The temperature of a muffle oven depends on its design, heating elements, and control system. Most muffle furnaces operate within a range of 1000°C to 1200°C when equipped with metallic wire heating elements, while advanced models with silicon carbide or molybdenum disilicide heating elements can reach up to 1600°C or 1800°C, respectively. The temperature control system employs intelligent PID regulation, allowing for precise adjustments and up to 30 stages of temperature rise and fall programs. Proper setup and monitoring are essential for achieving optimal results.
Key Points Explained:
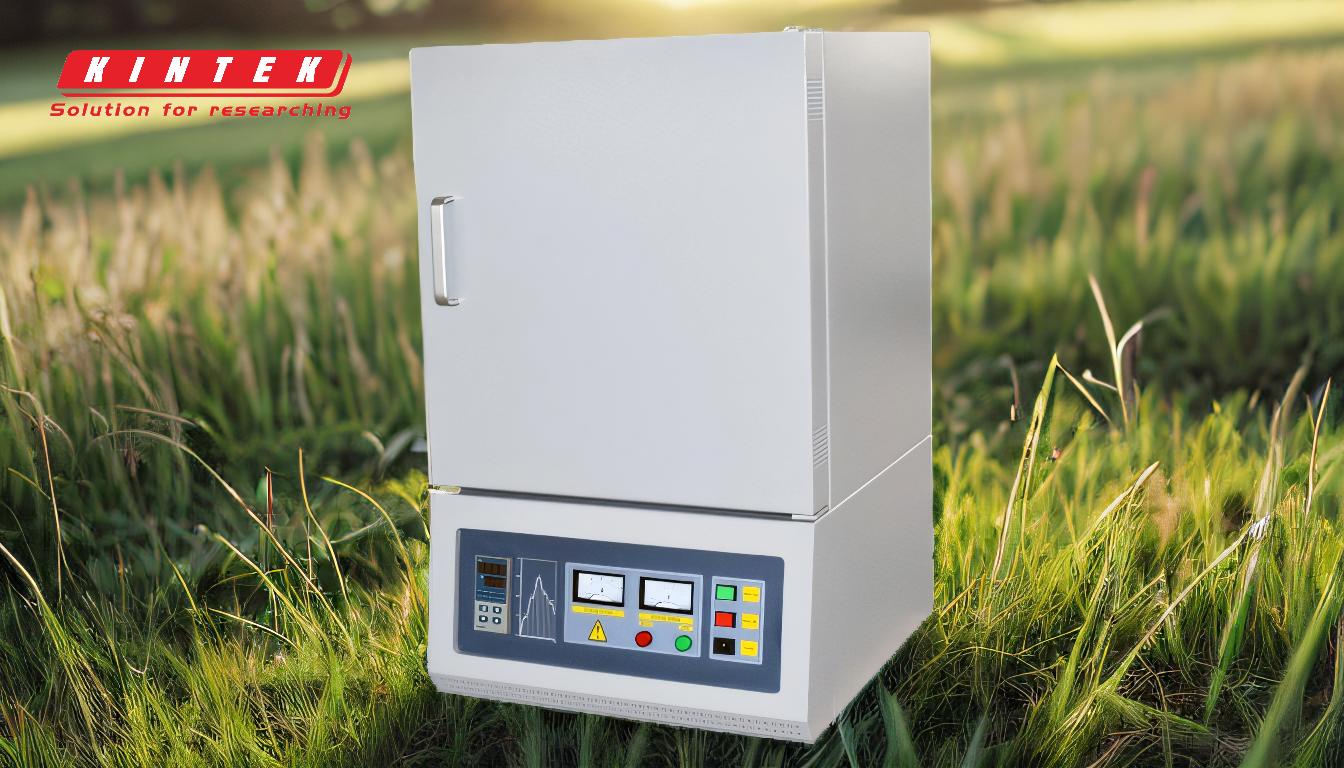
-
Temperature Range of Muffle Furnaces:
- The maximum temperature of a muffle furnace depends on the type of heating elements used.
- Metallic wire heating elements: These are the most common and typically support temperatures between 1000°C and 1200°C.
- Silicon carbide heating elements: These can achieve higher temperatures, up to 1600°C.
- Molybdenum disilicide heating elements: These are capable of reaching the highest temperatures, up to 1800°C.
- The choice of heating elements determines the furnace's suitability for specific applications, such as high-temperature material testing or heat treatment.
- The maximum temperature of a muffle furnace depends on the type of heating elements used.
-
Temperature Control System:
- Muffle furnaces use an intelligent PID (Proportional-Integral-Derivative) regulation system for precise temperature control.
- The system can be programmed for up to 30 stages of temperature rise and fall, allowing for complex heating and cooling cycles.
- The control system adjusts the heat source energy based on the deviation between the actual furnace temperature and the desired temperature. This ensures stability and accuracy within a specified range.
-
Automatic Temperature Control Principles:
- The system operates on a feedback loop, continuously comparing the actual temperature with the target temperature.
- Based on the deviation, the system adjusts the heat source energy by turning it on/off or modulating its power.
- Common control methods include:
- Two-position or three-position control: Simple on/off or intermediate states.
- Proportional control: Adjusts heat output proportionally to the deviation.
- Proportional-Integral (PI) and Proportional-Integral-Derivative (PID) control: These methods provide more precise and stable temperature regulation by accounting for past and future deviations.
-
Key Considerations for Temperature Setting:
- Preparation: Ensure the furnace is clean and free of debris before starting.
- Precise Adjustment: Follow the user manual for specific instructions on setting the desired temperature and programming stages.
- Continuous Monitoring: Regularly check the furnace temperature and make adjustments as needed to maintain stability.
- Energy Efficiency: The intelligent PID system and balanced temperature field contribute to energy savings while maintaining performance.
-
Applications and Suitability:
- The temperature range and control capabilities make muffle furnaces suitable for a variety of applications, including:
- Material testing (e.g., ash content determination, thermal analysis).
- Heat treatment processes (e.g., annealing, sintering).
- High-temperature research and experiments.
- Selecting the right furnace with the appropriate heating elements and temperature range is crucial for achieving accurate and reliable results.
- The temperature range and control capabilities make muffle furnaces suitable for a variety of applications, including:
By understanding these key points, users can effectively operate a muffle furnace, ensuring precise temperature control and optimal performance for their specific needs.
Summary Table:
Heating Element | Temperature Range |
---|---|
Metallic Wire | 1000°C - 1200°C |
Silicon Carbide | Up to 1600°C |
Molybdenum Disilicide | Up to 1800°C |
Control System | Features |
---|---|
PID Regulation | Precise adjustments |
Up to 30 Stages | Complex heating cycles |
Feedback Loop | Stable temperature |
Need a muffle oven with precise temperature control? Contact us today to find the perfect solution for your lab!