End mills are critical cutting tools used in milling applications, and the choice of material significantly impacts their performance, durability, and precision. Tungsten carbide is the most commonly used material for end mills due to its exceptional hardness, wear resistance, and ability to withstand high temperatures. It is typically composed of tungsten carbide powder combined with a binder material, such as cobalt or nickel, which provides the necessary toughness and structural integrity. This combination ensures that end mills can handle demanding machining tasks while maintaining sharp cutting edges over extended periods.
Key Points Explained:
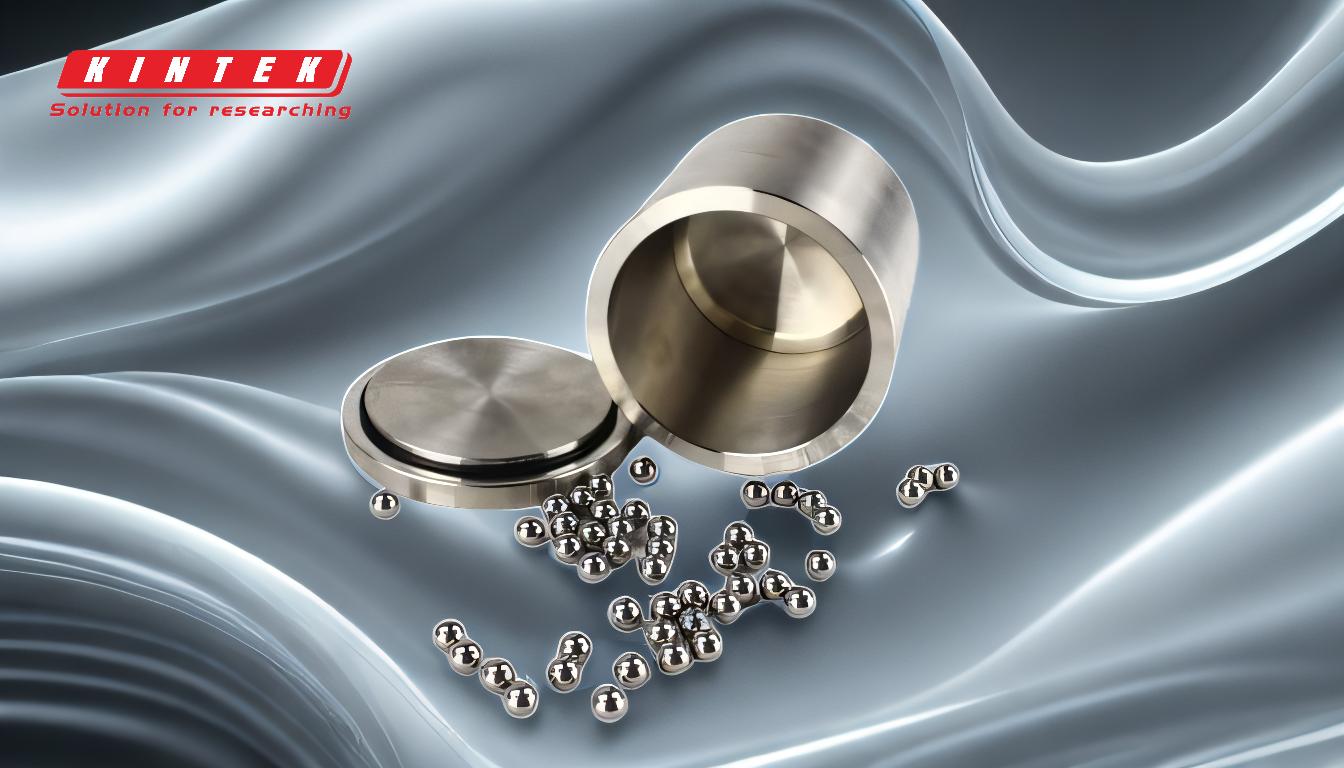
-
Tungsten Carbide as the Primary Material:
- Tungsten carbide is the dominant material used in end mills due to its superior properties:
- Hardness: Tungsten carbide is one of the hardest materials available, second only to diamond. This hardness allows end mills to cut through tough materials like steel, stainless steel, and titanium with ease.
- Wear Resistance: The material's resistance to abrasion ensures that end mills maintain their cutting edges for longer periods, reducing the need for frequent replacements.
- High-Temperature Stability: Tungsten carbide retains its strength and hardness even at elevated temperatures, making it ideal for high-speed machining operations.
- Tungsten carbide is the dominant material used in end mills due to its superior properties:
-
Composition of Tungsten Carbide End Mills:
- Tungsten carbide end mills are not made from pure tungsten carbide but are a composite material:
- Tungsten Carbide Powder: This forms the bulk of the material and provides the hardness and wear resistance.
-
Binder Material: Typically, cobalt or nickel is used as a binder to hold the tungsten carbide particles together. The binder adds toughness and prevents the tool from being too brittle.
- Cobalt Binders: More commonly used due to their excellent balance of hardness and toughness. Cobalt also enhances the material's thermal conductivity, helping to dissipate heat during machining.
- Nickel Binders: Used in applications where corrosion resistance is critical, such as in wet or chemically aggressive environments.
- Tungsten carbide end mills are not made from pure tungsten carbide but are a composite material:
-
Advantages of Tungsten Carbide End Mills:
- Long Tool Life: The combination of hardness and wear resistance ensures that tungsten carbide end mills last significantly longer than those made from high-speed steel (HSS).
- High Precision: The material's stability allows for precise machining, even in complex geometries and tight tolerances.
- Versatility: Tungsten carbide end mills can be used to machine a wide range of materials, including metals, composites, and plastics.
-
Applications of Tungsten Carbide End Mills:
- Metalworking: Ideal for machining hard metals like stainless steel, titanium, and hardened steels.
- Aerospace and Automotive Industries: Used extensively for high-precision components that require durability and precision.
- Mold and Die Making: The material's ability to maintain sharp edges makes it suitable for detailed work in mold and die manufacturing.
-
Considerations for Purchasers:
- When selecting tungsten carbide end mills, consider the following factors:
- Coating Options: Many end mills are coated with materials like titanium nitride (TiN) or aluminum titanium nitride (AlTiN) to further enhance performance and tool life.
- Geometry and Design: The shape and design of the end mill (e.g., number of flutes, helix angle) should match the specific machining task.
- Binder Type: Choose between cobalt or nickel binders based on the application's requirements for toughness and corrosion resistance.
- When selecting tungsten carbide end mills, consider the following factors:
In summary, tungsten carbide end mills, made from a combination of tungsten carbide powder and cobalt or nickel binders, are the preferred choice for high-performance machining due to their hardness, wear resistance, and versatility. Understanding the material composition and its advantages helps in selecting the right tool for specific applications, ensuring optimal performance and cost-effectiveness.
Summary Table:
Key Feature | Details |
---|---|
Primary Material | Tungsten carbide powder with cobalt or nickel binders |
Hardness | Second only to diamond; ideal for cutting tough materials |
Wear Resistance | Maintains sharp edges, reducing replacement frequency |
High-Temperature Stability | Retains strength and hardness even at elevated temperatures |
Applications | Metalworking, aerospace, automotive, mold and die making |
Coating Options | TiN, AlTiN for enhanced performance and tool life |
Binder Types | Cobalt (toughness) or nickel (corrosion resistance) |
Ready to optimize your machining process? Contact us today to find the perfect tungsten carbide end mills for your needs!