Physical Vapor Deposition (PVD) is a process used to deposit thin films of material onto a substrate by transitioning the material from a solid to a vapor phase and then condensing it back into a solid form on the substrate. This process is typically carried out in a vacuum chamber to minimize contamination and ensure a controlled environment. PVD is widely used in industries such as electronics, optics, and manufacturing due to its ability to produce highly durable, corrosion-resistant, and temperature-tolerant coatings. The process involves several key steps: vaporization of the target material, transportation of the vapor through the chamber, and condensation onto the substrate. PVD methods include thermal evaporation, sputtering, and arc discharge, each offering unique advantages depending on the application.
Key Points Explained:
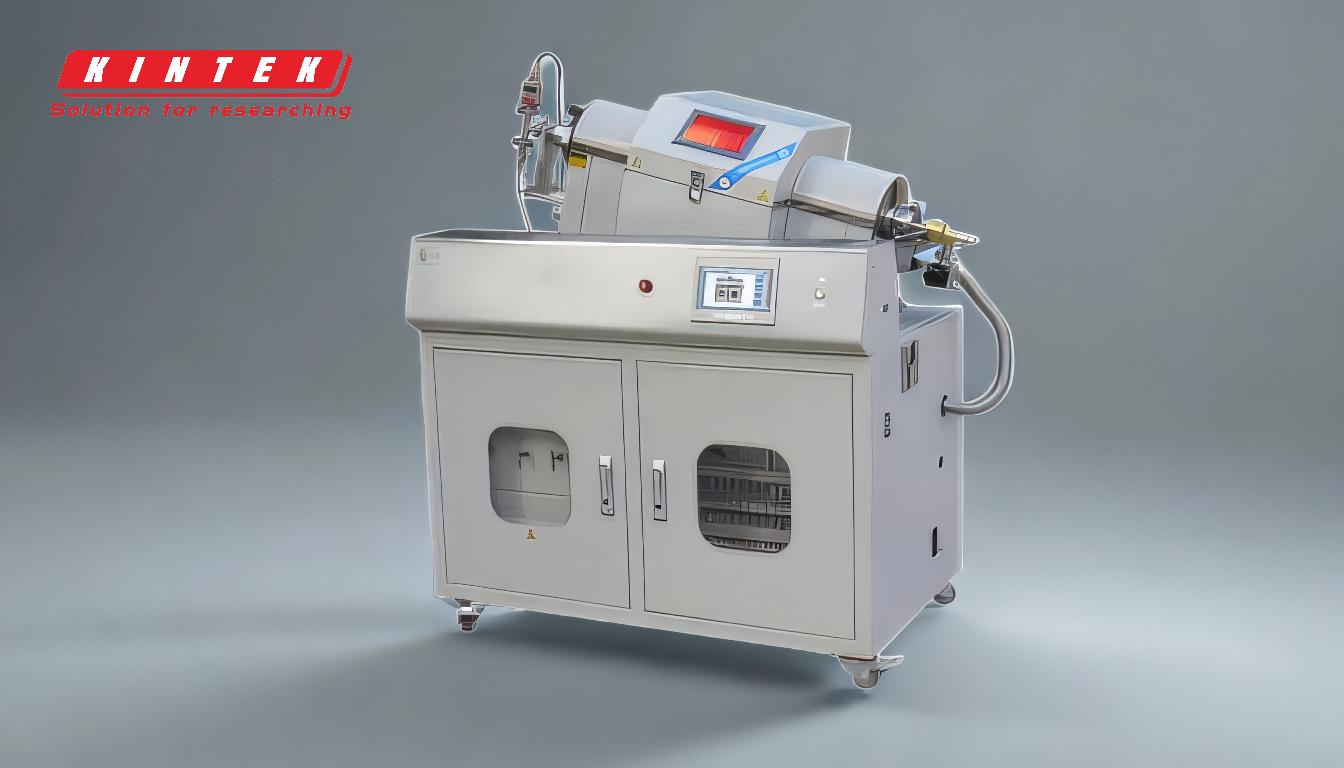
-
Transition from Solid to Vapor Phase:
- The core principle of PVD is the conversion of a solid target material into a vapor phase. This is achieved through various methods such as thermal evaporation, sputtering, or arc discharge. The target material is typically a metal or ceramic, chosen based on the desired properties of the final coating.
- Thermal Evaporation: Involves heating the target material until it evaporates. This method is often used for materials with relatively low melting points.
