Thin film deposition is a critical process in materials science and engineering, used to create thin layers of material on a substrate. The two primary categories of thin film deposition methods are Physical Vapor Deposition (PVD) and Chemical Vapor Deposition (CVD). PVD involves the physical vaporization of a solid material in a vacuum, which then condenses onto a substrate to form a thin film. CVD, on the other hand, relies on chemical reactions to deposit a thin film from gaseous precursors. Beyond these, there are other advanced techniques such as Atomic Layer Deposition (ALD) and Spray Pyrolysis, each with unique mechanisms and applications. These methods are chosen based on the desired film properties, substrate material, and specific application requirements.
Key Points Explained:
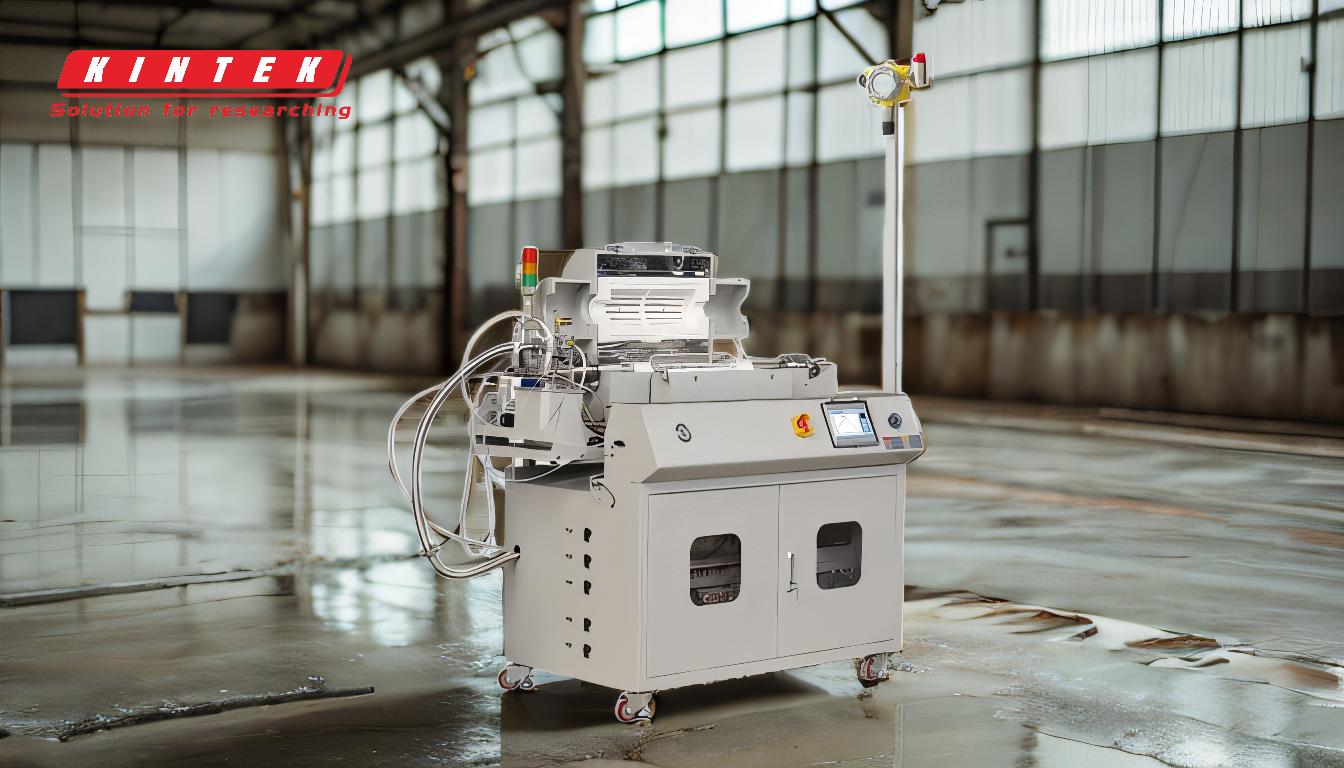
-
Physical Vapor Deposition (PVD)
- Definition: PVD is a process where a solid material is vaporized in a vacuum and then deposited onto a substrate to form a thin film.
- Mechanism: The material is typically vaporized using techniques like thermal evaporation, electron beam evaporation, or sputtering. In sputtering, high-energy ions bombard the target material, ejecting atoms that then deposit onto the substrate.
