Plasma Enhanced Chemical Vapor Deposition (PECVD) is a versatile thin-film deposition technique widely used in various industries, including microelectronics, tribology, food packaging, and biomedical applications. PECVD enables the deposition of a range of materials, including dielectric compounds like silicon dioxide and silicon nitride, diamond-like carbon (DLC) for wear resistance, and organic and inorganic polymers for specialized applications. The process leverages plasma to enhance chemical reactions, allowing for lower deposition temperatures and improved film quality compared to traditional CVD methods. PECVD can be further categorized into types such as RF-PECVD, VHF-PECVD, DBD-PECVD, and MWECR-PECVD, each tailored for specific applications and material properties.
Key Points Explained:
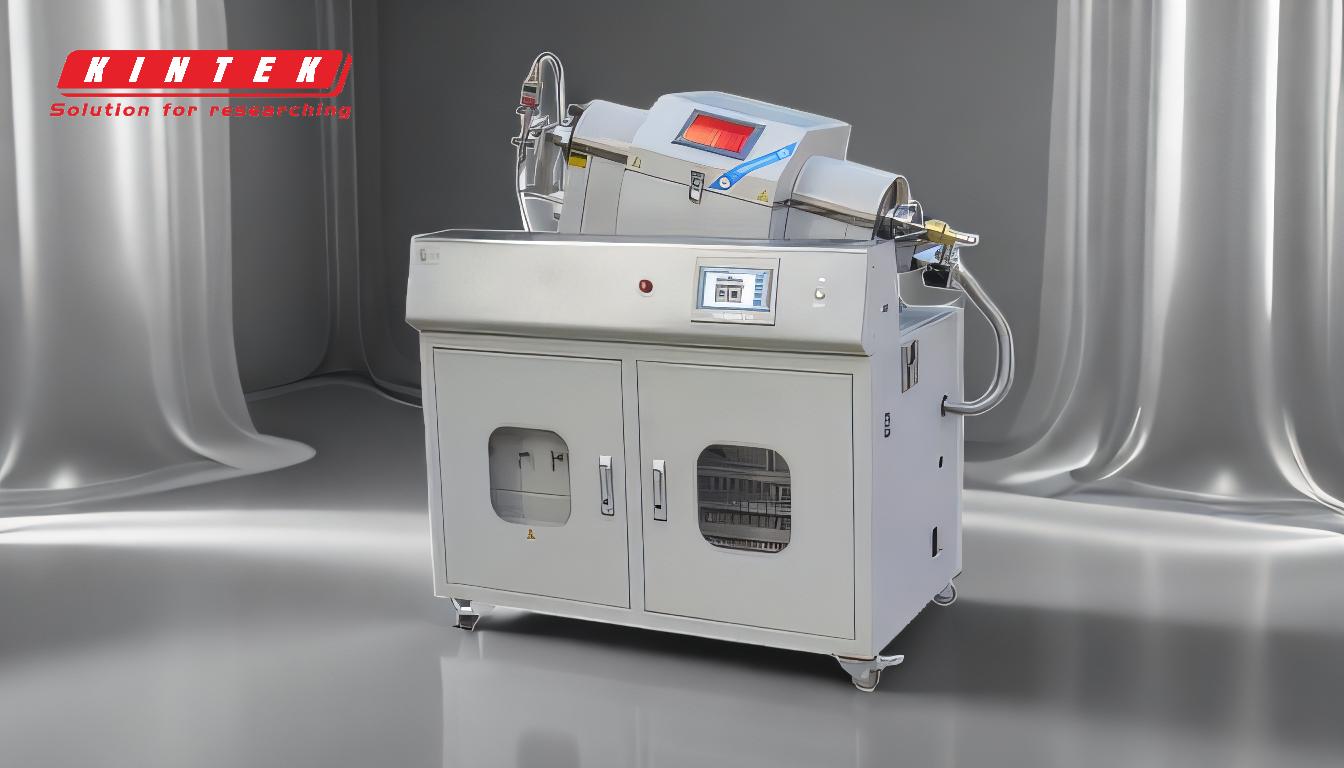
-
Dielectric Materials (Silicon Compounds):
- PECVD is extensively used to deposit dielectric materials such as silicon dioxide (SiO2) and silicon nitride (Si3N4). These materials are critical in microelectronics for creating insulating layers and encapsulating devices. Silicon dioxide provides excellent electrical insulation, while silicon nitride offers superior mechanical strength and chemical resistance. Both materials are deposited at relatively low temperatures, making PECVD suitable for temperature-sensitive substrates.
