Gasification is a thermochemical process that converts carbonaceous materials, such as coal, biomass, or waste, into a mixture of gases known as syngas (synthesis gas). This process occurs in a high-temperature, oxygen-limited environment, where the feedstock undergoes partial oxidation, pyrolysis, and reduction reactions. The resulting syngas primarily consists of carbon monoxide (CO), hydrogen (H₂), and smaller amounts of methane (CH₄) and carbon dioxide (CO₂). Gasification is widely used for energy production, chemical synthesis, and waste management, offering a cleaner and more efficient alternative to direct combustion.
Key Points Explained:
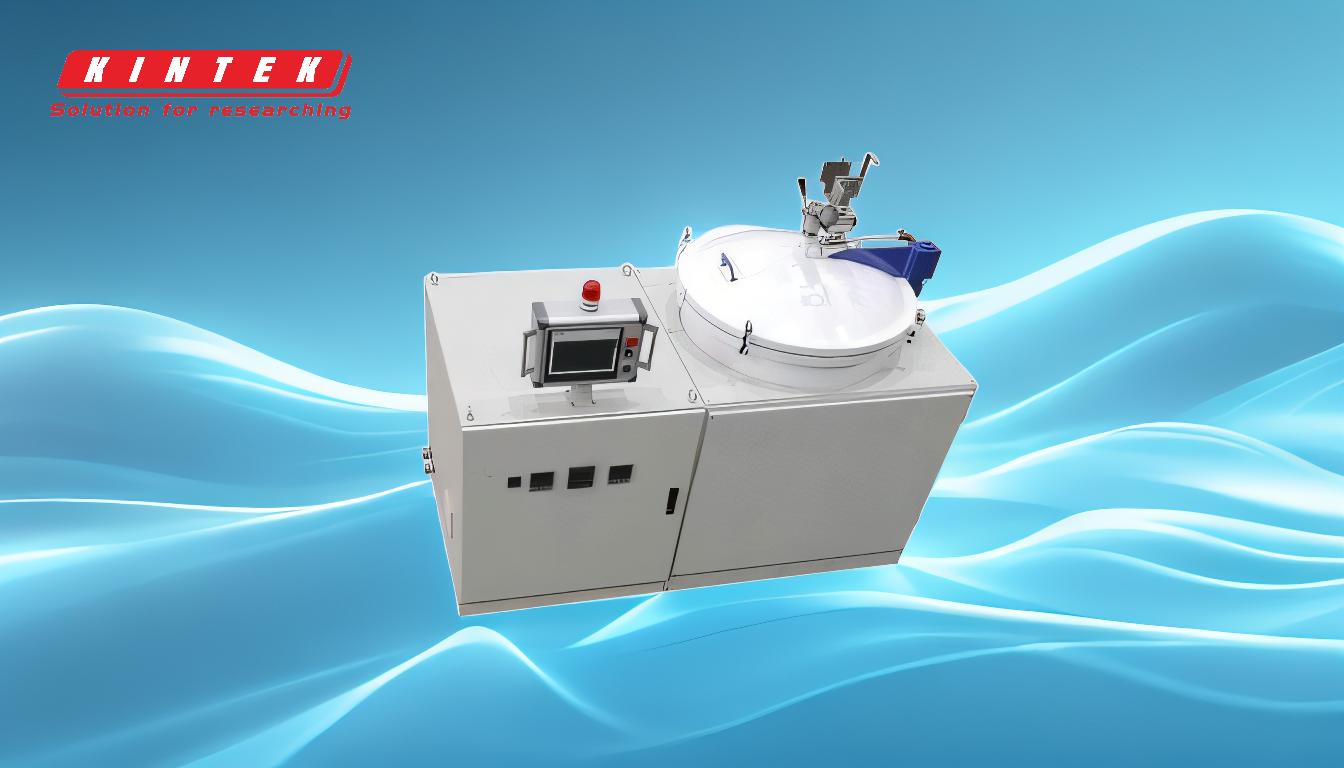
-
Definition and Purpose of Gasification:
- Gasification is a process that transforms solid or liquid carbon-based materials into a gaseous fuel (syngas) through controlled thermal decomposition.
- The primary purpose is to produce a versatile fuel that can be used for electricity generation, heating, or as a precursor for chemical synthesis.
-
Key Chemical Reactions in Gasification:
- Partial Oxidation: The feedstock reacts with a limited supply of oxygen or air, producing carbon monoxide and heat. [ \text{C} + \frac{1}{2}\text{O}_2 \rightarrow \text{CO} + \text{Heat} ]
- Pyrolysis: In the absence of oxygen, the feedstock thermally decomposes into volatile gases, tar, and char. [ \text{Feedstock} \rightarrow \text{Volatiles} + \text{Char} + \text{Tar} ]
- Reduction: Carbon dioxide and water vapor react with the char to produce carbon monoxide and hydrogen. [ \text{C} + \text{CO}_2 \rightarrow 2\text{CO} ] [ \text{C} + \text{H}_2\text{O} \rightarrow \text{CO} + \text{H}_2 ]
-
Types of Gasifiers:
- Fixed-Bed Gasifiers: These include updraft and downdraft designs, suitable for small-scale applications.
- Fluidized-Bed Gasifiers: Provide better mixing and heat transfer, ideal for heterogeneous feedstocks like biomass.
- Entrained-Flow Gasifiers: Operate at high temperatures and pressures, suitable for large-scale industrial applications.
-
Applications of Gasification:
- Energy Production: Syngas can be burned directly in turbines or engines to generate electricity.
- Chemical Synthesis: Syngas is a precursor for producing methanol, ammonia, and synthetic fuels.
- Waste Management: Gasification can convert municipal solid waste into energy while reducing landfill use.
-
Advantages of Gasification:
- Efficiency: Higher thermal efficiency compared to direct combustion.
- Environmental Benefits: Lower emissions of pollutants like sulfur oxides (SOₓ) and nitrogen oxides (NOₓ).
- Versatility: Can process a wide range of feedstocks, including low-grade coal and waste materials.
-
Challenges and Limitations:
- Complexity: Requires precise control of temperature, pressure, and feedstock composition.
- Tar Formation: Tars can clog equipment and reduce efficiency, necessitating advanced cleanup systems.
- Capital Costs: High initial investment for gasification plants and associated infrastructure.
-
Future Trends in Gasification:
- Integration with carbon capture and storage (CCS) to further reduce greenhouse gas emissions.
- Development of advanced gasifiers capable of handling diverse and low-quality feedstocks.
- Increased use of biomass gasification for renewable energy production.
By understanding the theory and applications of gasification, stakeholders can make informed decisions about its implementation for energy and environmental solutions.
Summary Table:
Aspect | Details |
---|---|
Definition | Converts carbonaceous materials into syngas (CO, H₂, CH₄, CO₂) in a high-temperature, oxygen-limited environment. |
Key Reactions | Partial Oxidation, Pyrolysis, Reduction. |
Types of Gasifiers | Fixed-Bed, Fluidized-Bed, Entrained-Flow. |
Applications | Energy production, chemical synthesis, waste management. |
Advantages | High efficiency, lower emissions, versatile feedstock processing. |
Challenges | Complexity, tar formation, high capital costs. |
Future Trends | Integration with CCS, advanced gasifiers, biomass gasification. |
Discover how gasification can transform your energy and waste management strategies—contact us today!