Physical Vapor Deposition (PVD) is a versatile and widely used technique for depositing thin films and coatings with precise control over thickness, composition, and properties. It is employed across various industries to enhance the performance, durability, and functionality of materials and components. PVD is particularly valued for its ability to produce dense, high-quality coatings that are resistant to wear, corrosion, and extreme temperatures. Applications range from aerospace and semiconductors to cutting tools, decorative coatings, and biomedical devices. The technique is also used to create optical films, reflective coatings, and multilayer structures, making it indispensable in advanced manufacturing and technology sectors.
Key Points Explained:
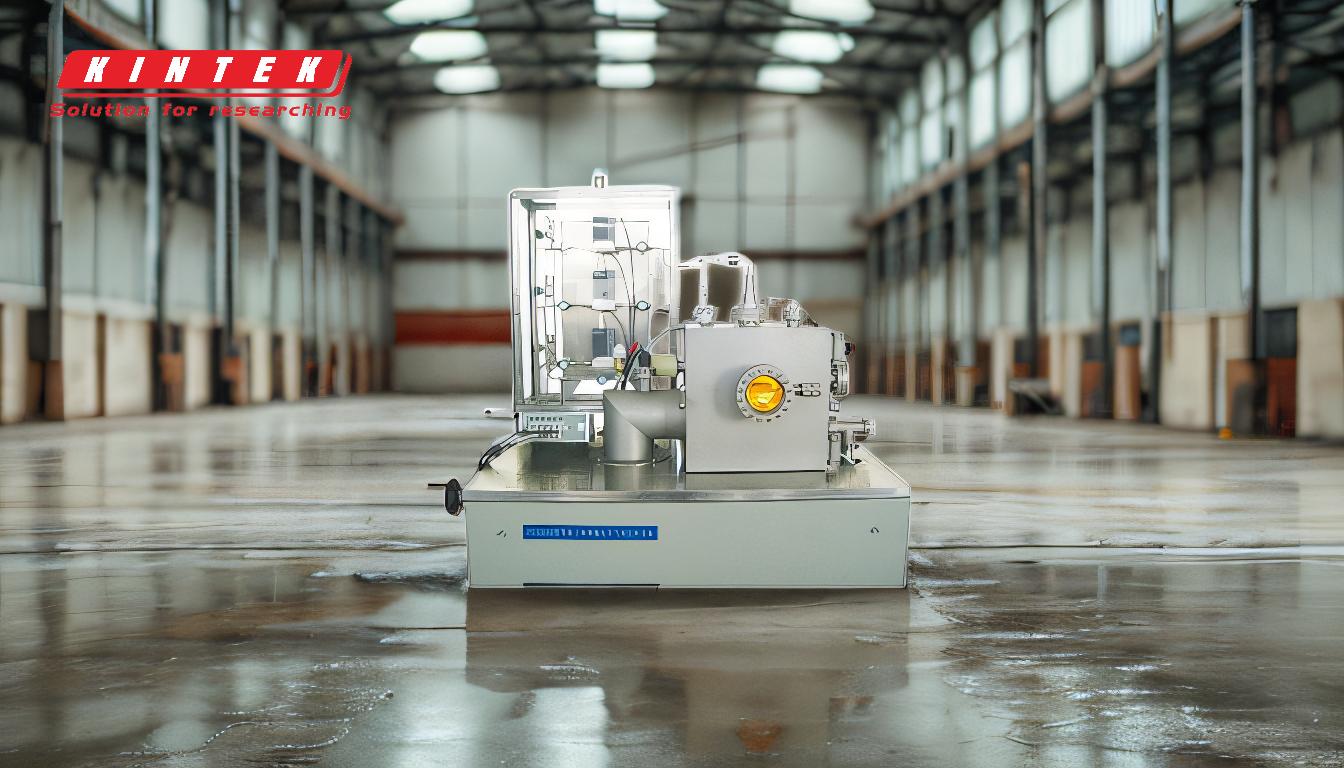
-
Thin Film Deposition for Functional Applications:
- PVD is used to deposit thin films ranging from a few nanometers to thousands of nanometers in thickness.
- These films serve mechanical, optical, chemical, or electronic functions in various products.
- Examples include semiconductor devices, thin-film solar panels, and aluminized PET films for food packaging and balloons.
-
Enhanced Durability and Performance:
- PVD coatings are applied to improve the durability and performance of materials and components.
- In the aerospace industry, PVD is used to apply dense, temperature-resistant coatings to components, enabling them to withstand extreme conditions.
- Cutting tools are coated with materials like titanium nitride to enhance hardness and wear resistance, extending their lifespan in demanding applications.
-
Corrosion and Wear Resistance:
- PVD is widely used to apply hard, corrosion-resistant coatings to protect tools and products used in harsh environments.
- These coatings are critical in industries such as manufacturing, where tools are exposed to abrasive or corrosive conditions.
-
Optical and Reflective Coatings:
- PVD is employed to create optical films for applications like solar panels and reflective coatings.
- These coatings are essential for improving the efficiency of solar energy systems and producing highly reflective surfaces for mirrors and other optical devices.
-
Multilayer and Graded Composition Coatings:
- PVD techniques can produce multilayer coatings and graded composition deposits, allowing for tailored material properties.
- This capability is valuable in advanced manufacturing, where specific material characteristics are required for specialized applications.
-
Diverse Industry Applications:
- PVD is used in a wide range of industries, including aerospace, semiconductors, cutting tools, decorative coatings, and biomedical fields.
- In the biomedical sector, PVD coatings are applied to implants and medical devices to improve biocompatibility and resistance to wear.
-
Freestanding Structures and Thick Deposits:
- Beyond thin films, PVD can also be used to create freestanding structures and very thick deposits.
- This versatility expands its applicability to more complex and demanding manufacturing needs.
-
E-beam Evaporation for Precision Coatings:
- E-beam evaporation, a PVD technique, is particularly valued for its ability to deposit dense, high-quality coatings with precise control.
- It is commonly used in aerospace and semiconductor industries for temperature-resistant and optical coatings.
By leveraging the capabilities of PVD, industries can achieve significant improvements in material performance, product longevity, and functionality, making it a critical technology in modern manufacturing and engineering.
Summary Table:
Key Aspect | Details |
---|---|
Thin Film Deposition | Deposits films from nanometers to micrometers for mechanical, optical, and electronic functions. |
Durability & Performance | Enhances material lifespan and performance in extreme conditions. |
Corrosion & Wear Resistance | Protects tools and components in harsh environments. |
Optical & Reflective Coatings | Improves solar panel efficiency and creates reflective surfaces. |
Multilayer Coatings | Tailors material properties for specialized applications. |
Industry Applications | Aerospace, semiconductors, cutting tools, decorative coatings, and biomedical devices. |
E-beam Evaporation | Deposits dense, high-quality coatings with precise control. |
Unlock the potential of PVD coatings for your industry—contact our experts today to learn more!