PVD (Physical Vapor Deposition) coating is a versatile and widely used technique for applying thin, durable, and high-performance coatings to various substrates. The materials used in PVD coatings are selected based on their unique properties and the specific requirements of the application. Common materials include Cr2N, TiN, ZnSn, AlCr, and ITO thin films, each serving distinct industries such as watches, electronics, automotive, and semiconductors. Additionally, PVD coatings can utilize metallic alloys, ceramics, bio-glasses, polymers, and even real gold for specialized applications. The choice of material depends on factors like hardness, wear resistance, conductivity, and aesthetic appeal. PVD processes, such as thermal vapor deposition and ion beam sputtering, ensure the deposition of pure, uniform, and adherent films.
Key Points Explained:
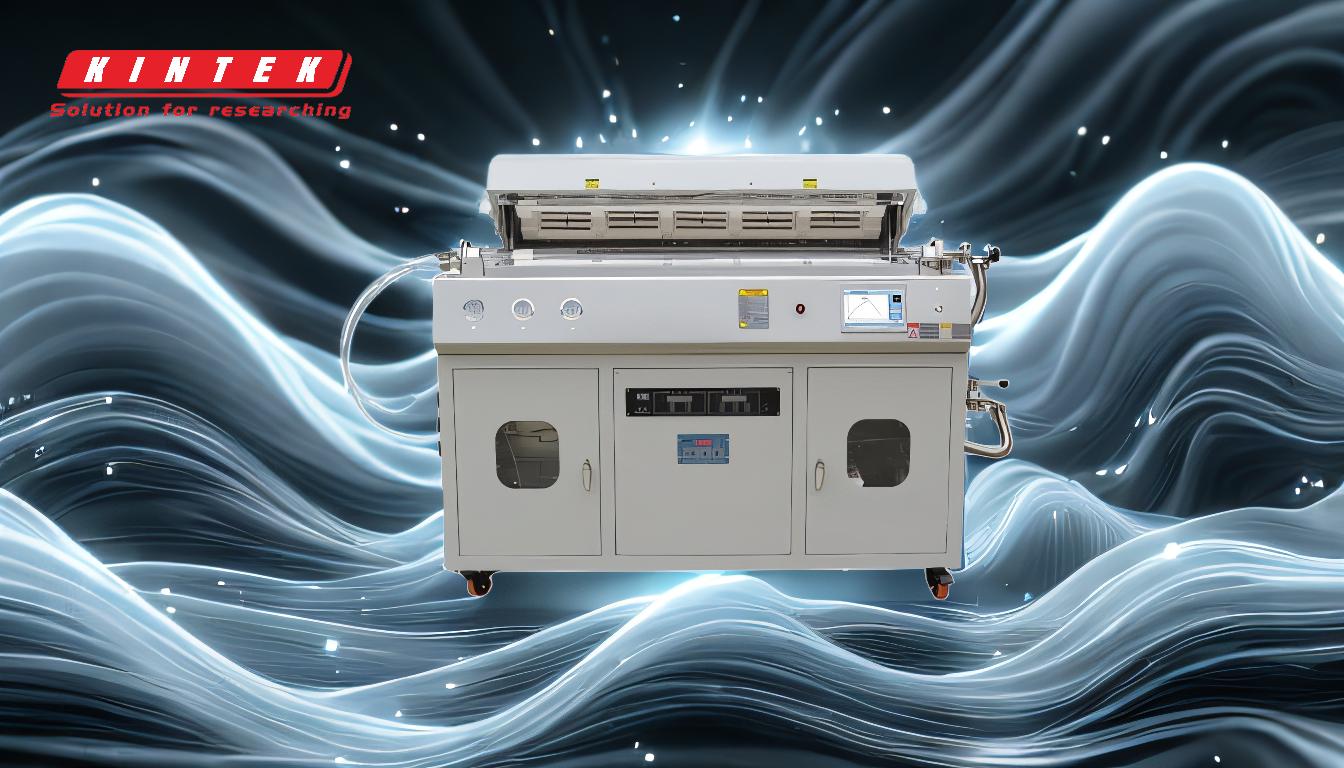
-
Common PVD Coating Materials and Their Applications:
- Cr2N: Used in watches and jewelry for its durability and aesthetic appeal.
- TiN (Titanium Nitride): Commonly applied to phones, glasses, and hardware parts for its hardness and corrosion resistance.
- ZnSn (Zinc Tin Oxide): Utilized in low-emissivity (low-e) windows and glass for its thermal insulation properties.
- AlCr (Aluminum Chromium): Extends the service life of tools and machine parts due to its wear resistance.
- ITO (Indium Tin Oxide): Essential in LCDs, plasma displays, and touch panels for its electrical conductivity and optical transparency.
-
Specialized Materials for Unique Applications:
- Real Gold PVD Coatings: Used for luxury items, with options like 24k, 18k, 14k, or 9k gold applied to surfaces for a premium finish.
- Metallic Alloys and Ceramics: Provide durable protection and are used in industries requiring high-performance coatings.
- Bio-glasses and Polymers: Offer biocompatibility and are used in medical and dental applications.
- Engineered Plastic Materials: Used for lightweight and corrosion-resistant coatings in various industries.
-
PVD Coating Processes:
- Thermal Vapor Deposition: Involves heating the material until it vaporizes, forming a thin, uniform film on the substrate.
- Molecular Beam Epitaxy: A precise method for depositing single-crystal films, often used in semiconductor manufacturing.
- Ion Beam Sputtering Deposition: Produces high-purity, adherent films by bombarding a target material with ions.
-
Material Selection Criteria:
- Hardness and Wear Resistance: Critical for tools and machine parts (e.g., AlCr).
- Electrical Conductivity: Essential for electronic components (e.g., ITO).
- Optical Properties: Important for applications like low-e glass (e.g., ZnSn).
- Aesthetic Appeal: Key for decorative items (e.g., Cr2N and real gold coatings).
-
Advantages of PVD Coatings:
- Thin and Uniform Films: Achieved through atom-by-atom deposition, ensuring precise control over coating thickness.
- Adhesion and Durability: Strong bonding to substrates enhances longevity and performance.
- Versatility: Suitable for a wide range of materials and industries, from consumer electronics to industrial tools.
By understanding the materials and processes involved in PVD coatings, purchasers can make informed decisions based on the specific needs of their applications, ensuring optimal performance and cost-effectiveness.
Summary Table:
Material | Properties | Applications |
---|---|---|
Cr2N | Durability, Aesthetic Appeal | Watches, Jewelry |
TiN | Hardness, Corrosion Resistance | Phones, Glasses, Hardware |
ZnSn | Thermal Insulation | Low-e Windows, Glass |
AlCr | Wear Resistance | Tools, Machine Parts |
ITO | Electrical Conductivity, Optical Transparency | LCDs, Touch Panels |
Real Gold | Premium Finish | Luxury Items |
Metallic Alloys, Ceramics | Durable Protection | High-Performance Industries |
Bio-glasses, Polymers | Biocompatibility | Medical, Dental Applications |
Engineered Plastics | Lightweight, Corrosion Resistance | Various Industries |
Ready to enhance your products with PVD coatings? Contact us today for expert guidance!