Thermal Chemical Vapor Deposition (CVD) is a specialized technique within the broader category of chemical vapor deposition methods. It involves the use of thermal energy to facilitate the chemical reactions necessary for depositing a solid material onto a substrate. This process is widely used in various industries to create high-purity, high-performance coatings and thin films. The method leverages the interaction between gaseous precursors and a heated substrate, resulting in the decomposition or reaction of the gases to form a solid film. The process is highly controllable, allowing for the precise adjustment of film properties by modifying parameters such as temperature, pressure, and gas flow rates.
Key Points Explained:
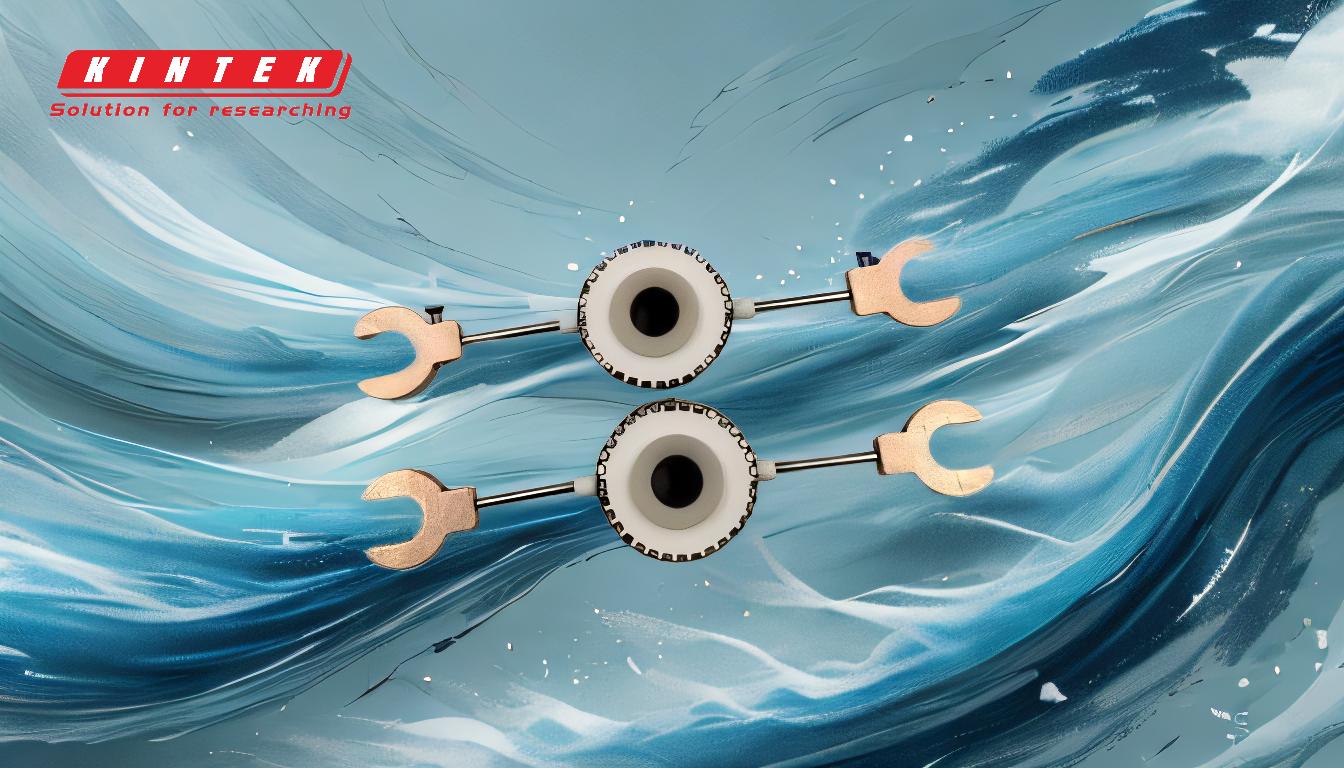
-
Basic Principle of Thermal CVD:
- Thermal CVD relies on the use of heat to initiate and sustain the chemical reactions necessary for film deposition. The substrate is placed in a reaction chamber and heated to a high temperature, typically above 500°C. This thermal energy causes the gaseous precursors to react or decompose on the substrate's surface, forming a solid film.
