Thin film processing in semiconductors involves the deposition of very thin layers of material onto a substrate, typically silicon or silicon carbide, to create functional layers for electronic devices. The two primary techniques used are Chemical Vapor Deposition (CVD) and Physical Vapor Deposition (PVD). CVD is favored for its precision and ability to produce high-quality films, while PVD is known for creating high-purity coatings. These processes are essential for manufacturing integrated circuits, transistors, solar cells, LEDs, and other semiconductor devices. Thin films enable the miniaturization of components and are patterned using lithographic technologies to form active and passive devices.
Key Points Explained:
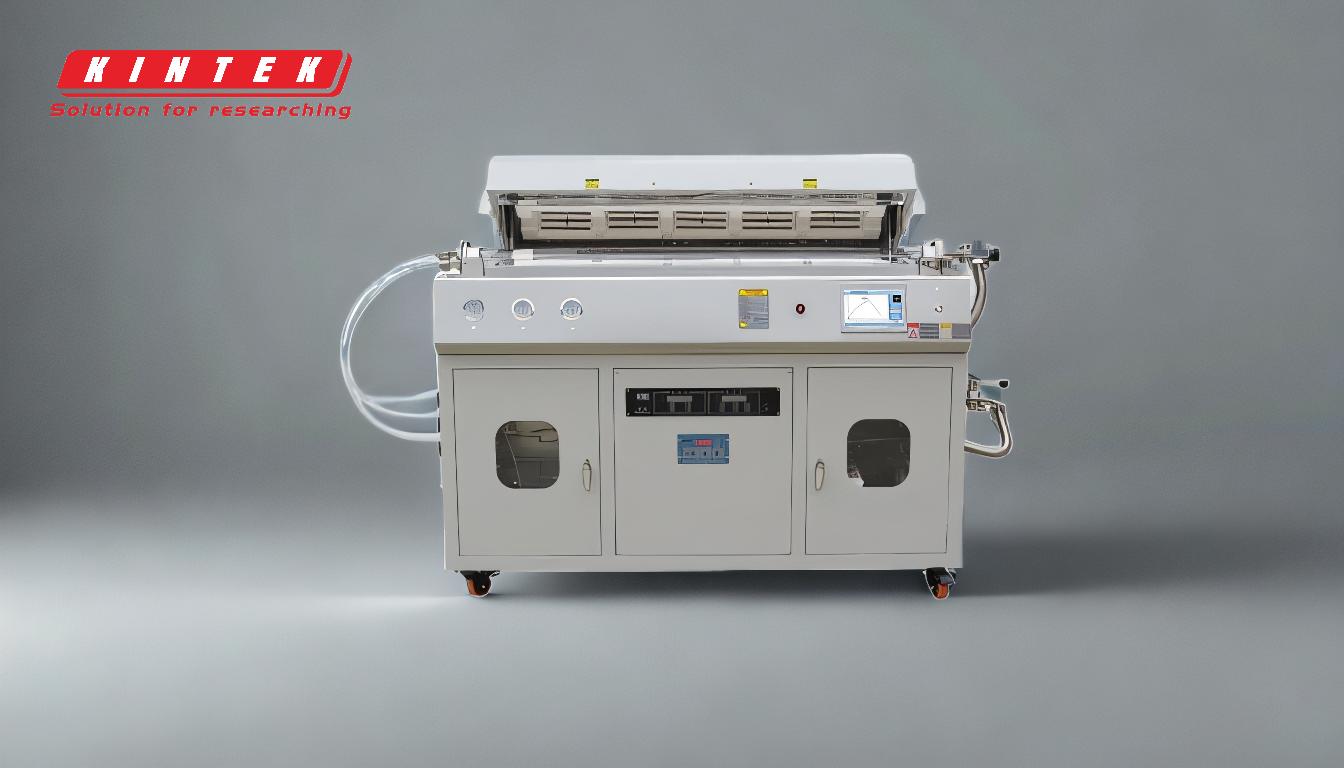
-
Thin Film Deposition Techniques:
-
Chemical Vapor Deposition (CVD): This technique involves chemical reactions to deposit a thin film on the substrate. It is widely used in the semiconductor industry due to its high precision and ability to produce uniform and high-quality films. CVD methods include:
- Chemical Bath Deposition: A simple, low-cost method where a substrate is immersed in a chemical solution to form a thin film.