- Sputtering: Uses high-energy particles (usually argon ions) to knock atoms off the target material, creating a vapor. This method is suitable for materials with high melting points.
- Arc Discharge: Involves creating an electric arc that vaporizes the target material. This method is particularly effective for depositing hard coatings like titanium nitride.
-
Transportation of Vapor in a Vacuum Chamber:
- Once the target material is vaporized, the vapor is transported through a vacuum chamber. The vacuum environment is crucial as it minimizes the presence of contaminants and ensures that the vapor travels in a straight line (line-of-sight) to the substrate.
- The vacuum chamber is typically maintained at a temperature between 50 to 600 degrees Celsius, depending on the specific requirements of the coating process.
-
Condensation on the Substrate:
- The vaporized material travels through the chamber and condenses onto the substrate, forming a thin film. The substrate can be made of various materials, including metals, ceramics, or polymers, depending on the application.
- The condensation process results in a coating that is highly adherent and uniform. The thin films produced by PVD are often only a few nanometers to micrometers thick, making them ideal for applications requiring precision and durability.
-
Types of PVD Methods:
- Thermal Evaporation: This method involves heating the target material until it evaporates. The vapor then condenses on the substrate. It is commonly used for depositing metals like aluminum and gold.
- Sputtering: In this method, high-energy particles bombard the target material, causing atoms to be ejected and deposited onto the substrate. Sputtering is versatile and can be used for a wide range of materials, including metals, alloys, and ceramics.
- Arc Discharge: This method uses an electric arc to vaporize the target material. It is particularly effective for depositing hard coatings like titanium nitride, which are used in cutting tools and wear-resistant applications.
-
Advantages of PVD:
- High Adhesion: PVD coatings are known for their excellent adhesion to the substrate, which is crucial for applications requiring durability and resistance to wear and tear.
- Material Versatility: PVD can be used to deposit a wide range of materials, including metals, ceramics, and even some polymers. This makes it a versatile technique for various industrial applications.
- High-Temperature Resistance: PVD coatings can withstand high temperatures, making them suitable for use in harsh environments, such as in aerospace or automotive applications.
- Corrosion Resistance: The coatings produced by PVD are highly resistant to corrosion, which is essential for applications exposed to corrosive environments, such as marine or chemical processing industries.
-
Applications of PVD:
- Electronics: PVD is used to deposit thin films in the manufacturing of semiconductors, solar panels, and displays. The precision and uniformity of PVD coatings are critical for the performance of electronic components.
- Optics: PVD is employed to create reflective and anti-reflective coatings on lenses, mirrors, and other optical components. These coatings enhance the performance and durability of optical devices.
- Manufacturing: PVD is widely used in the production of cutting tools, molds, and wear-resistant components. The hard coatings produced by PVD extend the lifespan of these tools and improve their performance.
-
Challenges and Considerations:
- Complexity of the Process: PVD requires specialized equipment and a controlled environment, which can be costly and complex to set up and maintain.
- Material Limitations: While PVD is versatile, not all materials are suitable for deposition using this method. Some materials may require specific conditions or alternative deposition techniques.
- Uniformity and Thickness Control: Achieving uniform coatings with precise thickness can be challenging, especially for complex geometries or large substrates. Advanced control systems and techniques are often required to ensure consistent results.
In summary, Physical Vapor Deposition (PVD) is a sophisticated and versatile technique for depositing thin films of material onto substrates. It involves the conversion of a solid target material into a vapor phase, transportation of the vapor in a vacuum chamber, and condensation onto the substrate to form a thin film. PVD offers numerous advantages, including high adhesion, material versatility, and resistance to high temperatures and corrosion. However, it also presents challenges such as process complexity and the need for precise control over coating uniformity and thickness. Despite these challenges, PVD remains a critical technology in industries ranging from electronics to manufacturing, where high-performance coatings are essential.
Summary Table:
Aspect | Details |
---|---|
Process | Converts solid material to vapor, transports in vacuum, condenses on substrate. |
Methods | Thermal evaporation, sputtering, arc discharge. |
Advantages | High adhesion, material versatility, temperature & corrosion resistance. |
Applications | Electronics, optics, manufacturing (cutting tools, wear-resistant coatings). |
Challenges | Process complexity, material limitations, uniformity control. |
Discover how PVD can enhance your products—contact our experts today for tailored solutions!