CVD (Chemical Vapor Deposition) coatings are versatile and high-performance thin films used across a wide range of industries and applications. They are valued for their ability to provide wear resistance, corrosion resistance, high-temperature protection, and erosion protection, among other properties. These coatings can be applied to various base materials, including ceramics, glass, metals, and metal alloys, and are capable of coating intricate and precision surfaces. CVD coatings are particularly useful in demanding environments, such as biomedical implants, circuit boards, machine tools, and analytical flow path components, due to their durability, adhesion, and ability to withstand extreme conditions. The precursor gases used in CVD can be tailored to optimize specific properties like lubricity, chemical inertness, or high purity, making them suitable for specialized applications.
Key Points Explained:
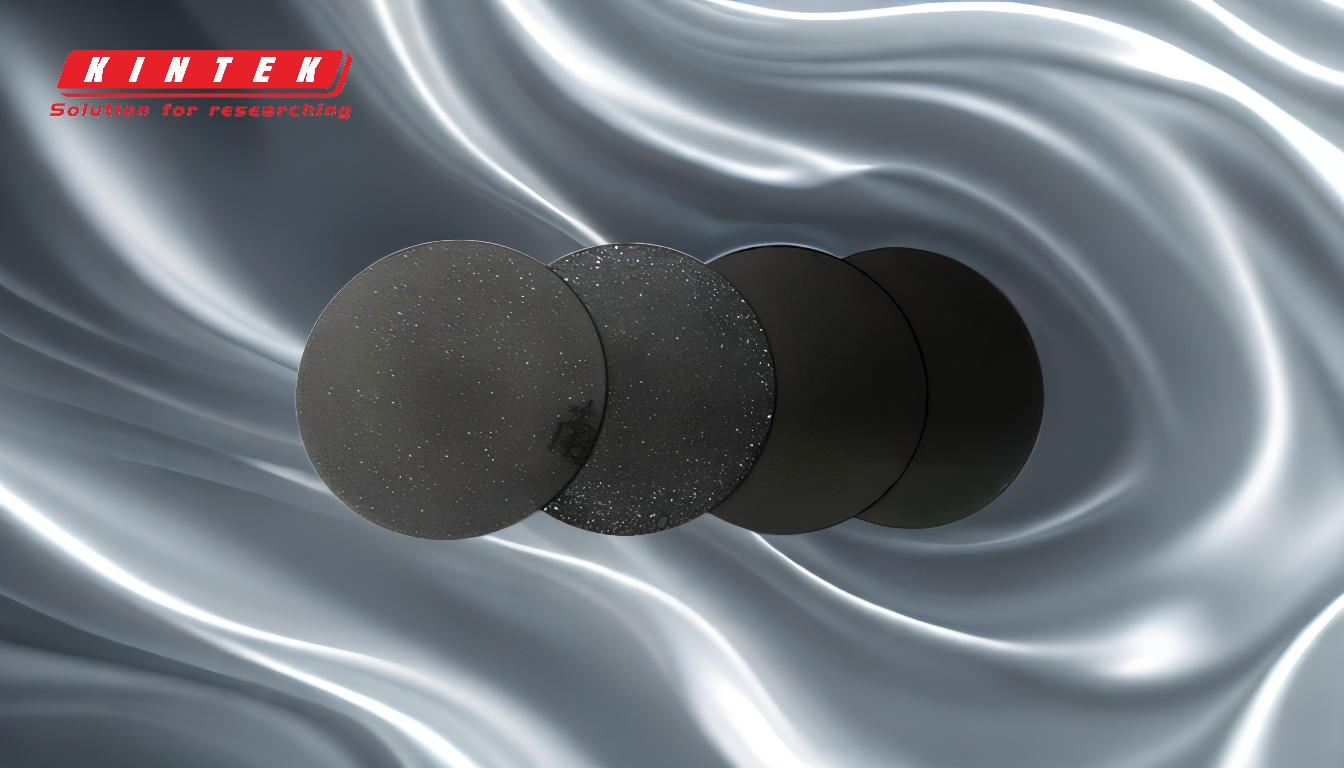
-
Versatility in Applications
- CVD coatings are used in a wide range of industries, including biomedical, electronics, manufacturing, and instrumentation.
