Sintering is a versatile manufacturing process used to create dense, durable materials from powders. It is applied to a wide range of materials, including metals, ceramics, polymers, and glass. Each material category has unique properties and applications, making sintering a critical process in industries such as aerospace, automotive, electronics, and medical devices. The process involves heating powdered materials below their melting point to fuse particles, resulting in improved mechanical properties and structural integrity. This summary explores the key materials sintered, their characteristics, and their applications.
Key Points Explained:
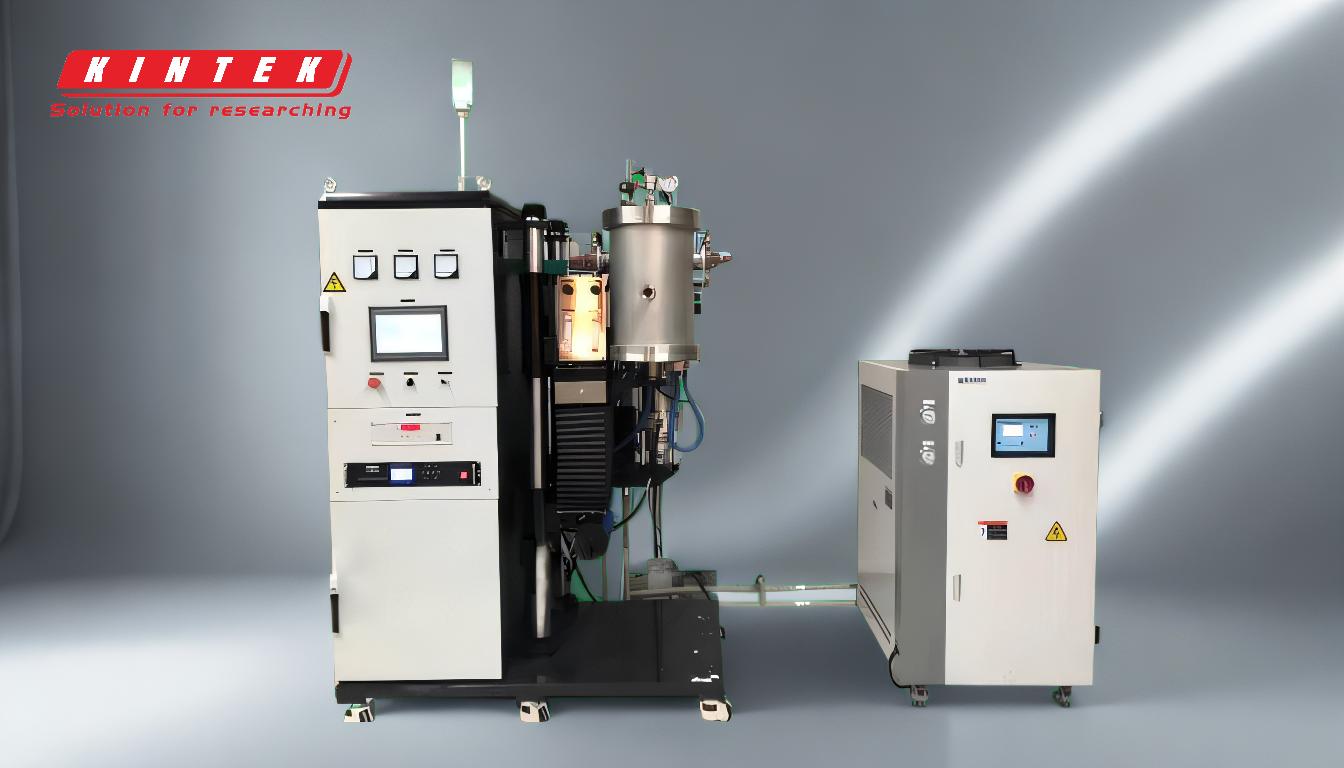
-
Metals Sintered:
- Common Metals: Stainless steel, aluminum, nickel, copper, titanium alloy, brass, bronze, and Inconel 718 are frequently sintered. These metals are chosen for their strength, corrosion resistance, and thermal conductivity.
- Applications: Sintered metals are used in small components like gears, pulleys, and bearings, as well as in additive manufacturing for creating complex, high-performance parts.
- Advantages: Sintering allows for precise control over the manufacturing process, resulting in consistent and high-quality products. It also enables the production of intricate shapes that are difficult to achieve with traditional methods.
-
Ceramics Sintered:
- Common Ceramics: Alumina, aluminum nitride, zirconia, silicon nitride, boron nitride, silicon carbide, magnesium oxide, lime, beryllium oxide, and iron oxide are widely used in ceramic sintering.
- Applications: Sintered ceramics are ideal for high-temperature and wear-resistant components, such as bearings, cutting tools, and electronic substrates. They are also used in medical implants and aerospace applications.
- Challenges: Some ceramic materials, like silicon nitride and boron nitride, have low water affinity and require organic additives during the pre-sintering stage to improve processing.
-
Glass Materials Sintered:
- Common Glass Types: Ceramic glazes, silica glass, lead glass, and sintered glass slabs made from fused silica glass powder are sintered for various applications.
- Applications: Sintered glass is used in optical components, laboratory equipment, and decorative items. It is also employed in the production of advanced ceramics and composites.
- Properties: Sintered glass offers excellent thermal stability, transparency, and chemical resistance, making it suitable for demanding environments.
-
Polymers Sintered:
- Common Polymers: Polymers are sintered for rapid prototyping and filter manufacturing. Materials like nylon and polyetheretherketone (PEEK) are often used.
- Applications: Sintered polymers are used in 3D printing, creating lightweight and durable parts for industries such as automotive, aerospace, and consumer goods.
- Advantages: Polymer sintering allows for the production of complex geometries with high precision and minimal material waste.
-
Advanced Sintering Techniques:
- Spark Plasma Sintering (SPS): This technique can sinter materials that are difficult to densify, such as highly reactive systems. SPS uses high heating rates and shorter holding times to prevent the formation of undesirable phases.
- Applications: SPS is used for advanced materials like ceramics, composites, and nanocrystalline metals, which require precise control over microstructure and properties.
-
3D Printed Materials Sintered:
- Common Materials: Pyrex, bronze, copper, 316L stainless steel, 17-4PH stainless steel, and Inconel 718 are sintered in 3D printing processes.
- Applications: These materials are used in additive manufacturing to produce high-strength, lightweight components for aerospace, medical, and industrial applications.
- Benefits: Sintering in 3D printing allows for the creation of complex, custom-designed parts with excellent mechanical properties.
By understanding the materials commonly sintered and their applications, manufacturers can select the appropriate materials and techniques to meet specific performance requirements. Sintering continues to evolve, offering new possibilities for material innovation and advanced manufacturing.
Summary Table:
Material Category | Common Examples | Applications | Advantages |
---|---|---|---|
Metals | Stainless steel, aluminum, titanium alloy | Gears, bearings, additive manufacturing | Precise control, intricate shapes |
Ceramics | Alumina, zirconia, silicon carbide | Bearings, cutting tools, medical implants | High-temperature resistance |
Polymers | Nylon, PEEK | 3D printing, rapid prototyping | Complex geometries, minimal waste |
Glass | Silica glass, lead glass | Optical components, lab equipment | Thermal stability, chemical resistance |
Advanced Techniques | Spark Plasma Sintering (SPS) | Advanced ceramics, composites | Precise microstructure control |
3D Printed Materials | 316L stainless steel, Inconel 718 | Aerospace, medical components | High-strength, lightweight parts |
Want to learn more about sintering materials for your industry? Contact us today for expert guidance!