- The process is driven by the interaction between the heated substrate and the gaseous species, which can include atoms, molecules, or a combination of both.
-
Components of the Thermal CVD Process:
- Reaction Chamber: The chamber is where the substrate and gaseous precursors are housed. It is designed to withstand high temperatures and maintain a controlled environment.
- Gaseous Precursors: These are the volatile compounds that contain the elements needed for the coating. They are introduced into the chamber and react or decompose upon contact with the heated substrate.
- Substrate: The material onto which the coating is deposited. The substrate is typically heated to facilitate the reaction and ensure uniform film growth.
-
Advantages of Thermal CVD:
- High Purity: Thermal CVD can produce highly pure films, which are essential for applications requiring high performance and reliability.
- Control Over Film Properties: By adjusting parameters such as temperature, pressure, and gas flow rates, the properties of the deposited film can be finely tuned.
- Versatility: The method can be used to deposit a wide range of materials, including metals, non-metals, oxides, and nitrides.
-
Applications of Thermal CVD:
- Semiconductor Industry: Thermal CVD is widely used in the fabrication of semiconductor devices, where high-purity films are crucial for performance.
- Optoelectronics: The method is employed in the production of OLED displays, solar cells, and thin-film transistors.
- Protective Coatings: Thermal CVD is used to apply protective coatings on various materials to enhance their durability and resistance to environmental factors.
-
Comparison with Other CVD Methods:
- Aerosol-Assisted CVD: This method uses an aerosol to deliver the precursor, which can be beneficial for certain materials but may not offer the same level of control as thermal CVD.
- Plasma-Based CVD: Plasma-based methods use plasma instead of heat to drive the reactions. While this can lower the required temperature, it may not be suitable for all materials.
- Direct Liquid Injection CVD: This technique involves injecting a liquid precursor into the chamber, which can be useful for materials that are difficult to vaporize.
-
Process Parameters and Their Impact:
- Temperature: The temperature of the substrate and the chamber plays a critical role in determining the rate and quality of the deposition. Higher temperatures generally lead to faster reactions but must be carefully controlled to avoid damaging the substrate.
- Pressure: The pressure within the reaction chamber affects the concentration of the gaseous precursors and the rate at which they interact with the substrate.
- Gas Flow Rate: The flow rate of the precursor gases influences the uniformity and thickness of the deposited film. Proper control of the gas flow is essential for achieving consistent results.
-
Challenges and Considerations:
- Substrate Compatibility: The substrate must be able to withstand the high temperatures required for thermal CVD without degrading.
- Precursor Selection: The choice of precursor gases is critical, as they must be able to decompose or react at the desired temperature to form the desired film.
- Uniformity and Adhesion: Ensuring that the film is uniformly deposited and adheres well to the substrate is essential for the performance and longevity of the coating.
In summary, Thermal Chemical Vapor Deposition is a powerful and versatile method for depositing high-purity, high-performance films onto various substrates. Its ability to precisely control film properties through the adjustment of process parameters makes it a valuable tool in industries ranging from semiconductors to optoelectronics. However, careful consideration of substrate compatibility, precursor selection, and process conditions is essential to achieve optimal results.
Summary Table:
Aspect | Details |
---|---|
Basic Principle | Uses heat to initiate chemical reactions, forming solid films on a heated substrate. |
Key Components | Reaction chamber, gaseous precursors, and substrate. |
Advantages | High purity, precise control over film properties, and versatility in material deposition. |
Applications | Semiconductor devices, optoelectronics (OLEDs, solar cells), and protective coatings. |
Comparison with Others | More control than aerosol-assisted CVD, higher temperature than plasma-based CVD. |
Key Parameters | Temperature, pressure, and gas flow rate influence film quality and uniformity. |
Challenges | Substrate compatibility, precursor selection, and ensuring uniform film adhesion. |
Interested in thermal CVD for your applications? Contact our experts today to learn more!