A tube furnace is a versatile heating device widely used in various scientific and industrial applications. It is designed to heat samples contained within a work tube, providing precise temperature control and uniform heating. Tube furnaces are commonly employed in materials research, chemistry, nanotechnology, and other fields for processes such as annealing, thermal decomposition, chemical vapor deposition (CVD), sintering, and more. They offer advantages like uniform temperature distribution, space-saving design, ease of operation, and low energy consumption. Tube furnaces are also used in specialized applications like graphitization, calcining, and oxidation, making them indispensable in both research and industrial settings.
Key Points Explained:
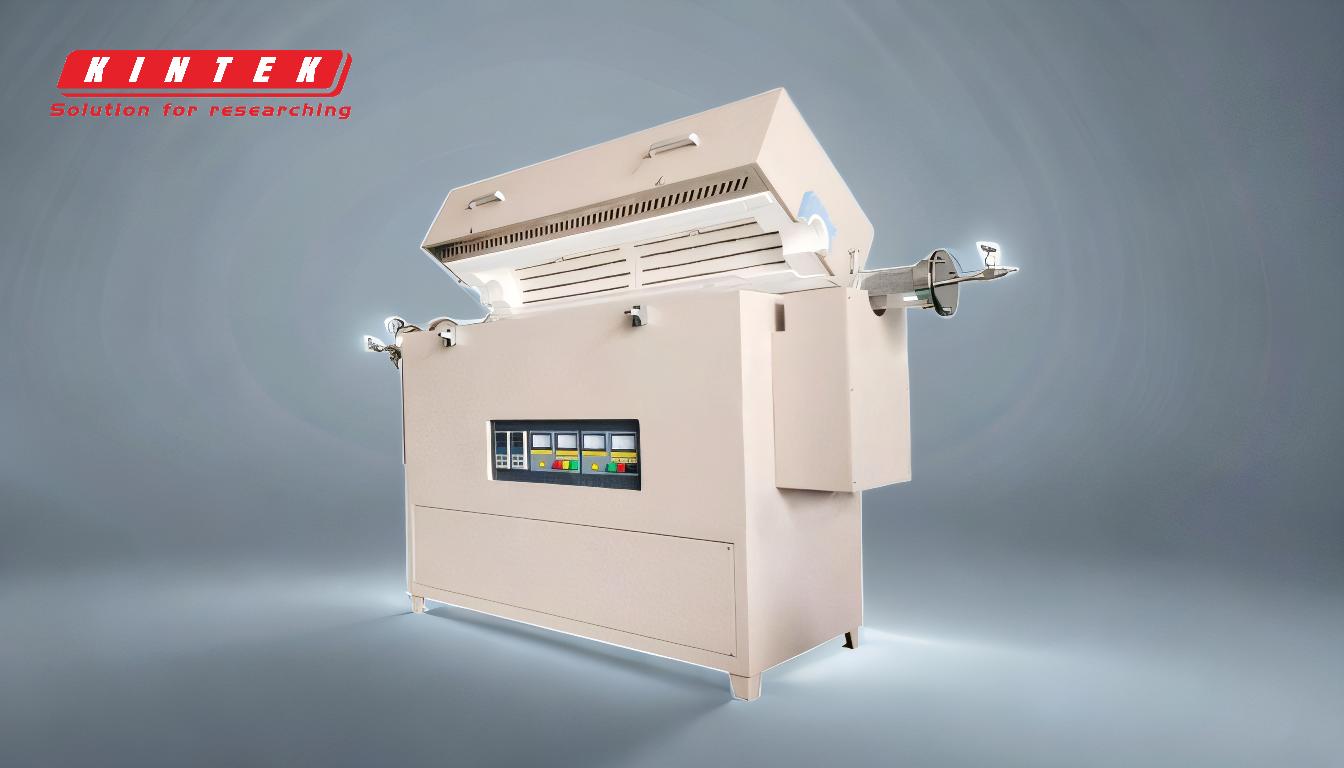
-
Primary Applications of Tube Furnaces:
- Materials Research: Tube furnaces are extensively used in materials science for processes like annealing, sintering, and thermal decomposition. These processes are crucial for studying and developing new materials with specific properties.