- Common applications include:
- Biomedical device implants (e.g., corrosion-resistant coatings for surgical tools or implants).
- Circuit boards (e.g., dielectric films like silicon dioxide or silicon nitride for insulation).
- Machine tools and wear components (e.g., wear-resistant coatings to extend tool life).
- Analytical flow path components (e.g., coatings for chemical inertness in lab equipment).
-
High Performance and Durability
- CVD coatings are known for their ability to withstand extreme conditions, including:
- High and low temperatures, as well as rapid temperature variations.
- High-stress environments, where the coating remains bonded even when the substrate flexes or bends.
- These properties make them ideal for applications requiring long-term durability and reliability.
- CVD coatings are known for their ability to withstand extreme conditions, including:
-
Wide Range of Base Materials
- CVD coatings can be applied to various substrates, including:
- Ceramics (e.g., for high-temperature applications).
- Glass (e.g., for optical or protective coatings).
- Metals and metal alloys (e.g., for wear or corrosion resistance).
- This versatility allows CVD coatings to be used in diverse industries and applications.
- CVD coatings can be applied to various substrates, including:
-
Precision and Intricate Surface Coating
- CVD coatings can coat complex geometries, including:
- Internal surfaces and seal areas.
- Intricate or precision-engineered components.
- This capability is critical for applications where uniform coating thickness and coverage are essential.
- CVD coatings can coat complex geometries, including:
-
Tailored Properties Through Precursor Gas Optimization
- The precursor gases used in CVD can be optimized to achieve specific properties, such as:
- Wear resistance (e.g., for machine tools).
- Lubricity (e.g., for reducing friction in moving parts).
- Corrosion resistance (e.g., for biomedical implants or marine equipment).
- Chemical inertness (e.g., for analytical instruments).
- High purity (e.g., for semiconductor manufacturing).
- This customization makes CVD coatings highly adaptable to specialized needs.
- The precursor gases used in CVD can be optimized to achieve specific properties, such as:
-
Smooth Surface Finish and Thin Film Deposition
- CVD coatings are used to deposit thin films with a smooth surface finish, which is critical for applications such as:
- Semiconductors (e.g., silicon or carbon films).
- Dielectric films (e.g., silicon dioxide or silicon nitride for insulation).
- The smooth finish ensures optimal performance in electronic and optical applications.
- CVD coatings are used to deposit thin films with a smooth surface finish, which is critical for applications such as:
-
Resistance to Environmental Challenges
- CVD coatings provide protection against:
- Corrosion (e.g., in harsh chemical environments).
- Erosion (e.g., in high-velocity fluid flow applications).
- Fouling (e.g., in marine or biomedical applications).
- This makes them suitable for use in challenging environments where other coatings might fail.
- CVD coatings provide protection against:
-
Strong Coating-to-Substrate Bond
- The adhesion of CVD coatings to substrates is exceptionally strong, ensuring:
- Long-term durability in high-stress environments.
- Resistance to delamination or peeling, even under mechanical stress or temperature fluctuations.
- This bond is critical for applications where the coating must remain intact under extreme conditions.
- The adhesion of CVD coatings to substrates is exceptionally strong, ensuring:
In summary, CVD coatings are a critical technology for creating high-performance, durable, and tailored thin films across a wide range of industries. Their ability to coat various materials, withstand extreme conditions, and provide specific functional properties makes them indispensable in applications ranging from biomedical implants to semiconductor manufacturing. The flexibility of the CVD process, combined with its ability to produce smooth, adherent coatings, ensures its continued relevance in advanced material science and engineering.
Summary Table:
Key Benefits of CVD Coatings | Applications |
---|---|
Wear resistance | Machine tools, wear components |
Corrosion resistance | Biomedical implants, marine equipment |
High-temperature protection | Ceramics, glass, metals |
Erosion resistance | Analytical flow path components |
Tailored properties (e.g., lubricity, chemical inertness) | Semiconductor manufacturing, lab equipment |
Smooth surface finish | Optical, electronic applications |
Strong coating-to-substrate bond | High-stress environments |
Unlock the potential of CVD coatings for your industry—contact our experts today!