The temperature of the Physical Vapor Deposition (PVD) process typically ranges from 200°C to 450°C, depending on the substrate material and specific application. This range is significantly lower than that of Chemical Vapor Deposition (CVD), which operates at temperatures above 900°C. The PVD process involves vaporizing a solid material in a vacuum environment and depositing it onto a substrate, which can be made of materials like zinc, brass, steel, or plastic. The relatively low temperatures in PVD make it suitable for coating temperature-sensitive materials without causing thermal damage.
Key Points Explained:
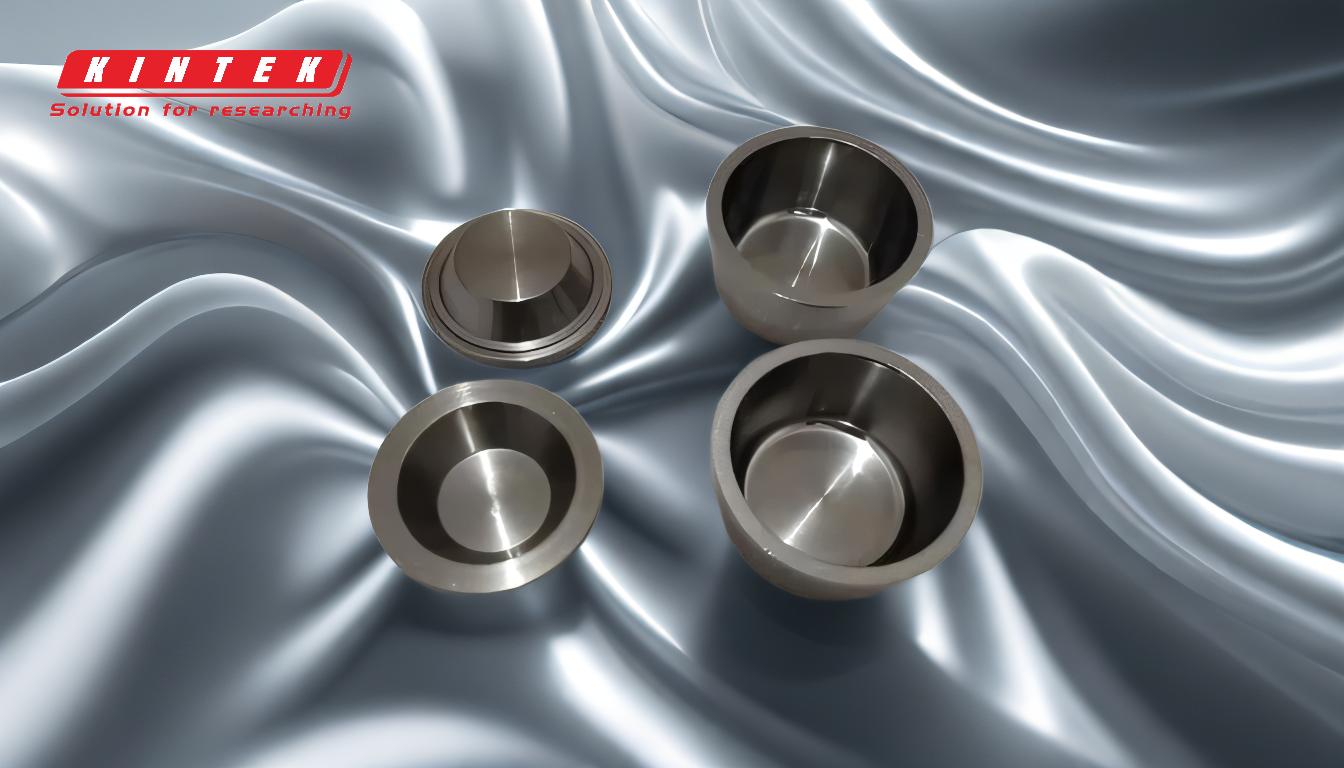
-
Temperature Range of PVD Process:
- The PVD process typically operates at temperatures between 200°C and 450°C. This range is lower compared to CVD, which requires temperatures above 900°C.
- The exact temperature depends on the substrate material and the specific PVD technique used.
-
Comparison with CVD:
- PVD operates at lower temperatures (200-450°C) because it involves vaporizing a solid material using plasma, which does not require high heat.
- CVD, on the other hand, requires higher temperatures (600-1100°C) because it involves heating gases to react with the substrate.
-
Substrate Material Influence:
- The substrate material (e.g., zinc, brass, steel, or plastic) plays a significant role in determining the process temperature. For instance:
- Plastic substrates may require lower temperatures (closer to 200°C) to avoid thermal damage.
- Metal substrates like steel or brass can withstand higher temperatures (up to 400°C or 450°C).
- The substrate material (e.g., zinc, brass, steel, or plastic) plays a significant role in determining the process temperature. For instance:
-
Advantages of Lower Temperatures:
- The lower temperatures in PVD make it suitable for coating temperature-sensitive materials like plastics or certain alloys.
- It reduces the risk of thermal distortion or degradation of the substrate material.
-
Process Flexibility:
- PVD allows for temperature control within a wide range (50°F to 400°F or 200°C to 450°C), making it adaptable to various applications and materials.
- This flexibility is particularly useful in industries like electronics, automotive, and medical devices, where precise temperature control is critical.
-
Energy Efficiency:
- Operating at lower temperatures makes PVD more energy-efficient compared to CVD, which requires significant energy to achieve and maintain high temperatures.
-
Applications of PVD:
- PVD is widely used in industries requiring durable coatings (e.g., wear resistance, corrosion protection) on temperature-sensitive substrates.
- Examples include coating cutting tools, optical lenses, and medical implants.
By understanding these key points, a purchaser can make informed decisions about selecting PVD equipment or coatings based on the specific temperature requirements of their substrates and applications.
Summary Table:
Aspect | Details |
---|---|
PVD Temperature Range | 200°C to 450°C |
CVD Temperature Range | Above 900°C |
Substrate Materials | Zinc, brass, steel, plastic |
Key Advantages | Lower temperatures, energy efficiency, suitable for sensitive materials |
Applications | Cutting tools, optical lenses, medical implants |
Need PVD solutions for your temperature-sensitive materials? Contact our experts today!