- Applications: PVD is widely used in industries such as semiconductors, optics, and decorative coatings due to its ability to produce high-purity, dense films.
-
Advantages:
- High control over film thickness and composition.
- Suitable for a wide range of materials, including metals, alloys, and ceramics.
-
Limitations:
- Requires a high-vacuum environment, which can be costly.
- Limited scalability for large-area coatings.
-
Chemical Vapor Deposition (CVD)
- Definition: CVD involves introducing reactant gases into a chamber, where they undergo chemical reactions to form a solid film on the substrate.
- Mechanism: The process typically involves heating the substrate to a high temperature to facilitate the chemical reactions. Variants like Plasma-Enhanced CVD (PECVD) use plasma to lower the reaction temperature.
- Applications: CVD is essential in the production of semiconductors, solar cells, and protective coatings.
-
Advantages:
- Produces high-purity, uniform films with excellent conformality.
- Can deposit a wide variety of materials, including silicon, carbon, and metal oxides.
-
Limitations:
- High temperatures can limit substrate compatibility.
- Requires careful control of gas flow and reaction conditions.
-
Atomic Layer Deposition (ALD)
- Definition: ALD is a specialized form of CVD where films are deposited one atomic layer at a time through self-limiting surface reactions.
- Mechanism: The process alternates between two or more precursor gases, allowing precise control over film thickness at the atomic level.
- Applications: ALD is used in advanced semiconductor manufacturing, nanotechnology, and energy storage devices.
-
Advantages:
- Exceptional control over film thickness and uniformity.
- Enables the deposition of ultra-thin, conformal films on complex geometries.
-
Limitations:
- Slower deposition rates compared to other methods.
- Limited material options due to the need for specific precursors.
-
Spray Pyrolysis
- Definition: Spray pyrolysis involves spraying a solution containing the desired material onto a heated substrate, where it decomposes to form a thin film.
- Mechanism: The solution is atomized into fine droplets and directed onto the substrate, where thermal decomposition occurs.
- Applications: Commonly used for depositing transparent conductive oxides, such as indium tin oxide (ITO), in solar cells and displays.
-
Advantages:
- Simple and cost-effective for large-area coatings.
- Suitable for depositing a variety of materials, including oxides and sulfides.
-
Limitations:
- Limited control over film thickness and uniformity.
- Requires precise control of solution composition and substrate temperature.
-
Other Deposition Methods
- Electroplating: A chemical method where a metal film is deposited onto a conductive substrate using an electric current.
- Sol-Gel: Involves the formation of a gel from a solution, which is then dried and heated to form a thin film.
- Dip Coating and Spin Coating: Simple techniques where a substrate is dipped into or spun with a solution to form a thin film.
- Pulsed Laser Deposition (PLD): A PVD method where a high-power laser ablates material from a target, which then deposits onto a substrate.
-
Choosing the Right Method
- Material Compatibility: The choice of method depends on the material to be deposited and its compatibility with the substrate.
- Film Properties: Desired film properties, such as thickness, uniformity, and purity, influence the selection of the deposition technique.
- Application Requirements: Specific applications, such as semiconductor manufacturing or decorative coatings, may require particular deposition methods.
In summary, thin film deposition methods are diverse and tailored to specific needs. PVD and CVD are the most widely used, but advanced techniques like ALD and Spray Pyrolysis offer unique advantages for specialized applications. Understanding the strengths and limitations of each method is crucial for selecting the appropriate technique for a given application.
Summary Table:
Method | Key Mechanism | Applications | Advantages | Limitations |
---|---|---|---|---|
PVD | Physical vaporization of solid material in a vacuum, condensing onto a substrate. | Semiconductors, optics, decorative coatings | High control over thickness, suitable for metals, alloys, and ceramics. | Requires high-vacuum, limited scalability for large-area coatings. |
CVD | Chemical reactions of gases to form a solid film on a substrate. | Semiconductors, solar cells, coatings | High-purity, uniform films; wide material variety. | High temperatures, precise gas flow control required. |
ALD | Atomic layer-by-layer deposition via self-limiting surface reactions. | Advanced semiconductors, nanotechnology | Exceptional thickness control, conformal films on complex geometries. | Slower deposition rates, limited material options. |
Spray Pyrolysis | Spraying solution onto a heated substrate for thermal decomposition. | Solar cells, displays (e.g., ITO films) | Cost-effective for large areas, suitable for oxides and sulfides. | Limited thickness control, precise solution and temperature control required. |
Need help selecting the right thin film deposition method for your project? Contact our experts today!