- Chemistry and Nanotechnology: In chemical synthesis and nanotechnology, tube furnaces facilitate processes such as chemical vapor deposition (CVD), which is essential for creating thin films and nanomaterials.
- Industrial Processes: Industries utilize tube furnaces for brazing, ceramic firing, degassing, and graphitizing, among other applications.
-
Key Processes Enabled by Tube Furnaces:
- Annealing: A heat treatment process that alters the physical and sometimes chemical properties of a material to increase its ductility and reduce its hardness.
- Chemical Vapor Deposition (CVD): A method used to produce high-quality, high-performance solid materials, typically under vacuum.
- Sintering: The process of compacting and forming a solid mass of material by heat or pressure without melting it to the point of liquefaction.
- Thermal Decomposition: The breakdown of chemical compounds by heat, often used in the production of ceramics and other materials.
-
Advantages of Tube Furnaces:
- Uniform Temperature Distribution: Adjustable heating devices around the work tube ensure even heating, which is critical for consistent results.
- Space-Saving Design: Tube furnaces are compact and efficient, making them ideal for laboratories and industrial settings with limited space.
- Ease of Operation: Advanced control systems allow for intelligent operation and remote monitoring, simplifying the user experience.
- Low Energy Consumption: Designed to be energy-efficient, tube furnaces help reduce operational costs over time.
-
Specialized Types of Tube Furnaces:
- Vertical Tube Furnaces: Ideal for processes requiring precise temperature control and uniform heating of vertically aligned samples. They are commonly used in materials research and nanotechnology.
- Rotary Tube Furnaces: Suitable for applications like calcining, which involve the continuous throughput of loose materials and oxidation processes.
- Graphite Tube Furnaces: Used in graphitization treatment, graphene growth, and carbon nanotube preparation, among other specialized applications.
-
Industries and Fields Utilizing Tube Furnaces:
- Materials Science: For developing and testing new materials with specific thermal and chemical properties.
- Chemical Industry: For synthesizing new compounds and materials through controlled thermal processes.
- Nanotechnology: For creating nanostructures and nanomaterials with precise control over their properties.
- Industrial Manufacturing: For processes like brazing, ceramic firing, and degassing, which are essential in the production of various industrial components.
-
Operational Mechanism:
- Work Tube: Samples are placed inside a work tube, which is then installed into the furnace. The furnace heats the outside of the work tube, gradually transferring heat to the samples inside.
- Temperature Control: Users can set specific temperatures on the furnace controller, ensuring precise control over the heating process.
-
Environmental and Atmospheric Control:
- Controlled Atmospheres: Tube furnaces can operate under various atmospheric conditions, including inert gases, vacuum, or specific gas mixtures, which is crucial for processes like heat treatment and powder forming.
- Specialized Applications: For materials like tungsten and molybdenum, tube furnaces are used in sintering and other high-temperature processes.
In summary, tube furnaces are essential tools in both research and industrial settings, offering precise temperature control and uniform heating for a wide range of applications. Their versatility, efficiency, and ease of operation make them indispensable in fields ranging from materials science to nanotechnology. For more detailed information, you can explore the tube furnace topic.
Summary Table:
Aspect | Details |
---|---|
Primary Applications | Materials research, chemistry, nanotechnology, industrial processes |
Key Processes | Annealing, CVD, sintering, thermal decomposition |
Advantages | Uniform heating, space-saving, easy operation, low energy consumption |
Specialized Types | Vertical, rotary, graphite tube furnaces |
Industries | Materials science, chemical industry, nanotechnology, industrial manufacturing |
Operational Mechanism | Work tube heating with precise temperature control |
Atmospheric Control | Inert gases, vacuum, or specific gas mixtures for specialized applications |
Ready to enhance your lab or industrial processes with a tube furnace? Contact us today to find the perfect solution!