Rolling is a metalworking process that involves passing metal stock through one or more pairs of rolls to reduce thickness, improve uniformity, or impart a desired mechanical property. The materials used in rolling techniques are primarily metals and alloys, chosen based on their mechanical properties, thermal stability, and suitability for the intended application. Common materials include steel, aluminum, copper, and titanium, as well as specialized alloys like stainless steel and nickel-based superalloys. These materials are selected for their ability to withstand the high pressures and temperatures involved in rolling, as well as their final application requirements, such as strength, ductility, and corrosion resistance.
Key Points Explained:
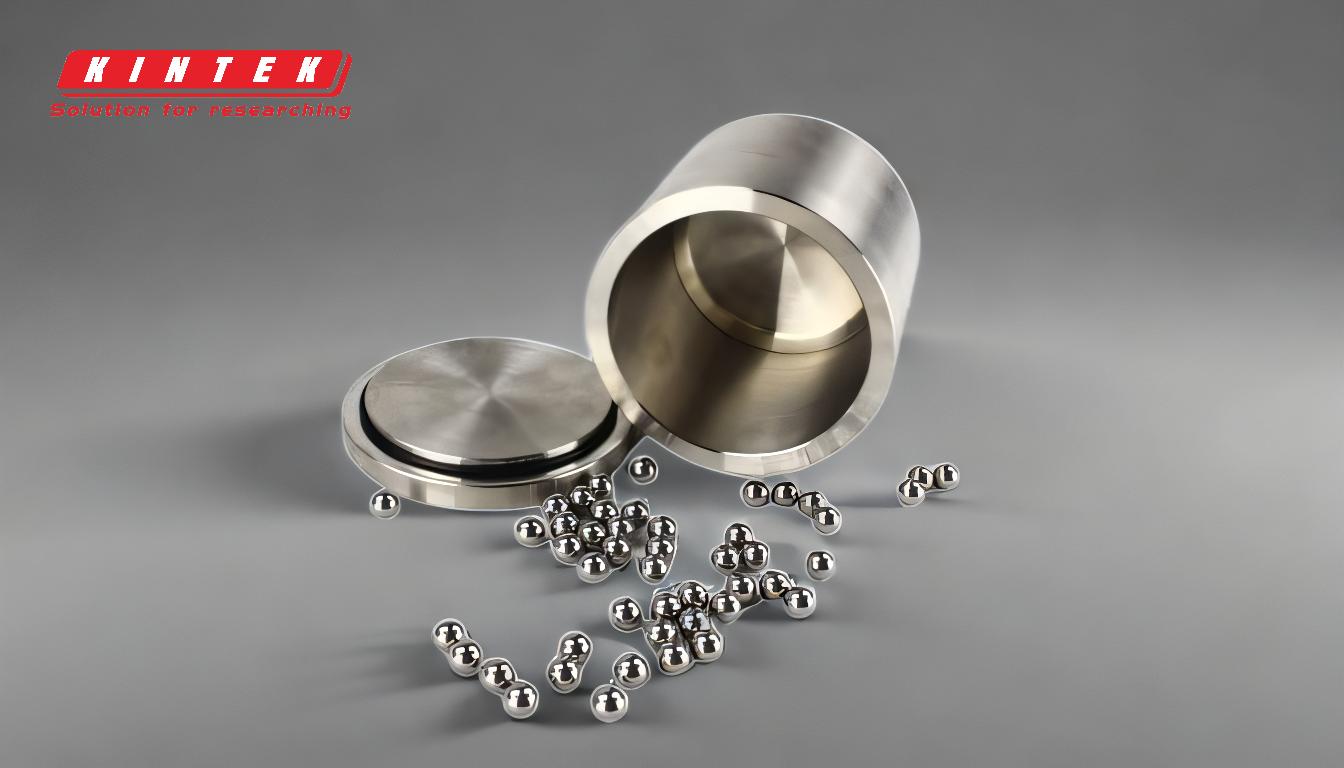
-
Steel:
- Steel is the most widely used material in rolling techniques due to its versatility, strength, and availability. It can be rolled into various forms, such as sheets, plates, and structural shapes.
- Types of steel used include carbon steel, alloy steel, and stainless steel. Carbon steel is commonly used for general-purpose applications, while alloy steel is chosen for enhanced mechanical properties. Stainless steel is preferred for its corrosion resistance.
- Rolling steel requires precise control of temperature and pressure to achieve the desired mechanical properties and surface finish.
-
Aluminum:
- Aluminum is another popular material in rolling, known for its lightweight, corrosion resistance, and excellent thermal and electrical conductivity.
- It is often rolled into thin sheets or foils for applications in the aerospace, automotive, and packaging industries.
- Aluminum rolling involves both hot and cold rolling processes, with cold rolling being used to achieve thinner gauges and improved surface finishes.
-
Copper:
- Copper is widely used in rolling for its excellent electrical conductivity and malleability. It is commonly rolled into sheets, strips, and foils for electrical and electronic applications.
- Copper alloys, such as brass and bronze, are also rolled to enhance specific properties like strength, wear resistance, and corrosion resistance.
- Rolling copper requires careful temperature control to prevent work hardening and ensure uniformity in thickness.
-
Titanium:
- Titanium is valued in rolling for its high strength-to-weight ratio, corrosion resistance, and biocompatibility. It is often used in aerospace, medical, and chemical industries.
- Rolling titanium is challenging due to its high strength and low thermal conductivity, requiring specialized equipment and processes.
- Both hot and cold rolling techniques are used, with hot rolling being more common for achieving larger reductions in thickness.
-
Specialized Alloys:
- Nickel-based superalloys and other high-performance alloys are used in rolling for applications requiring extreme strength, heat resistance, and corrosion resistance, such as in jet engines and gas turbines.
- These materials are difficult to roll due to their high strength and work-hardening characteristics, often requiring advanced rolling techniques and equipment.
-
Material Selection Considerations:
- The choice of material for rolling depends on the intended application, required mechanical properties, and processing conditions.
- Factors such as thermal stability, ductility, and resistance to deformation under high pressure are critical in selecting the appropriate material.
By understanding the properties and applications of these materials, manufacturers can optimize the rolling process to produce high-quality products tailored to specific industry needs.
Summary Table:
Material | Key Properties | Common Applications |
---|---|---|
Steel | Versatile, strong, corrosion-resistant | Sheets, plates, structural shapes |
Aluminum | Lightweight, corrosion-resistant | Aerospace, automotive, packaging |
Copper | Excellent conductivity, malleable | Electrical, electronic applications |
Titanium | High strength-to-weight, biocompatible | Aerospace, medical, chemical industries |
Alloys | Extreme strength, heat resistance | Jet engines, gas turbines |
Need help selecting the right material for your rolling process? Contact our experts today for tailored solutions!