Chemical Vapor Deposition (CVD) is a versatile and widely used technique for depositing high-quality thin films and coatings onto substrates. It involves the use of gaseous or vaporized precursors that undergo chemical reactions on the substrate surface, forming a solid layer. The process is highly controllable, allowing for the deposition of a wide range of materials, including metals, semiconductors, and ceramics. CVD is performed in a vacuum or controlled environment, where parameters like temperature, pressure, and gas flow are precisely regulated to achieve the desired film properties. The process is economical, scalable, and capable of producing uniform, dense, and high-performance coatings.
Key Points Explained:
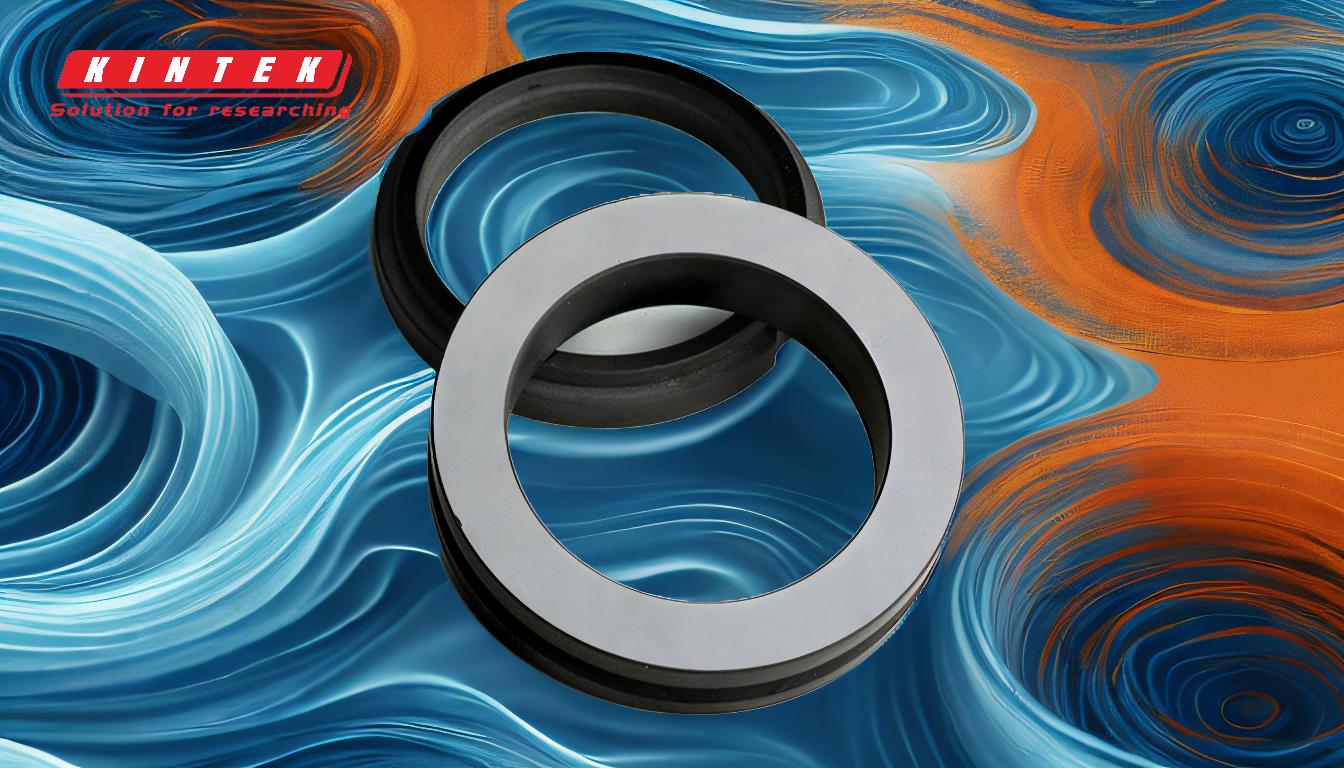
-
Basic Principle of CVD:
- CVD relies on chemical reactions between gaseous or vaporized precursors and a substrate surface.
