The uniaxial pressing method is a widely used technique in materials science and manufacturing for forming powdered materials into solid shapes. This process involves applying pressure in a single direction to compact the powder within a die, resulting in a dense and uniform green body. The method is particularly favored for its simplicity, cost-effectiveness, and ability to produce parts with high dimensional accuracy. It is commonly used in the production of ceramics, metals, and composites. The process typically includes steps such as powder preparation, die filling, pressing, and ejection of the compacted part. Uniaxial pressing is suitable for both small-scale laboratory research and large-scale industrial production.
Key Points Explained:
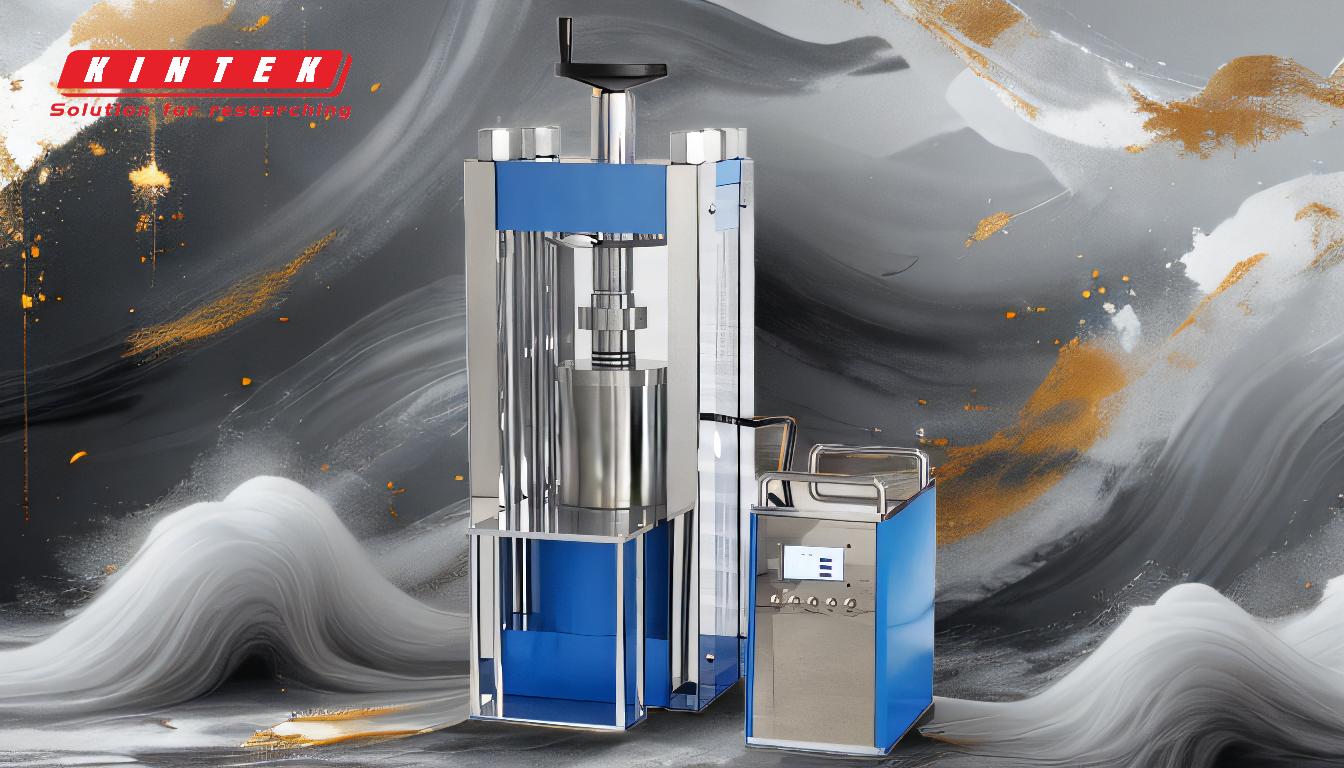
-
Definition and Overview of Uniaxial Pressing:
- Uniaxial pressing is a compaction technique where pressure is applied in one direction to consolidate powdered materials into a solid shape.
- It is commonly used in the manufacturing of ceramics, metals, and composite materials due to its simplicity and efficiency.
-
Steps Involved in the Uniaxial Pressing Process:
- Powder Preparation: The raw material is prepared by milling or mixing to achieve the desired particle size and distribution.
- Die Filling: The powder is poured into a die cavity, ensuring even distribution to avoid defects in the final product.
- Pressing: Pressure is applied uniaxially (in one direction) using a hydraulic or mechanical press to compact the powder into a dense green body.
- Ejection: The compacted part is ejected from the die, ready for further processing such as sintering.
-
Advantages of Uniaxial Pressing:
- Cost-Effectiveness: The process requires relatively simple equipment and has low operational costs.
- High Dimensional Accuracy: Parts produced by uniaxial pressing have precise dimensions and consistent density.
- Scalability: It is suitable for both small-scale laboratory research and large-scale industrial production.
-
Applications of Uniaxial Pressing:
- Ceramics: Used to produce components like insulators, refractories, and structural ceramics.
- Metals: Applied in the production of metal powders for sintering and additive manufacturing.
- Composites: Enables the fabrication of composite materials with tailored properties.
-
Limitations and Considerations:
- Anisotropy: The unidirectional pressure can lead to anisotropic properties in the final product, which may not be desirable for some applications.
- Die Wear: Frequent use of dies can lead to wear and tear, requiring maintenance or replacement.
- Powder Characteristics: The success of the process depends on the flowability and compressibility of the powder.
-
Comparison with Other Pressing Methods:
- Isostatic Pressing: Unlike uniaxial pressing, isostatic pressing applies pressure uniformly from all directions, resulting in isotropic properties but requiring more complex equipment.
- Hot Pressing: Combines heat and pressure to achieve higher densities, but is more energy-intensive and costly.
By understanding the uniaxial pressing method, manufacturers and researchers can leverage its advantages while addressing its limitations to produce high-quality materials and components efficiently.
Summary Table:
Aspect | Details |
---|---|
Definition | Compaction technique applying pressure in one direction to form solid shapes. |
Steps | Powder preparation, die filling, pressing, and ejection. |
Advantages | Cost-effective, high dimensional accuracy, scalable. |
Applications | Ceramics, metals, and composites. |
Limitations | Anisotropy, die wear, and dependency on powder characteristics. |
Comparison | Isostatic pressing (uniform pressure), hot pressing (heat + pressure). |
Discover how uniaxial pressing can optimize your material production—contact us today for expert guidance!