Pyrolysis is a thermal decomposition process that breaks down organic materials in the absence of oxygen, producing a range of products including solids (char, coke, or biochar), liquids (pyrolysis oil, tar, or bio-oil), and gases (non-condensable gases like hydrogen, methane, and carbon monoxide). The temperature of pyrolysis products varies depending on the stage of the process, the type of feedstock, and the specific pyrolysis conditions (e.g., slow, fast, or flash pyrolysis). Generally, pyrolysis occurs at temperatures ranging from 300°C to 900°C, with the resulting products exiting the reactor at temperatures close to the pyrolysis temperature. The gases and vapors produced are often cooled to condense the liquid products, while the solid residues and non-condensable gases remain at elevated temperatures.
Key Points Explained:
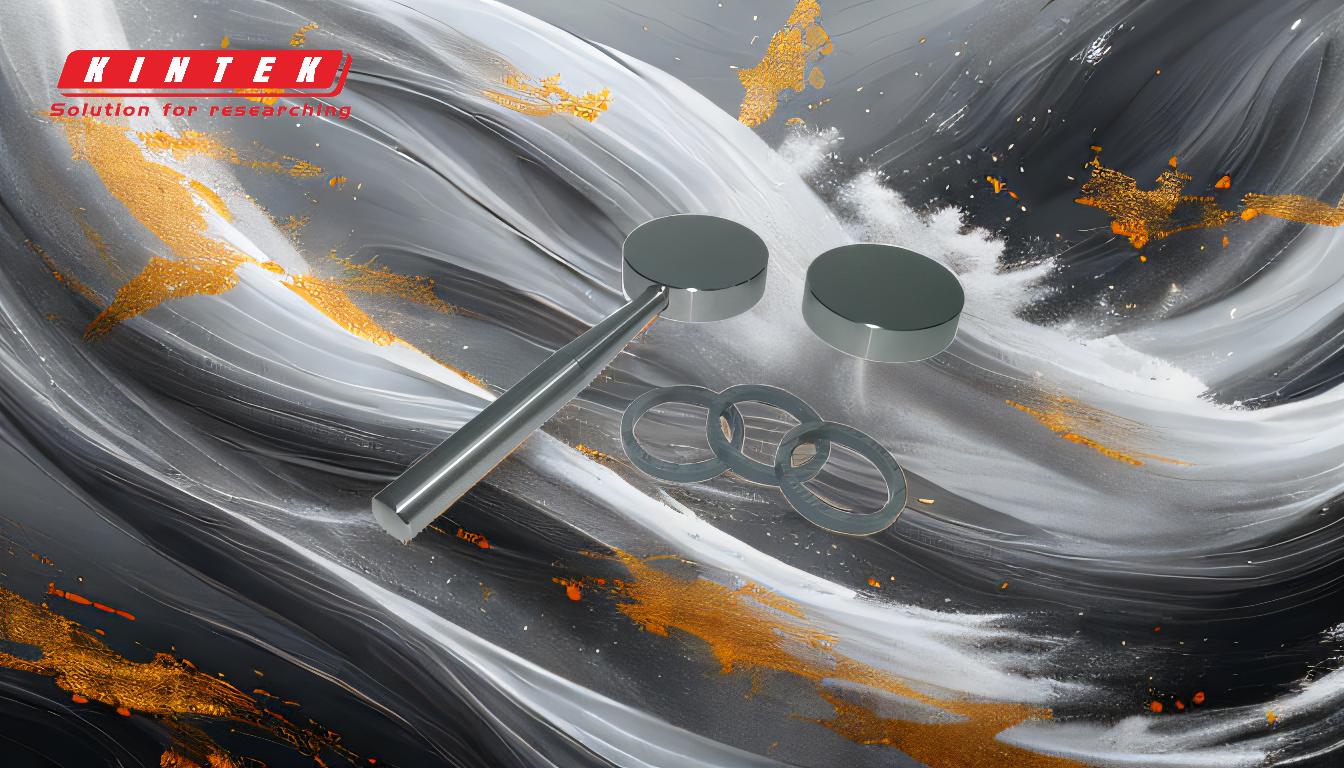
-
Pyrolysis Process and Temperature Range:
- Pyrolysis typically occurs at temperatures between 300°C and 900°C, depending on the feedstock and desired products.
