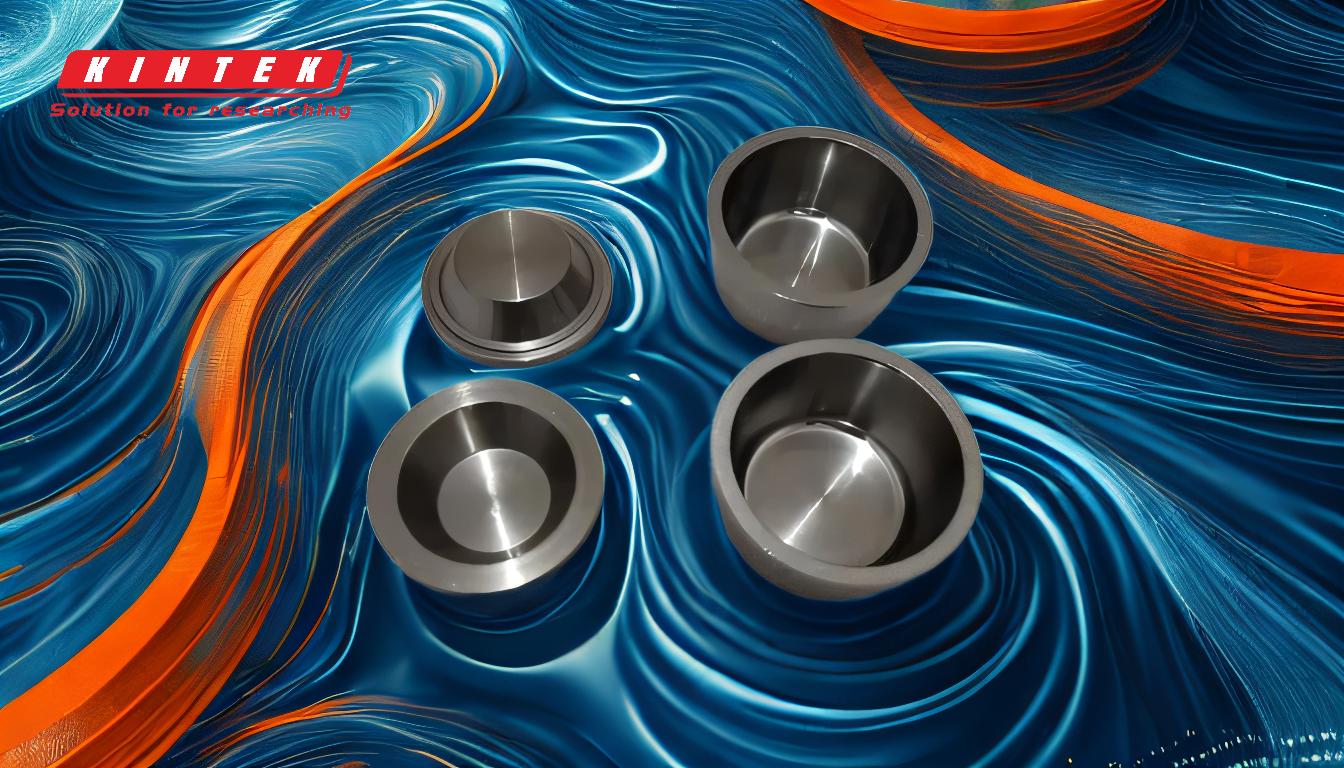
-
Typical Temperature Range for PVD Coating:
- The substrate temperature during PVD coating generally falls within 200°C to 600°C (392°F to 1112°F). This range is lower than CVD processes, which often require much higher temperatures.
- For heat-sensitive materials, such as plastics or certain alloys, the temperature can be controlled to as low as 50°F to 400°F (10°C to 204°C) to prevent distortion or damage.
-
Impact of Temperature on Substrate and Coating:
- Substrate Integrity: High temperatures can alter the hardness of the substrate or cause distortion. To mitigate this, heat-sensitive parts are often tempered at 900 to 950°F (482°C to 510°C) before coating.
- Coating Quality: The temperature must be optimized to ensure the coating adheres well and achieves the desired properties, such as hardness, corrosion resistance, and uniformity.
-
Comparison with Other Coating Methods:
- PVD operates at lower temperatures compared to CVD, making it suitable for materials that cannot withstand high heat, such as aluminum or certain plastics.
- The lower temperature range also reduces the risk of thermal stress or deformation in the substrate.
-
Material-Specific Temperature Considerations:
- Metals (e.g., Steel, Brass, Zinc): These materials can typically withstand higher temperatures, allowing for a broader range of coating options.
- Plastics: For plastic substrates, the temperature is kept below 400°F (204°C) to prevent melting or deformation.
- Aluminum: PVD coatings are generally unsuitable for aluminum due to its low melting point, which is close to the upper limit of PVD temperatures.
-
Advantages of PVD Coating Temperatures:
- High Purity and Uniformity: The controlled temperature ensures that the coating is applied evenly and adheres well to the substrate.
- Enhanced Properties: PVD coatings are known for their hardness, corrosion resistance, and durability, which are achieved without compromising the substrate's integrity.
-
Challenges and Limitations:
- Poor Coating Performance on Certain Areas: Due to the low air pressure in PVD processes, coatings may not perform well on the back or sides of tools.
- Temperature Sensitivity: The process requires precise temperature control to avoid damaging heat-sensitive substrates.
By understanding these key points, equipment and consumable purchasers can make informed decisions about the suitability of PVD coatings for their specific applications, ensuring optimal performance and longevity of the coated materials.
Summary Table:
Key Aspect | Details |
---|---|
Typical Temperature Range | 200°C to 600°C (392°F to 1112°F) |
Heat-Sensitive Materials | 50°F to 400°F (10°C to 204°C) |
Substrate Integrity | Tempered at 900 to 950°F (482°C to 510°C) before coating |
Coating Quality | Ensures hardness, corrosion resistance, and uniformity |
Comparison with CVD | Lower temperatures, suitable for heat-sensitive materials |
Material-Specific Temperatures | Metals: higher temps; Plastics: <400°F; Aluminum: generally unsuitable |
Advantages | High purity, uniformity, and enhanced properties |
Challenges | Poor coating on certain areas; requires precise temperature control |
Discover how PVD coating can enhance your material performance—contact our experts today!