Vacuum induction melting (VIM) is a specialized metallurgical process used primarily for producing high-performance alloys and metals under controlled conditions. It is widely employed in industries such as aerospace, automotive, and nuclear energy due to its ability to produce materials with superior mechanical properties, cleanliness, and precision. The process involves melting metals in a vacuum or inert atmosphere to prevent contamination and oxidation, making it ideal for creating high-temperature alloys, reactive metals, and precision components. VIM is also used to produce consumable electrodes for secondary remelting processes and master alloys for precision casting.
Key Points Explained:
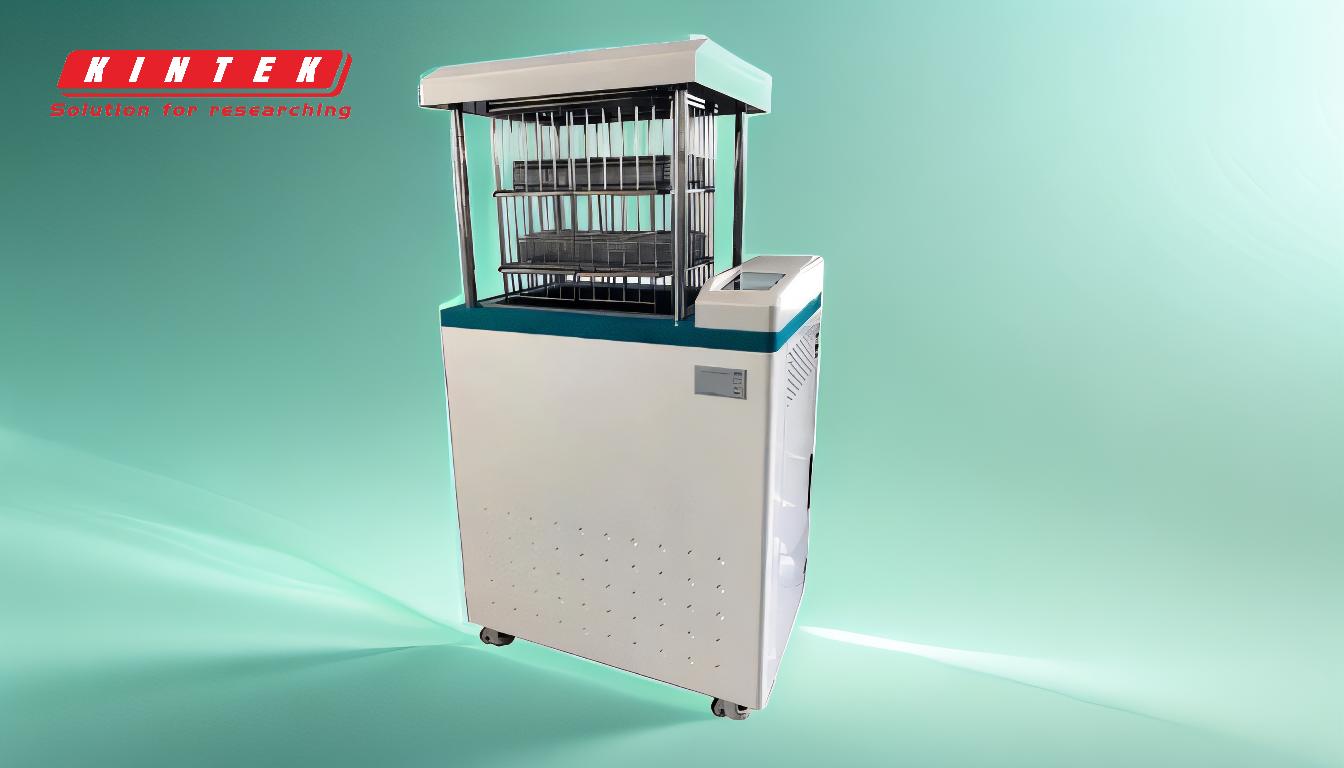
-
Primary Applications of Vacuum Induction Melting:
- High-Temperature Alloys: VIM is extensively used to smelt nickel-based, cobalt-based, and iron-based alloys, which are critical for applications requiring high strength and thermal resistance, such as turbine blades and jet engines.
- Elastic and Expansion Alloys: The process ensures the production of materials with precise mechanical properties, making it suitable for applications like springs and sensors.
- Reactive and Refractory Metals: VIM is ideal for melting reactive metals like titanium and refractory materials such as stainless steel, which are prone to contamination in open-air environments.
-
Process and Equipment:
- Vacuum Melting Furnace: The core equipment used in VIM is a vacuum melting furnace, which operates under vacuum or protective atmospheres to prevent oxidation and contamination.
- Temperature Control: A thermocouple is used to measure the temperature of the molten metal, ensuring precise control over the melting process.
- Casting and Pouring: The molten metal is poured into molds using a turning mechanism, enabling the production of ingots, precision castings, or consumable electrodes.
-
Advantages of Vacuum Induction Melting:
- Cleanliness: The vacuum environment eliminates impurities and gases, resulting in high-purity metals with improved mechanical properties.
- Precision: The process allows for precise control over alloy composition and temperature, ensuring consistent material quality.
- Versatility: VIM can handle a wide range of materials, from high-temperature alloys to reactive metals, making it suitable for diverse industrial applications.
-
Industrial Applications:
- Aerospace and Defense: VIM is critical for producing high-temperature alloys used in jet engines, rocket components, and missile systems.
- Automotive: The process is used to manufacture durable and lightweight components for high-performance vehicles.
- Nuclear Energy: VIM-produced materials are used in reactors and other equipment requiring high strength and resistance to extreme conditions.
-
Secondary Remelting and Precision Casting:
- Consumable Electrodes: VIM produces high-quality electrodes for secondary remelting processes like vacuum arc remelting (VAR) and electroslag remelting (ESR).
- Master Alloys: The process is used to create master alloys for precision casting, ensuring the production of high-performance components.
-
Operational Flexibility:
- Cyclic and Semi-Continuous Operation: VIM furnaces can operate in cyclic or semi-continuous modes, allowing for efficient production of multiple batches.
- In-Process Adjustments: The process allows for sampling, alloy composition adjustments, and temperature monitoring without breaking the vacuum, ensuring consistent quality.
-
Economic and Production Benefits:
- Cost-Effectiveness: Despite the high initial investment, VIM is cost-effective for high-volume production of high-performance materials.
- High-Quality Joints: The process is particularly beneficial for vacuum brazing, producing strong and clean joints for precision components.
In summary, vacuum induction melting is a versatile and essential process for producing high-performance alloys and metals. Its ability to operate under controlled conditions ensures the production of materials with superior properties, making it indispensable in industries like aerospace, automotive, and nuclear energy. The use of advanced equipment like the vacuum melting furnace further enhances the precision and efficiency of the process.
Summary Table:
Application | Description |
---|---|
High-Temperature Alloys | Used for nickel, cobalt, and iron-based alloys in turbine blades and jet engines. |
Elastic and Expansion Alloys | Produces materials for springs, sensors, and precision components. |
Reactive and Refractory Metals | Ideal for melting titanium and stainless steel in contamination-free environments. |
Aerospace and Defense | Critical for jet engines, rocket components, and missile systems. |
Automotive | Manufactures durable, lightweight components for high-performance vehicles. |
Nuclear Energy | Produces materials for reactors and equipment requiring high strength. |
Learn how vacuum induction melting can enhance your production process—contact our experts today!