- At lower temperatures (300°C–500°C), the process favors the production of char and bio-oil, while higher temperatures (600°C–900°C) increase the yield of gases.
- The temperature of pyrolysis products (solids, liquids, and gases) is initially close to the reactor temperature but may vary during subsequent cooling and separation processes.
-
Solid Products (Char, Coke, Biochar):
- Solid residues like char, coke, or biochar are formed during pyrolysis and are typically rich in carbon.
- These solids exit the reactor at temperatures close to the pyrolysis temperature (300°C–900°C) and are often cooled for storage or further processing.
- Char and biochar are used in applications such as soil amendment, energy production, and sorbents.
-
Liquid Products (Pyrolysis Oil, Tar, Bio-Oil):
- Liquid products, including pyrolysis oil, tar, and bio-oil, are formed from the condensation of vapors produced during pyrolysis.
- These vapors are cooled to temperatures below 100°C to condense into liquids, which can then be collected and stored.
- Pyrolysis oil is a valuable product used as an alternative fuel or refined into chemicals and biodiesel.
-
Non-Condensable Gases (Syn-Gas, Hydrogen, Methane):
- Non-condensable gases, such as hydrogen (H2), methane (CH4), carbon monoxide (CO), and carbon dioxide (CO2), are produced during pyrolysis.
- These gases exit the reactor at high temperatures (close to the pyrolysis temperature) and are often used to generate heat energy for the pyrolysis process itself.
- In some cases, the hot syngas is directly fed into burners or oxidation chambers without cooling.
-
Temperature Variations Based on Feedstock:
- The type of feedstock (e.g., tires, plastics, biomass) influences the temperature and composition of pyrolysis products.
- For example, tire pyrolysis yields 35–45% oil, 30–35% carbon black, and 8–15% syn-gas, with the oil condensing at lower temperatures.
- Biomass pyrolysis, on the other hand, produces biochar, bio-oil, and gases, with the oil condensing at similar temperatures but differing in composition.
-
Cooling and Separation of Products:
- After pyrolysis, the products undergo cooling and separation processes to isolate solids, liquids, and gases.
- Gases and vapors are cooled to condense the liquid phase, while solids are separated and cooled for storage or further use.
- The cooling process ensures that the liquid products are collected efficiently and the gases are ready for energy recovery or other applications.
-
Applications and Industrial Relevance:
- Pyrolysis products have diverse applications, including energy production, chemical synthesis, and soil amendment.
- The ability to convert waste materials into valuable products makes pyrolysis an increasingly important process in industries focused on sustainability and resource recovery.
By understanding the temperature ranges and characteristics of pyrolysis products, purchasers of equipment and consumables can make informed decisions about the design and operation of pyrolysis systems to optimize product yields and quality.
Summary Table:
Product Type | Temperature Range | Key Characteristics | Applications |
---|---|---|---|
Solid (Char, Coke, Biochar) | 300°C–900°C | Rich in carbon, exits reactor at pyrolysis temperature, often cooled for storage. | Soil amendment, energy production, sorbents. |
Liquid (Pyrolysis Oil, Tar, Bio-Oil) | Below 100°C (condensed) | Formed from vapor condensation, collected and stored. | Alternative fuel, chemical synthesis, biodiesel. |
Non-Condensable Gases (Syn-Gas, H2, CH4) | Close to pyrolysis temperature | Exits reactor hot, used for heat energy or fed into burners. | Energy recovery, chemical feedstock. |
Feedstock Variations | 300°C–900°C | Influenced by feedstock type (e.g., tires, plastics, biomass). | Determines product composition and yield. |
Optimize your pyrolysis process with expert insights—contact us today for tailored solutions!