Thin film deposition is a critical process in various industries, including electronics, optics, and energy, where materials are deposited in thin layers onto substrates to create functional coatings. The materials used in thin film deposition are broadly categorized into metals, oxides, and compounds, each offering distinct properties and applications. Metals like copper and aluminum are valued for their conductivity and durability but can be costly. Oxides such as indium tin oxide (ITO) and copper oxide (CuO) are durable and resistant to high temperatures but may be brittle. Compounds like copper indium gallium diselenide (CIGS) combine multiple elements to achieve specific electrical or optical properties, though they can be expensive and challenging to process. The choice of material depends on the desired functionality, cost considerations, and the specific deposition technique employed, such as Physical Vapor Deposition (PVD) or Chemical Vapor Deposition (CVD).
Key Points Explained:
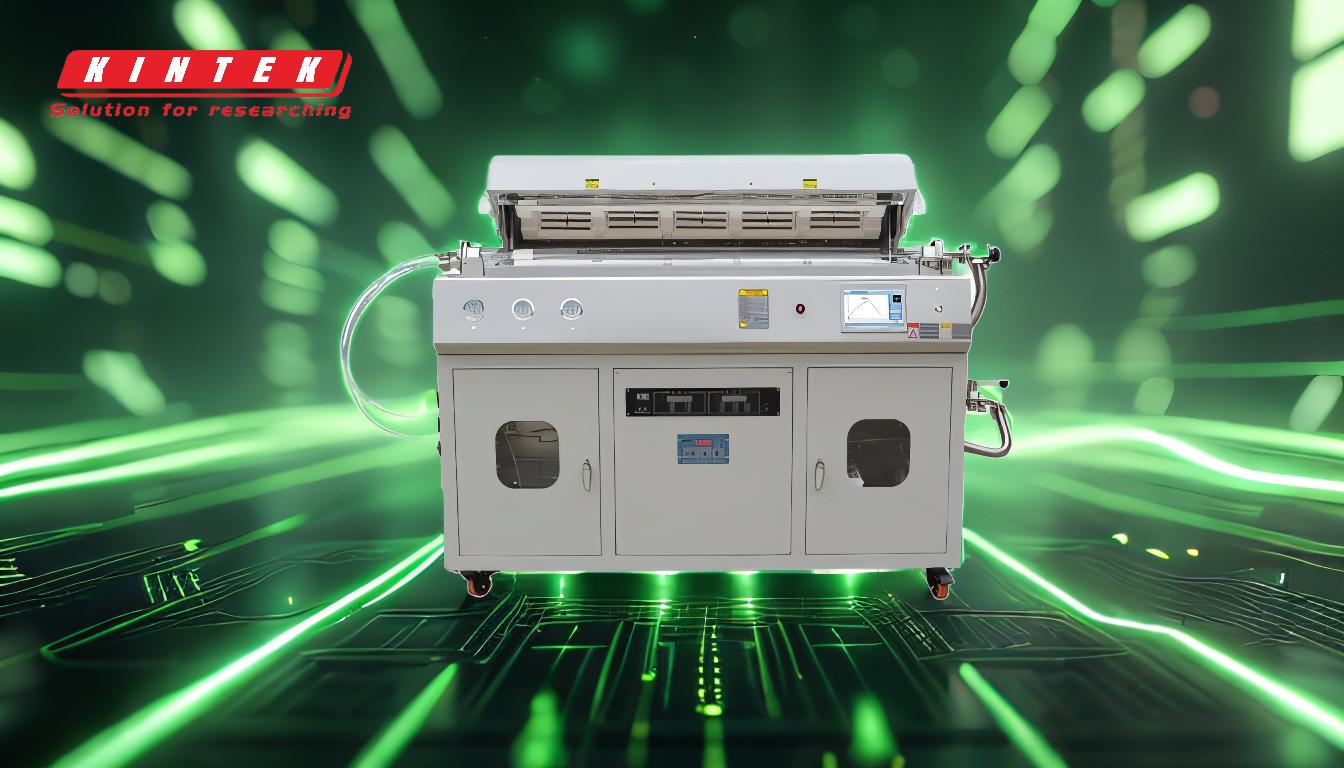
-
Categories of Materials Used in Thin Film Deposition:
- Metals: Metals like copper, aluminum, and gold are commonly used due to their excellent electrical conductivity and mechanical strength. They are ideal for applications requiring high conductivity, such as in microelectronics and solar cells. However, their high cost and susceptibility to oxidation can be limiting factors.
- Oxides: Oxides such as indium tin oxide (ITO) and copper oxide (CuO) are widely used in applications requiring transparency and conductivity, such as in touchscreens and photovoltaic cells. They are durable and can withstand high temperatures, but their brittleness can be a drawback in flexible applications.
- Compounds: Compounds like copper indium gallium diselenide (CIGS) are used in thin-film solar cells due to their high efficiency and tunable bandgap. These materials combine multiple elements to achieve specific properties, but they can be expensive and challenging to synthesize and process.
-
Advantages and Disadvantages of Each Material:
-
Metals:
- Advantages: High conductivity, durability, and mechanical strength.
- Disadvantages: High cost, susceptibility to oxidation, and limited transparency.
-
Oxides:
- Advantages: High durability, transparency, and resistance to high temperatures.
- Disadvantages: Brittleness, limited flexibility, and potential environmental concerns (e.g., indium scarcity).
-
Compounds:
- Advantages: Tunable electrical and optical properties, high efficiency in specific applications.
- Disadvantages: High cost, complex synthesis, and processing challenges.
-
Metals:
-
Common Materials in Thin Film Technology:
- Copper Oxide (CuO): Used in photovoltaic applications due to its semiconducting properties.
- Copper Indium Gallium Diselenide (CIGS): A key material in thin-film solar cells, offering high efficiency and flexibility.
- Indium Tin Oxide (ITO): Widely used in transparent conductive coatings for displays and touchscreens.
-
Deposition Techniques:
- Physical Vapor Deposition (PVD): Techniques like evaporation and sputtering are used to deposit metals and some oxides. PVD is known for producing high-purity films with excellent adhesion.
- Chemical Vapor Deposition (CVD): This method involves chemical reactions to deposit thin films, making it suitable for oxides and compounds. CVD allows for precise control over film composition and thickness.
- Atomic Layer Deposition (ALD): A variant of CVD, ALD deposits films one atomic layer at a time, offering exceptional control and uniformity, ideal for complex compounds.
- Spray Pyrolysis: This technique involves spraying a material solution onto a substrate and thermally degrading it to form a thin film. It is cost-effective and suitable for large-area coatings.
-
Application-Specific Considerations:
- The choice of material and deposition technique depends on the application's requirements, such as conductivity, transparency, flexibility, and cost. For example, ITO is preferred for touchscreens due to its transparency and conductivity, while CIGS is favored in solar cells for its high efficiency.
By understanding the properties, advantages, and limitations of each material and deposition technique, manufacturers can make informed decisions to optimize thin film deposition for specific applications.
Summary Table:
Material Type | Examples | Advantages | Disadvantages |
---|---|---|---|
Metals | Copper, Aluminum, Gold | High conductivity, durability, mechanical strength | High cost, susceptibility to oxidation, limited transparency |
Oxides | ITO, CuO | High durability, transparency, resistance to high temperatures | Brittleness, limited flexibility, environmental concerns (e.g., indium scarcity) |
Compounds | CIGS | Tunable electrical/optical properties, high efficiency in specific applications | High cost, complex synthesis, processing challenges |
Need help selecting the right materials for your thin film deposition? Contact our experts today for tailored solutions!