- Electroplating: A process that uses electrical current to reduce dissolved metal cations so that they form a coherent metal coating on an electrode.
- Molecular Beam Epitaxy (MBE): A highly controlled method for growing thin films with precise atomic layers.
- Thermal Oxidation: A process that forms a thin oxide layer on a silicon substrate by heating it in an oxygen-rich environment.
-
Physical Vapor Deposition (PVD): This technique involves the physical transfer of material from a source to the substrate. PVD methods include:
- Evaporation: The source material is heated to a high temperature, causing it to evaporate and condense on the substrate.
- Sputtering: A process where atoms are ejected from a solid target material due to bombardment of the target by energetic particles.
- E-beam Evaporation: A form of evaporation where an electron beam is used to heat the source material.
-
Chemical Vapor Deposition (CVD): This technique involves chemical reactions to deposit a thin film on the substrate. It is widely used in the semiconductor industry due to its high precision and ability to produce uniform and high-quality films. CVD methods include:
-
Applications of Thin Films in Semiconductors:
- Integrated Circuits (ICs): Thin films are used to create the various layers of an IC, including the insulating, conducting, and semiconducting layers.
- Transistors: Thin films form the gate dielectric, source, drain, and channel regions in transistors.
- Solar Cells: Thin films are used to create the active layers that absorb light and convert it into electricity.
- LEDs: Thin films are used to create the multiple layers that make up an LED, including the n-type and p-type layers.
- Miniaturization: Thin films enable the creation of smaller and more efficient semiconductor components, such as BJTs, FETs, MOSFETs, and diodes.
-
Fabrication Process:
- Forming Layers: The process begins with forming an ammonia layer on the interlayer insulator, followed by covering it with a light-resistant layer.
- Photoresist Patterning: A photoresist pattern is developed using lithographic techniques.
- Etching: The ammonia layer and interlayer insulation are etched using the photoresist pattern as a mask.
- Doping: Doping is performed relative to the connection regions and the semiconductor volume to modify the electrical properties of the material.
- Removing Photoresist: The photoresist pattern is removed by etching, leaving behind the patterned thin film.
-
Advanced Deposition Methods:
- Atomic Layer Deposition (ALD): This technique deposits films one atomic layer at a time, allowing for extremely precise control over film thickness and composition.
- Spray Pyrolysis: A method where a material solution is sprayed onto the substrate and thermally degraded to form a thin layer.
-
Importance of Thin Films:
- High Precision: Thin films allow for the creation of highly precise and uniform layers, which are essential for the performance of semiconductor devices.
- Versatility: Thin films can be applied to various surfaces and used in a wide range of applications, from microelectronics to optoelectronics.
- Miniaturization: The ability to create thin, uniform layers enables the miniaturization of electronic components, leading to more compact and efficient devices.
In summary, thin film processing is a critical aspect of semiconductor manufacturing, involving precise deposition techniques to create functional layers for a variety of electronic devices. The choice of deposition method depends on the specific requirements of the application, with CVD and PVD being the most commonly used techniques. These processes enable the production of high-quality, miniaturized components that are essential for modern electronics.
Summary Table:
Aspect | Details |
---|---|
Primary Techniques | - Chemical Vapor Deposition (CVD): High precision, uniform films. |
- Physical Vapor Deposition (PVD): High-purity coatings. | |
Applications | - Integrated Circuits (ICs), Transistors, Solar Cells, LEDs. |
Fabrication Process | - Layer formation, photoresist patterning, etching, doping, and removal. |
Advanced Methods | - Atomic Layer Deposition (ALD), Spray Pyrolysis. |
Importance | - High precision, versatility, and miniaturization of components. |
Discover how thin film processing can revolutionize your semiconductor projects—contact our experts today!