Thermal Vapour Deposition (TVD) is a thin film deposition technique where a solid material is heated in a high vacuum chamber until it vaporizes, forming a vapor stream that travels to a substrate and condenses into a thin film. This process relies on thermal energy to transform the source material into a gaseous state, which then deposits onto the substrate surface. TVD is widely used in industries requiring precise and uniform thin film coatings, such as electronics, optics, and semiconductors. The process is characterized by its simplicity, cost-effectiveness, and ability to produce high-purity films.
Key Points Explained:
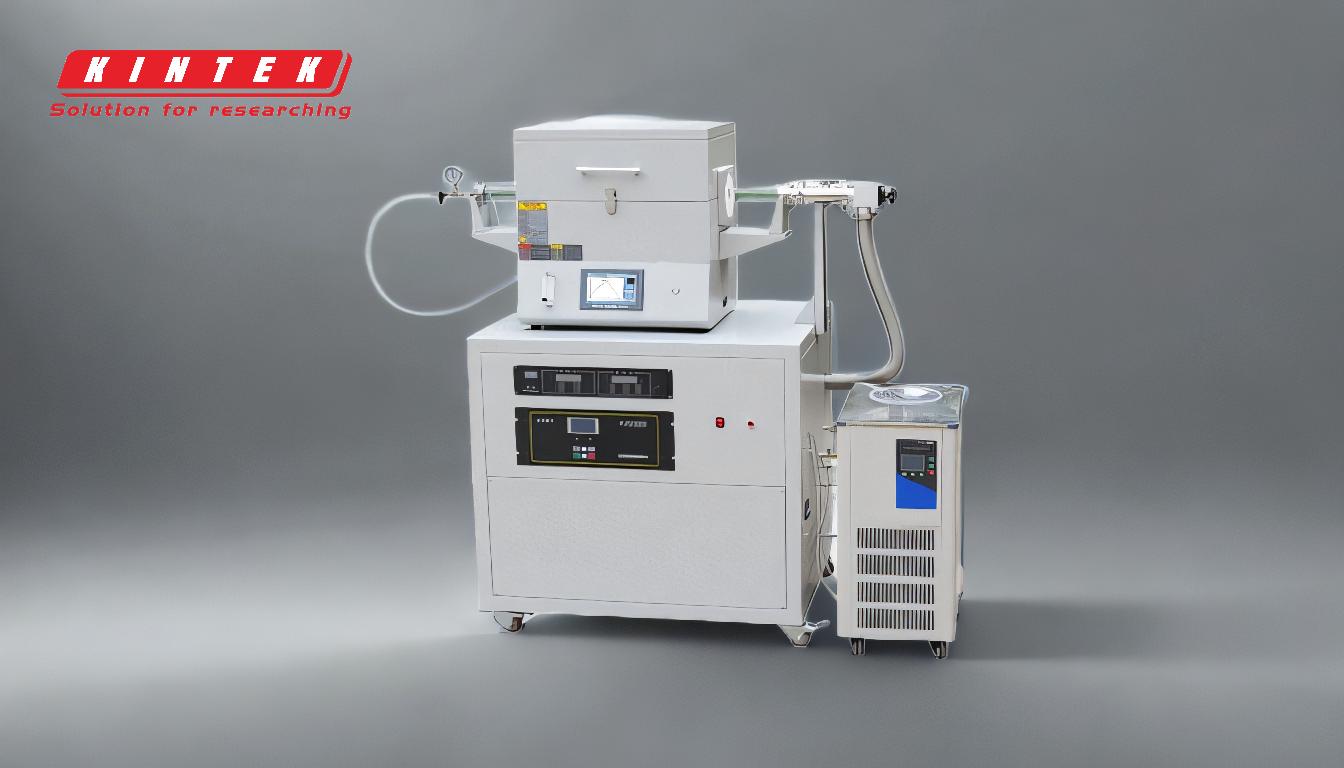
-
Process Overview:
- Thermal Vapour Deposition involves heating a solid material in a high vacuum chamber until it vaporizes.
- The vaporized material forms a vapor stream that travels through the vacuum and deposits onto a substrate, forming a thin film.
- This process is commonly used for applications requiring precise and uniform coatings, such as in electronics and optics.
-
Heating Mechanism:
- The source material is heated using an electric heater, tungsten heating element, or electron beam.
- Heating temperatures typically range from 250 to 350 degrees Celsius, depending on the material's properties.
- The heat transforms the solid material into a gaseous state, creating vapor pressure within the chamber.
-
Vacuum Environment:
- The process occurs in a high vacuum chamber to minimize interactions between the vapor stream and other atoms or molecules.
- The vacuum ensures the vapor stream travels unimpeded, reducing contamination and improving film purity.
- Even low vapor pressure is sufficient to create a vapor cloud in the vacuum environment.
-
Deposition on Substrate:
- The vapor stream travels through the chamber and condenses onto the substrate surface.
- The deposited material forms a thin film, which adheres to the substrate due to physical or chemical bonding.
- The thickness and uniformity of the film can be controlled by adjusting parameters such as heating temperature, deposition time, and substrate positioning.
-
Advantages of Thermal Vapour Deposition:
- High Purity: The vacuum environment minimizes contamination, resulting in high-purity films.
- Uniform Coatings: The process allows for precise control over film thickness and uniformity.
- Versatility: Suitable for a wide range of materials, including metals, semiconductors, and dielectrics.
- Cost-Effectiveness: Simple setup and operation make it a cost-effective choice for many applications.
-
Applications:
- Electronics: Used for depositing conductive and insulating layers in semiconductor devices.
- Optics: Applied in the production of anti-reflective coatings, mirrors, and optical filters.
- Decorative Coatings: Utilized for creating thin films on jewelry, glass, and other decorative items.
- Barrier Layers: Employed to create protective coatings that prevent corrosion or gas diffusion.
-
Comparison with Other Deposition Techniques:
- Thermal Evaporation vs. Sputtering: Thermal evaporation uses thermal energy to vaporize the source material, while sputtering involves bombarding the target material with ions to eject atoms.
- Thermal Evaporation vs. Chemical Vapour Deposition (CVD): TVD relies on physical vaporization, whereas CVD involves chemical reactions to deposit the film.
- Thermal Evaporation vs. Ion Beam Deposition: TVD is simpler and more cost-effective, but ion beam deposition offers better control over film properties and adhesion.
-
Limitations:
- Limited to materials that can be vaporized at achievable temperatures.
- May not be suitable for materials with high melting points or those prone to thermal decomposition.
- Requires a high vacuum environment, which can increase equipment and operational costs.
Thermal Vapour Deposition is a versatile and widely used technique for thin film deposition, offering high purity, uniformity, and cost-effectiveness. Its applications span various industries, making it a critical process in modern manufacturing and technology development.
Summary Table:
Aspect | Details |
---|---|
Process | Heating a solid material in a vacuum to vaporize and deposit as a thin film. |
Heating Mechanism | Electric heater, tungsten element, or electron beam (250–350°C). |
Vacuum Environment | High vacuum minimizes contamination, ensuring film purity. |
Applications | Electronics, optics, decorative coatings, barrier layers. |
Advantages | High purity, uniform coatings, versatility, cost-effectiveness. |
Limitations | Limited to vaporizable materials; requires high vacuum. |
Discover how Thermal Vapour Deposition can enhance your projects—contact our experts today!