The vapor deposition process, specifically chemical vapor deposition (CVD), is a sophisticated manufacturing technique used to deposit thin films of material onto a substrate. This process involves several key steps, including the transport of gaseous reactants to the substrate surface, adsorption of these reactants, chemical reactions that lead to film formation, and the removal of by-products. CVD is distinguished from physical vapor deposition (PVD) by its reliance on chemical reactions rather than physical processes. It is widely used in various industries to create high-quality, durable coatings and films for applications ranging from electronics to protective coatings.
Key Points Explained:
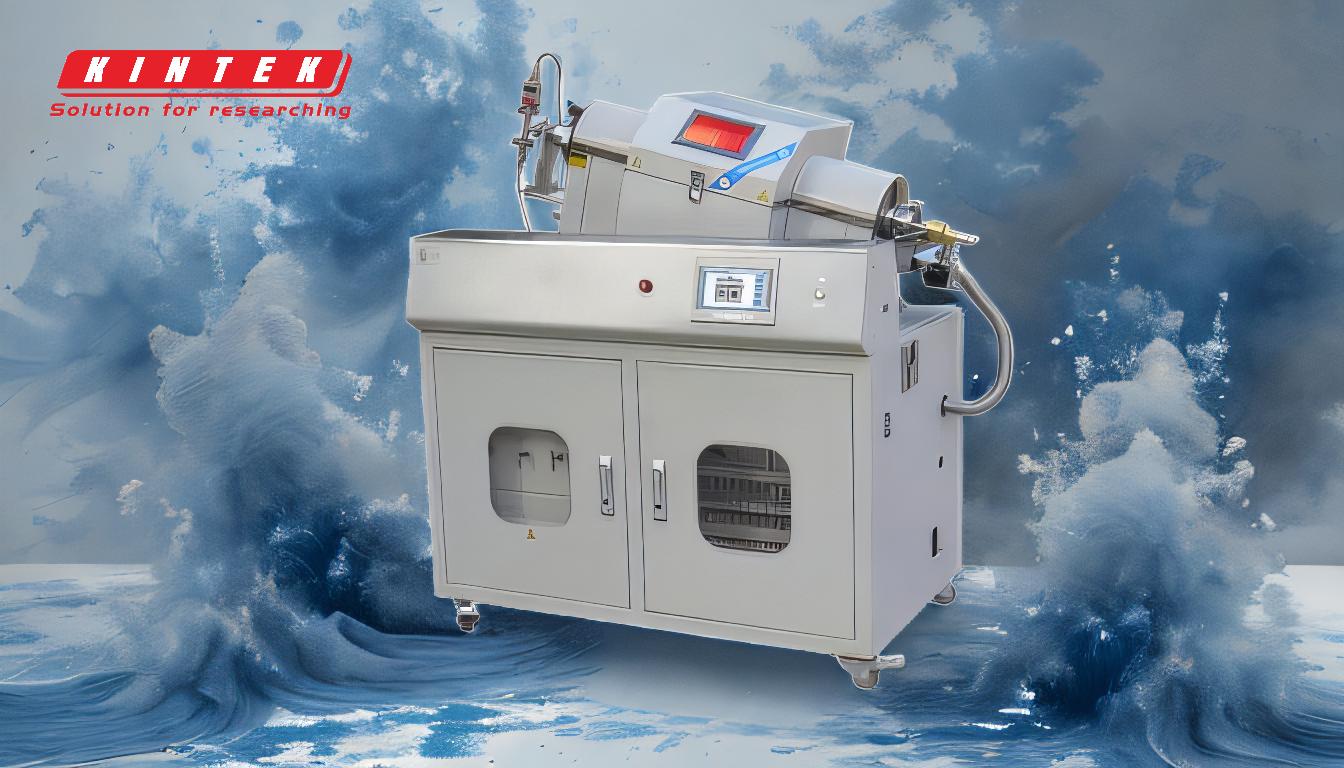
-
Definition of Chemical Vapor Deposition (CVD):
- CVD is a thin-film deposition process where a solid film is formed on a heated substrate through chemical reactions in the vapor phase. This process typically involves atoms, molecules, or a combination of both reacting on the substrate surface to form a thin, solid film. Unlike physical vapor deposition (PVD), which relies on physical processes like evaporation or sputtering, CVD is characterized by surface-mediated chemical reactions.
-
Steps Involved in CVD:
- Transport of Reacting Gaseous Species: The process begins with the transport of gaseous reactants to the substrate surface. These reactants are typically volatile compounds that can easily vaporize.
- Adsorption on the Surface: Once the gaseous species reach the substrate, they adsorb onto its surface. This step is crucial as it prepares the reactants for the subsequent chemical reactions.
- Surface-Catalyzed Reactions: The adsorbed species undergo chemical reactions on the substrate surface, often catalyzed by the surface itself. These reactions lead to the formation of the desired solid film.
- Surface Diffusion to Growth Sites: The reacted species then diffuse across the surface to specific growth sites where the film will nucleate and grow.
- Nucleation and Growth of the Film: At the growth sites, the film begins to nucleate and grow, forming a continuous layer over the substrate.
- Desorption of By-Products: Finally, any gaseous by-products formed during the reaction desorb from the surface and are transported away, leaving behind the deposited film.
-
Applications of CVD:
- CVD is extensively used in the semiconductor industry to deposit thin films of materials like silicon dioxide, silicon nitride, and various metals. It is also employed in the production of protective coatings, optical coatings, and even in the creation of complex nanostructures.
-
Advantages of CVD:
- High-Quality Films: CVD can produce films with excellent uniformity, purity, and adherence to the substrate.
- Versatility: It can deposit a wide range of materials, including metals, ceramics, and polymers.
- Complex Geometries: CVD can coat complex shapes and intricate geometries, making it suitable for a variety of applications.
-
Comparison with Physical Vapor Deposition (PVD):
- While both CVD and PVD are used to deposit thin films, they differ fundamentally in their mechanisms. PVD relies on physical processes like evaporation or sputtering, whereas CVD involves chemical reactions. This distinction makes CVD particularly suitable for applications requiring precise control over film composition and properties.
-
Polymerization via CVD:
- CVD can also be used to polymerize materials directly on a substrate. For example, poly(paraxylene) can be deposited via CVD in a vacuum chamber, where the monomer vapor polymerizes upon contact with the substrate, forming a thin polymer film.
-
Environmental and Safety Considerations:
- CVD processes often involve the use of hazardous chemicals and high temperatures, necessitating stringent safety protocols. Proper ventilation, waste management, and personal protective equipment are essential to ensure safe operation.
In summary, the chemical vapor deposition process is a versatile and powerful technique for depositing thin films with high precision and quality. Its reliance on chemical reactions allows for the creation of films with tailored properties, making it indispensable in modern manufacturing and technology. For more detailed information on the topic, you can refer to the chemical vapor deposition process.
Summary Table:
Aspect | Details |
---|---|
Definition | CVD deposits thin films via chemical reactions in the vapor phase. |
Key Steps | 1. Transport of gases 2. Adsorption 3. Surface reactions 4. Film growth |
Applications | Semiconductors, protective coatings, optical films, nanostructures. |
Advantages | High-quality films, versatility, ability to coat complex geometries. |
Comparison with PVD | CVD uses chemical reactions; PVD relies on physical processes. |
Safety Considerations | Requires handling of hazardous chemicals and high temperatures. |
Discover how CVD can elevate your manufacturing processes—contact us today for expert guidance!