Thermal evaporation is a versatile deposition technique widely used across various industries to create thin films of materials for functional and aesthetic purposes. It involves heating a source material in a high vacuum chamber until it vaporizes, allowing the vapor to condense onto a substrate, forming a thin, uniform film. This method is particularly effective for depositing metals like aluminum and silver, as well as more complex materials, and is used in applications ranging from electronics (OLEDs, solar cells) to consumer packaging and aerospace. The process is highly controllable, making it suitable for both simple and complex deposition tasks.
Key Points Explained:
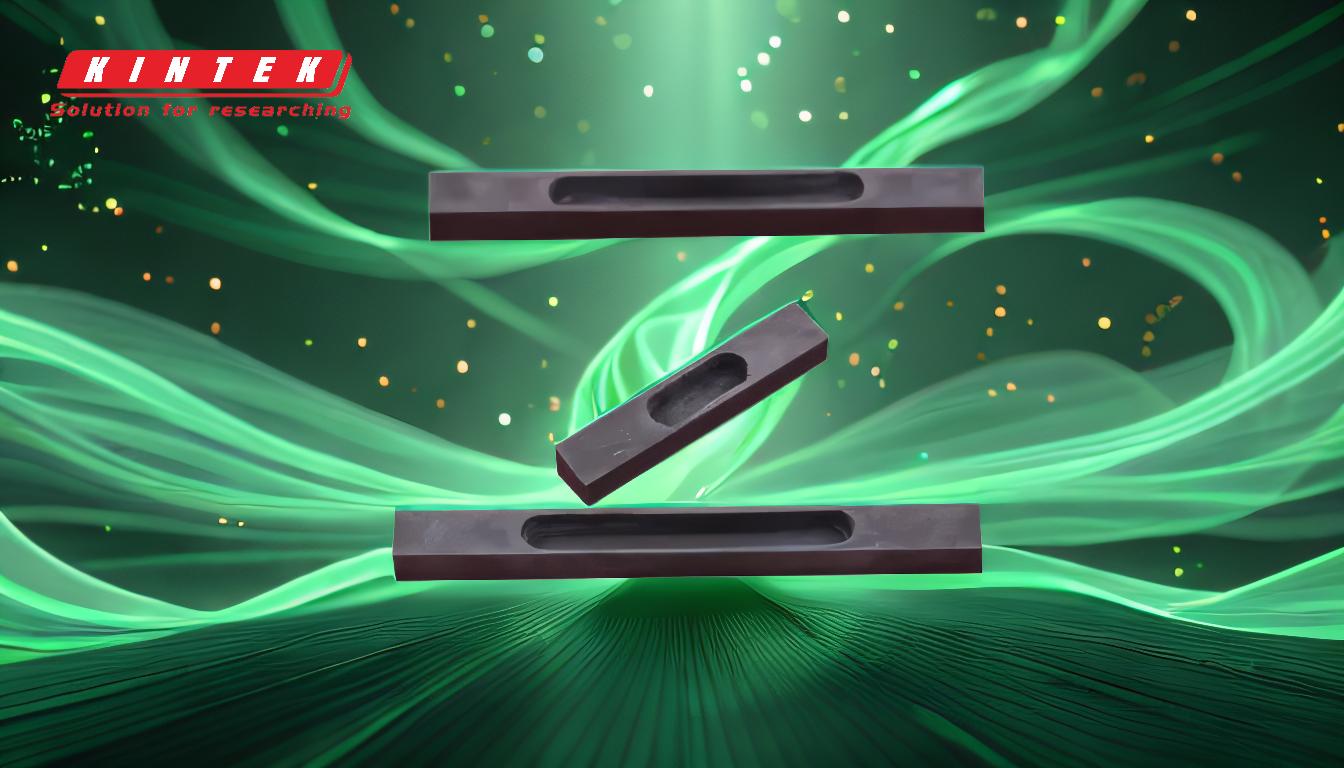
-
Applications of Thermal Evaporation:
- Electronics and Optoelectronics: Thermal evaporation is extensively used in the production of electronic devices such as OLEDs, thin-film transistors, and solar cells. It is particularly effective for creating electrical contacts and bonding layers in these devices.
- Packaging and Insulation: The technique is used to deposit thin metal films (e.g., aluminum) on polymers for applications like food packaging, heat and sound insulation, and decorative purposes.
- Aerospace and Safety: Thermal evaporation is employed in the manufacturing of NASA spacesuits, firefighter uniforms, and emergency blankets due to its ability to create durable, functional coatings.
- Optics: It is used to deposit coatings on lenses, such as anti-reflective layers and UV protection films.
-
Materials Deposited:
- Metals: Commonly deposited metals include aluminum, silver, nickel, chrome, and magnesium. These materials are chosen for their conductivity, reflectivity, or durability.
- Complex Materials: Thermal evaporation can also be used for co-deposition of multiple materials by controlling the temperature of individual crucibles, enabling the creation of more complex thin films.
-
Process Mechanism:
- The source material is heated in a high vacuum chamber to temperatures between 250 and 350 degrees Celsius, causing it to vaporize. The vapor then condenses onto a substrate, forming a thin film.
- The vacuum environment ensures minimal contamination and allows for precise control over the deposition process.
-
Advantages of Thermal Evaporation:
- High Purity: The vacuum environment minimizes impurities, resulting in high-quality thin films.
- Versatility: A wide range of materials can be deposited, from simple metals to complex compounds.
- Precision: The process allows for precise control over film thickness and uniformity, making it suitable for applications requiring exact specifications.
-
Comparison with Other Deposition Techniques:
- Sputtering: Unlike sputtering, which uses a plasma to dislodge atoms from a target material, thermal evaporation relies on heating to produce vapor. This makes thermal evaporation more suitable for materials that can withstand high temperatures.
- E-Beam Evaporation: E-beam evaporation is better suited for high-temperature materials like transition metal oxides (e.g., SiO2, HfO2, Al2O3), which are often used in UV coatings. Thermal evaporation, on the other hand, is more commonly used for metals and simpler compounds.
-
Industry-Specific Uses:
- Consumer Packaging: Aluminum films deposited on plastic packaging enhance barrier properties and aesthetics.
- Jewelry and Accessories: Thin-film coatings are applied for decorative purposes, providing a metallic or reflective finish.
- Microelectromechanical Systems (MEMS): Thermal evaporation is used to deposit thin films in MEMS devices, which require precise and uniform coatings.
Thermal evaporation is a critical technology in modern manufacturing, enabling the creation of thin films with specific properties for a wide range of applications. Its ability to deposit high-purity, uniform coatings makes it indispensable in industries ranging from electronics to aerospace.
Summary Table:
Aspect | Details |
---|---|
Applications | Electronics (OLEDs, solar cells), packaging, aerospace, optics, MEMS |
Materials Deposited | Metals (aluminum, silver, nickel), complex compounds, co-deposition |
Process Mechanism | Heating in a vacuum chamber (250-350°C), vapor condenses onto a substrate |
Advantages | High purity, versatility, precise control over film thickness and uniformity |
Comparison | Better for metals than sputtering; simpler than e-beam evaporation |
Want to learn more about thermal evaporation and its applications? Contact us today for expert advice and solutions!