Biomass pyrolysis operates within a temperature range that typically spans from below 200°C to over 800°C, depending on the desired end product. At lower temperatures (below 450°C), slow pyrolysis primarily produces biochar, while at higher temperatures (above 800°C), fast pyrolysis yields gases. Intermediate temperatures (around 500-600°C) with high heating rates are optimal for bio-oil production. The process is influenced by factors such as biomass type, moisture content, particle size, and heating rate. Understanding these temperature ranges and their effects is crucial for optimizing pyrolysis processes to achieve desired outputs like biochar, bio-oil, or gases.
Key Points Explained:
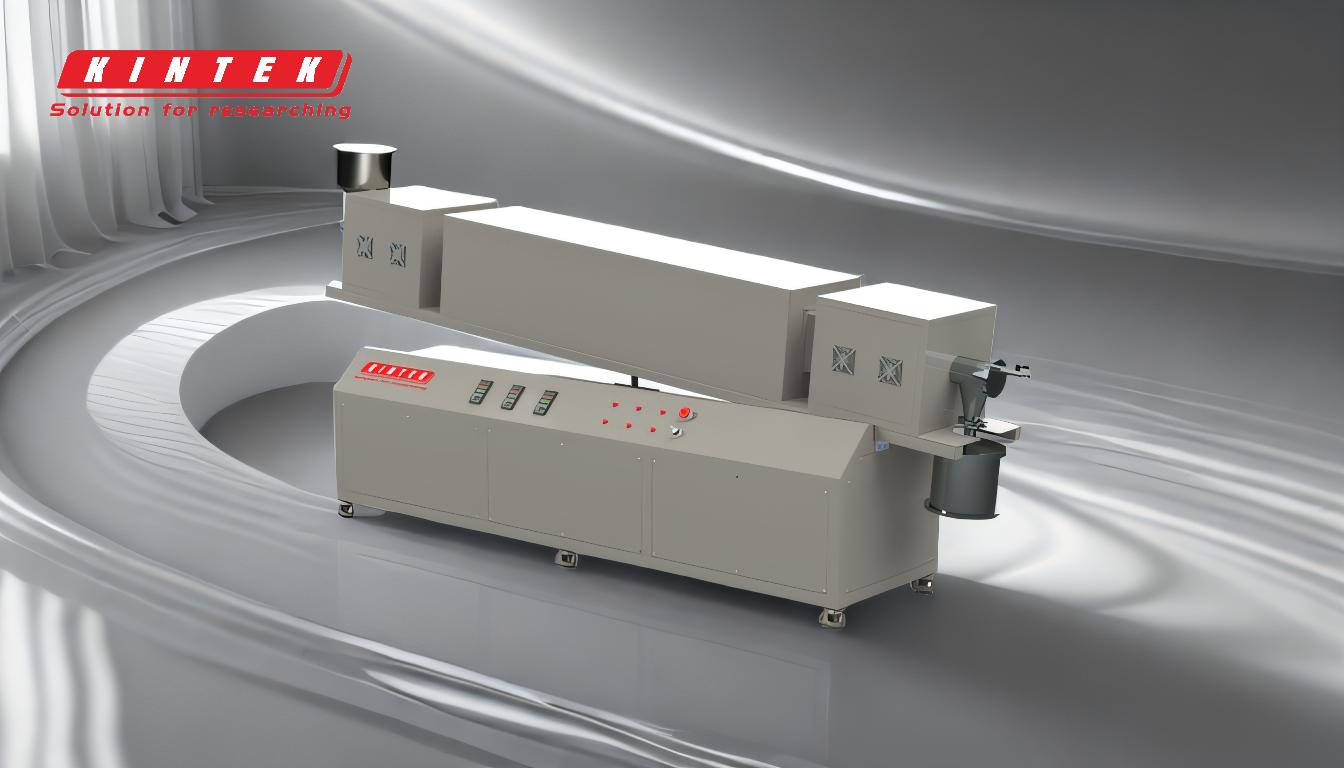
-
Temperature Ranges and Their Effects on Pyrolysis Products
- Below 200°C: Moisture content in the biomass evaporates, preparing the feedstock for further thermal decomposition.
- 200-300°C: Hemicellulose breaks down, producing syn gases and bio-oil.
- 250-350°C: Cellulose decomposes, leading to bio-oil formation and the initiation of biochar production.
- 300-500°C: Lignin breaks down, primarily producing biochar.
- 500-600°C: Optimal range for maximizing bio-oil yield, which is cost-effective for industrial applications.
- Above 800°C: High temperatures with rapid heating rates favor gas production, such as syngas.
-
Influence of Heating Rate
- Slow heating rates at lower temperatures (below 450°C) promote biochar formation due to prolonged thermal exposure.
- Fast heating rates at intermediate temperatures (500-600°C) enhance bio-oil production by minimizing secondary reactions.
- Rapid heating at high temperatures (above 800°C) shifts the process toward gasification, producing syngas.
-
Role of Biomass Properties
- Moisture Content: Biomass should ideally have a moisture content of around 10%. High-moisture feedstocks, such as sludge, require pre-drying to ensure efficient pyrolysis.
- Particle Size: Smaller particle sizes (typically less than 2 mm) improve heat transfer and reaction rates, which are critical for optimizing product yields.
- Biomass Composition: The proportions of hemicellulose, cellulose, and lignin in the feedstock influence the breakdown temperatures and product distribution.
-
Operational and Design Considerations
- Reactor Design: Optimizing reactor configurations, such as fluidized bed or fixed bed reactors, can enhance heat transfer and product yields.
- Residence Time: Controlling the time biomass spends in the pyrolysis furnace is essential for achieving the desired product mix.
- Pressure: While not explicitly detailed in the references, maintaining appropriate pressure conditions can influence reaction kinetics and product quality.
-
Economic and Efficiency Implications
- Producing bio-oil at 500-600°C reduces overall production costs due to its higher yield and energy density.
- Optimizing temperature and heating rates minimizes energy losses and maximizes the efficiency of the pyrolysis process.
- Tailoring the process to specific biomass types and conditions ensures cost-effective and sustainable production of desired outputs.
By carefully controlling these factors, biomass pyrolysis can be fine-tuned to produce biochar, bio-oil, or gases, depending on the intended application and economic objectives.
Summary Table:
Temperature Range | Primary Product | Key Process |
---|---|---|
Below 200°C | Moisture Evaporation | Prepares feedstock for decomposition |
200-300°C | Syn gases, Bio-oil | Hemicellulose breakdown |
250-350°C | Bio-oil, Biochar | Cellulose decomposition |
300-500°C | Biochar | Lignin breakdown |
500-600°C | Bio-oil | Optimal for industrial applications |
Above 800°C | Gases (e.g., syngas) | Fast pyrolysis for gasification |
Ready to optimize your biomass pyrolysis process? Contact our experts today for tailored solutions!