Vacuum evaporation is a technique used to concentrate substances dissolved in water or to deposit thin films of materials onto substrates. It involves converting a material into vapor by applying heat in a high-vacuum environment, which minimizes interactions with other gas molecules. This process is widely used in industries such as semiconductor manufacturing, optics, and food processing. The vacuum environment ensures efficient transport of vaporized material to the target surface, making it a precise and controlled method for material deposition or concentration.
Key Points Explained:
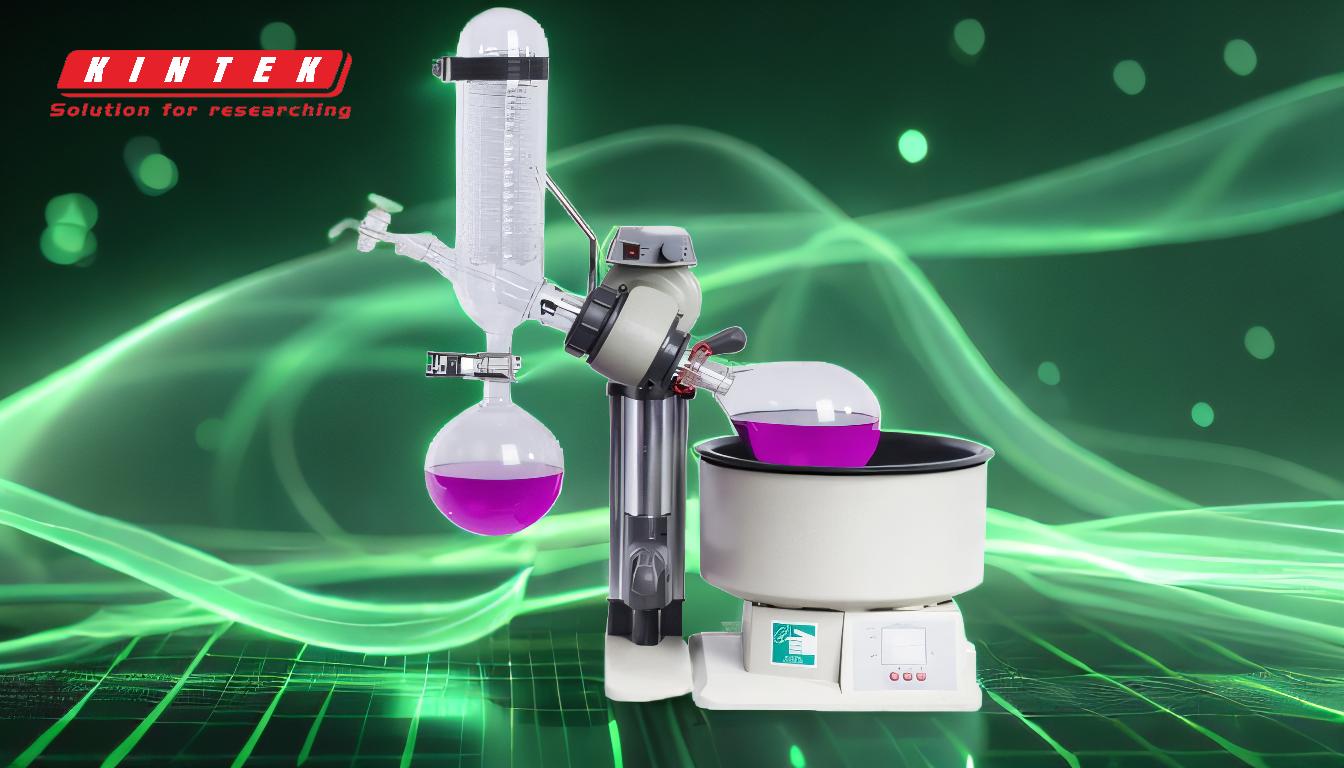
-
Definition of Vacuum Evaporation:
- Vacuum evaporation is a process where a material is heated to its vaporization point in a vacuum environment. The absence of air or other gases reduces collisions, allowing the vaporized material to travel unimpeded to a substrate or condense for concentration purposes.
-
Applications of Vacuum Evaporation:
- Concentration of Solutions: Used in industries like food processing to concentrate liquids such as fruit juices or milk by evaporating water under reduced pressure.
- Thin Film Deposition: In industries like semiconductor manufacturing, vacuum evaporation is used to deposit thin films of materials onto substrates, creating layers for electronic devices or optical coatings.
-
Process Mechanism:
- Heating the Source Material: The material to be evaporated is heated, often using resistive heating, electron beams, or induction heating, until it reaches its vaporization temperature.
- High-Vacuum Environment: The process takes place in a vacuum chamber to eliminate gas molecules that could interfere with the vapor's path to the substrate.
- Transport and Deposition: The vaporized material travels through the vacuum and condenses on the substrate, forming a thin film or concentrated residue.
-
Advantages of Vacuum Evaporation:
- Precision and Control: The vacuum environment allows for precise control over the deposition or concentration process, ensuring uniformity and quality.
- Minimized Contamination: The absence of air reduces the risk of contamination from impurities.
- Versatility: Suitable for a wide range of materials, including metals, semiconductors, and organic compounds.
-
Challenges and Limitations:
- High Equipment Costs: Vacuum chambers and heating systems can be expensive to install and maintain.
- Energy Consumption: The process requires significant energy to maintain the vacuum and heat the material.
- Material Limitations: Some materials may decompose or react under high temperatures, limiting their suitability for vacuum evaporation.
-
Comparison with Other Techniques:
- Vacuum Evaporation vs. Sputtering: Unlike sputtering, which uses energetic ions to dislodge atoms from a target, vacuum evaporation relies solely on thermal energy to vaporize the material.
- Vacuum Evaporation vs. Chemical Vapor Deposition (CVD): CVD involves chemical reactions to deposit materials, whereas vacuum evaporation is a purely physical process.
-
Future Trends:
- Nanotechnology Applications: Vacuum evaporation is increasingly used in nanotechnology to create nanostructured materials with unique properties.
- Sustainability Improvements: Efforts are being made to reduce energy consumption and improve the efficiency of vacuum evaporation systems.
By understanding these key points, equipment and consumable purchasers can make informed decisions about the suitability of vacuum evaporation for their specific applications, considering factors like cost, material compatibility, and desired outcomes.
Summary Table:
Aspect | Details |
---|---|
Definition | Heating materials in a vacuum to vaporize and deposit or concentrate them. |
Applications | Thin film deposition, solution concentration in semiconductors, food, etc. |
Advantages | Precision, minimized contamination, versatility for various materials. |
Challenges | High equipment costs, energy consumption, material limitations. |
Comparison | Differs from sputtering and CVD by relying on thermal energy alone. |
Future Trends | Nanotechnology, sustainability improvements in energy efficiency. |
Discover how vacuum evaporation can enhance your processes—contact our experts today for tailored solutions!