Vapor phase materials refer to substances that exist in the gaseous state under specific conditions, often used in various industrial and scientific applications such as chemical vapor deposition (CVD), surface modification, and thin-film coating. These materials are typically introduced into a reaction chamber in their gaseous form, where they undergo chemical reactions to form solid deposits or modify surfaces. Understanding vapor phase materials is crucial for applications in semiconductor manufacturing, nanotechnology, and advanced material synthesis.
Key Points Explained:
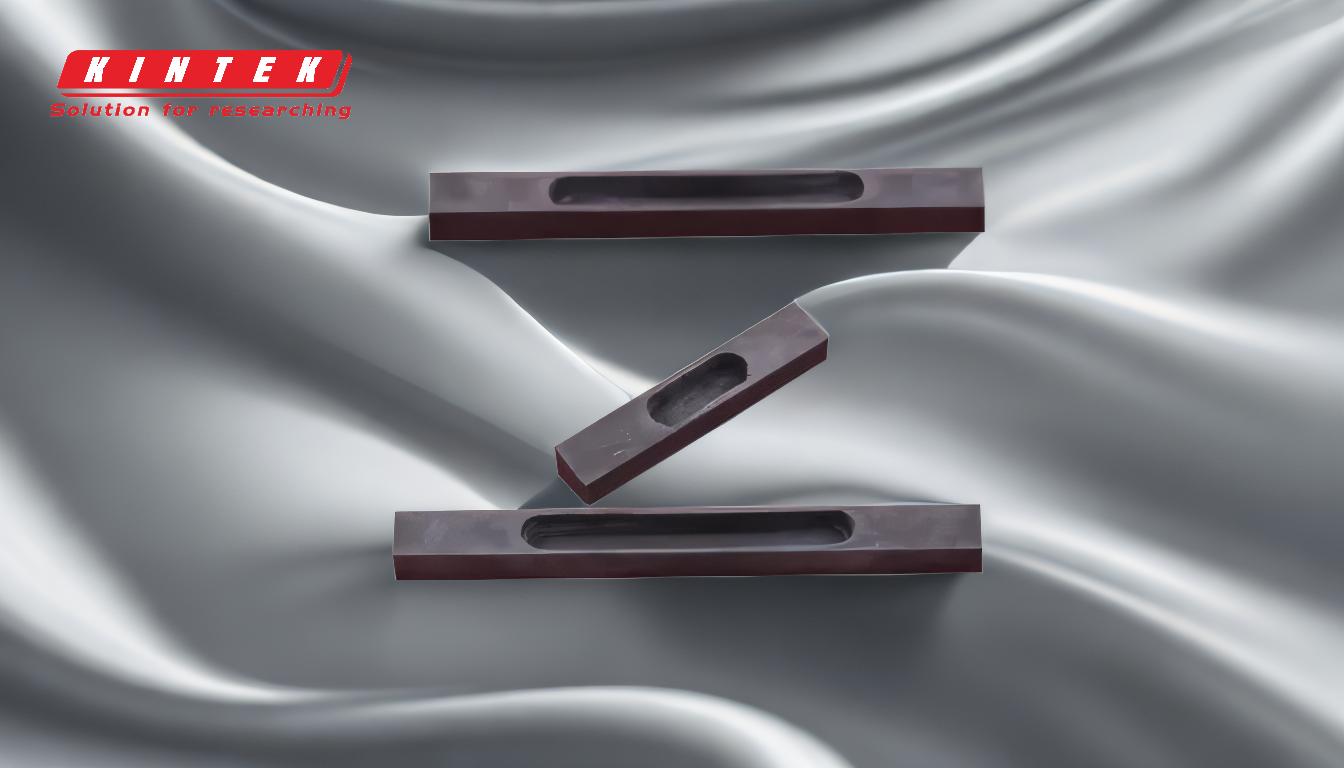
-
Definition of Vapor Phase Materials:
- Vapor phase materials are substances that are in a gaseous state under specific temperature and pressure conditions. They are often used in processes where precise control over material deposition or surface modification is required.
-
Applications of Vapor Phase Materials:
- Chemical Vapor Deposition (CVD): A process where vapor phase materials are used to deposit thin films on substrates. This is widely used in semiconductor manufacturing to create integrated circuits and other electronic components.
- Surface Modification: Vapor phase materials can be used to alter the surface properties of materials, such as increasing hardness, corrosion resistance, or adhesion.
- Thin-Film Coating: Used in the production of optical coatings, solar cells, and protective layers on various materials.
-
Types of Vapor Phase Materials:
- Organic Compounds: Such as methane, ethylene, and other hydrocarbons used in CVD processes.
- Inorganic Compounds: Including metal halides, oxides, and nitrides, which are often used in the deposition of metallic and ceramic films.
- Elemental Gases: Such as hydrogen, nitrogen, and argon, which are used as carrier gases or reactive gases in various processes.
-
Advantages of Using Vapor Phase Materials:
- Precision: Allows for precise control over the thickness and composition of deposited materials.
- Uniformity: Ensures even coating and modification across large areas or complex geometries.
- Versatility: Can be used with a wide range of materials and substrates.
-
Challenges and Considerations:
- Safety: Handling gaseous materials requires strict safety protocols to prevent leaks and exposure.
- Purity: High purity of vapor phase materials is essential to avoid contamination and ensure the quality of the final product.
- Equipment: Specialized equipment such as reactors, gas delivery systems, and exhaust management systems are required for handling vapor phase materials.
-
Future Trends:
- Nanotechnology: Increasing use of vapor phase materials in the synthesis of nanomaterials and nanostructures.
- Sustainability: Development of more environmentally friendly vapor phase materials and processes.
- Advanced Manufacturing: Integration of vapor phase material processes with additive manufacturing and other advanced fabrication techniques.
Understanding vapor phase materials and their applications is essential for advancements in technology and material science, particularly in fields requiring high precision and control over material properties.
Summary Table:
Aspect | Details |
---|---|
Definition | Substances in gaseous state under specific conditions, used for precise processes. |
Applications | CVD, surface modification, thin-film coating. |
Types | Organic compounds, inorganic compounds, elemental gases. |
Advantages | Precision, uniformity, versatility. |
Challenges | Safety, purity, specialized equipment. |
Future Trends | Nanotechnology, sustainability, advanced manufacturing. |
Learn how vapor phase materials can revolutionize your processes—contact our experts today!