Pyrolysis is a thermal decomposition process that occurs in the absence of oxygen, and its outcomes are highly dependent on temperature, heating rate, and residence time. For effective flash pyrolysis, temperatures typically range from 450–600 °C, with heating rates between 10^3 to 10^4 °C/s and residence times of less than 1 second. At lower temperatures (below 450°C) with slow heating rates, pyrolysis primarily yields biochar. At intermediate temperatures with high heating rates, bio-oil is the main product, while high temperatures (above 800°C) with rapid heating rates favor gas production. The process is also influenced by factors such as material composition, particle size, and thermal environment, which determine the distribution of solid, liquid, and gaseous products.
Key Points Explained:
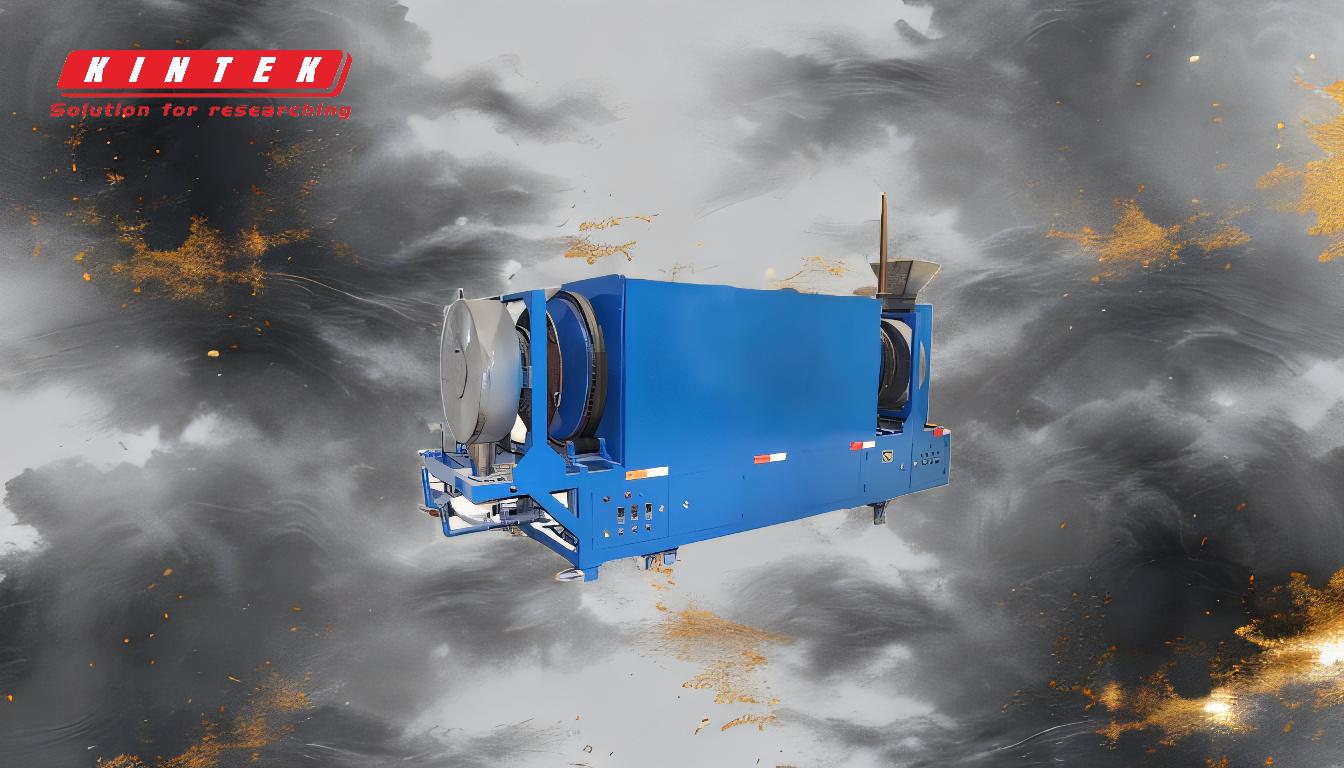
-
Temperature Ranges and Product Yields:
- Low Temperatures (Below 450°C): Pyrolysis at low temperatures with slow heating rates primarily produces biochar, a solid carbon-rich material. This is ideal for applications requiring high-quality solid products.
- Intermediate Temperatures (450–600°C): At these temperatures with relatively high heating rates, the main product is bio-oil, a liquid fuel. This range is often targeted for flash pyrolysis due to its efficiency in producing bio-oil.
- High Temperatures (Above 800°C): High temperatures with rapid heating rates favor the production of non-condensable gases, such as syngas, which can be used for energy generation.
-
Heating Rates:
- Slow Heating Rates: These are associated with low-temperature pyrolysis and result in higher char yields. The slower the heating rate, the more time the material has to undergo thermal decomposition into solid products.
- High Heating Rates: Rapid heating rates (10^3 to 10^4 °C/s) are used in flash pyrolysis to maximize bio-oil production. These rates minimize char formation and promote the breakdown of biomass into liquid and gaseous products.
-
Residence Time:
- Short Residence Times (Less Than 1 Second): In flash pyrolysis, short residence times are critical to achieving high bio-oil yields. Longer residence times can lead to secondary reactions, reducing oil yield and increasing gas production.
- Longer Residence Times: These are typically used in slow pyrolysis processes to maximize char production. The extended time allows for more complete thermal decomposition of the material.
-
Factors Influencing Pyrolysis Outcomes:
- Material Composition: Different biomass components decompose at different temperatures, affecting the distribution of pyrolysis products. For example, cellulose and hemicellulose decompose at lower temperatures, while lignin requires higher temperatures.
- Particle Size: Smaller particle sizes lead to quicker and more uniform thermal decomposition, increasing the yield of pyrolysis oil.
- Atmosphere and Pressure: The absence of oxygen is essential for pyrolysis, and pressure conditions can influence the reaction kinetics and product distribution.
- Feed Rate: The rate at which material is fed into the pyrolysis chamber affects the heating rate and residence time, both of which are critical for determining the final product mix.
-
Applications of Pyrolysis Products:
- Biochar: Used as a soil amendment, carbon sequestration agent, or in filtration systems.
- Bio-oil: Can be refined into transportation fuels or used as a feedstock for chemical production.
- Gases: Non-condensable gases like syngas are used for energy generation or as a precursor for synthetic fuels.
By understanding these key factors—temperature, heating rate, residence time, and material properties—purchasers and operators of pyrolysis equipment can optimize the process to achieve the desired product yields for specific applications.
Summary Table:
Factor | Impact on Pyrolysis |
---|---|
Temperature | - Low (<450°C): Biochar - Intermediate (450–600°C): Bio-oil - High (>800°C): Syngas |
Heating Rate | - Slow: Higher char yield - Fast (10^3–10^4 °C/s): Maximizes bio-oil production |
Residence Time | - Short (<1s): High bio-oil yield - Long: Maximizes char production |
Material Composition | Affects decomposition temperature and product distribution |
Particle Size | Smaller particles increase pyrolysis oil yield |
Ready to optimize your pyrolysis process? Contact our experts today for tailored solutions!