- The precursors are introduced into a reaction chamber, where they decompose or react under controlled conditions (temperature, pressure, and gas flow).
- The resulting solid material is deposited as a thin film on the substrate.
-
Process Steps:
- Introduction of Precursors: Gaseous or vaporized reactants containing the desired material are introduced into the reaction chamber.
- Chemical Reaction: The precursors undergo decomposition or chemical reactions on the substrate surface, often facilitated by heat, plasma, or other energy sources.
- Deposition: The solid material formed from the reaction adheres to the substrate, creating a uniform and dense layer.
- By-product Removal: Volatile by-products generated during the reaction are removed from the chamber via gas flow or vacuum pumping.
-
Key Components and Conditions:
- Reaction Chamber: A controlled environment where the deposition occurs, often under vacuum or low-pressure conditions.
- Substrate: The surface onto which the material is deposited. It must be compatible with the deposition process and capable of withstanding the reaction conditions.
- Energy Sources: Heat, plasma, or light radiation is used to activate the chemical reactions.
- Precursors: Volatile compounds that provide the necessary elements for the deposition. These can be gases, liquids, or solids with high vapor pressure.
-
Types of CVD:
- Thermal CVD: Uses heat to drive the chemical reactions.
- Plasma-Enhanced CVD (PECVD): Utilizes plasma to lower the reaction temperature, making it suitable for temperature-sensitive substrates.
- Low-Pressure CVD (LPCVD): Operates under reduced pressure to achieve higher uniformity and purity.
- Metal-Organic CVD (MOCVD): Uses metal-organic precursors for depositing compound semiconductors.
- Atomic Layer Deposition (ALD): A variant of CVD that deposits materials layer by layer with atomic precision.
-
Advantages of CVD:
- High-Quality Films: Produces uniform, dense, and high-performance coatings.
- Versatility: Can deposit a wide range of materials, including metals, ceramics, and polymers.
- Scalability: Suitable for large-scale industrial applications.
- Precision: Allows for precise control over film thickness and composition.
-
Applications:
- Semiconductor Industry: Used for depositing thin films in the fabrication of integrated circuits, solar cells, and LEDs.
- Optoelectronics: Produces coatings for optical devices and displays.
- Protective Coatings: Provides wear-resistant and corrosion-resistant layers for tools and components.
- Nanotechnology: Enables the deposition of nanomaterials and nanostructures.
-
Challenges and Considerations:
- Precursor Selection: Precursors must be volatile, stable, and capable of producing the desired material.
- Process Control: Precise regulation of temperature, pressure, and gas flow is critical for consistent results.
- Substrate Compatibility: The substrate must withstand the reaction conditions without degrading.
- By-product Management: Efficient removal of by-products is necessary to maintain film quality and prevent contamination.
In summary, CVD is a powerful and flexible deposition technique that leverages chemical reactions to create high-quality thin films and coatings. Its ability to produce uniform, dense, and high-performance materials makes it indispensable in industries ranging from semiconductors to nanotechnology. By carefully controlling process parameters and selecting appropriate precursors, CVD can meet the diverse needs of modern material science and engineering.
Summary Table:
Aspect | Details |
---|---|
Basic Principle | Chemical reactions between gaseous precursors and a substrate surface. |
Process Steps | Precursor introduction, chemical reaction, deposition, by-product removal. |
Key Components | Reaction chamber, substrate, energy sources, precursors. |
Types of CVD | Thermal CVD, PECVD, LPCVD, MOCVD, ALD. |
Advantages | High-quality films, versatility, scalability, precision. |
Applications | Semiconductors, optoelectronics, protective coatings, nanotechnology. |
Challenges | Precursor selection, process control, substrate compatibility, by-product management. |
Discover how CVD can revolutionize your material science projects—contact our experts today!