-
Diamond-Like Carbon (DLC):
- Diamond-like carbon is another material commonly deposited using PECVD. DLC films are known for their exceptional hardness, low friction, and wear resistance, making them ideal for tribological applications such as coatings for cutting tools, automotive components, and medical devices. The unique properties of DLC arise from its amorphous structure, which combines sp2 (graphite-like) and sp3 (diamond-like) carbon bonds.
-
Organic and Inorganic Polymers:
- PECVD is also employed to deposit organic and inorganic polymers. These materials are used in food packaging to create barrier layers that protect contents from moisture and gases. In biomedical applications, polymer films are used for drug delivery systems, biocompatible coatings, and tissue engineering scaffolds. The ability to deposit polymers at low temperatures and with precise control over film properties makes PECVD a preferred method in these fields.
-
PECVD Variants and Their Applications:
- PECVD can be categorized into several types, each with unique characteristics:
- RF-PECVD (Radio Frequency Enhanced PECVD): Uses radio frequency plasma to deposit thin films, commonly used for silicon-based dielectrics and DLC.
- VHF-PECVD (Very High Frequency PECVD): Operates at higher frequencies, enabling faster deposition rates and improved film uniformity, often used in solar cell manufacturing.
- DBD-PECVD (Dielectric Blocking Discharge PECVD): Utilizes dielectric barriers to generate plasma, suitable for large-area coatings and polymer films.
- MWECR-PECVD (Microwave Electron Cyclotron Resonance PECVD): Employs microwave-generated plasma, offering high-density plasma for high-quality thin films, particularly in advanced electronics and optics.
- PECVD can be categorized into several types, each with unique characteristics:
-
Advantages of PECVD:
- PECVD offers several advantages over traditional CVD, including lower deposition temperatures, enhanced film quality, and the ability to deposit a wide range of materials. The use of plasma allows for precise control over film properties such as thickness, composition, and morphology, making it suitable for diverse applications.
-
Comparison with Other Deposition Techniques:
- Unlike Physical Vapor Deposition (PVD), which is limited to metals, alloys, and ceramics, PECVD can deposit a broader range of materials, including dielectric compounds and polymers. Similarly, while Chemical Vapor Deposition (CVD) can process metallic and ceramic compounds, PECVD provides better control over film properties and is more versatile for temperature-sensitive applications.
In summary, PECVD is a highly adaptable deposition technique capable of producing a wide array of materials with tailored properties. Its ability to deposit dielectric compounds, diamond-like carbon, and polymers at low temperatures makes it indispensable in industries ranging from microelectronics to biomedical engineering. The various PECVD variants further enhance its applicability, enabling precise control over film characteristics for specific use cases.
Summary Table:
Material Type | Examples | Key Applications |
---|---|---|
Dielectric Compounds | Silicon dioxide (SiO2), Silicon nitride (Si3N4) | Microelectronics (insulating layers, device encapsulation) |
Diamond-Like Carbon (DLC) | DLC films | Tribology (cutting tools, automotive components, medical devices) |
Organic/Inorganic Polymers | Polymer films | Food packaging (barrier layers), biomedical (drug delivery, biocompatible coatings) |
PECVD Variants | Applications | |
RF-PECVD | Silicon-based dielectrics, DLC | |
VHF-PECVD | Solar cell manufacturing | |
DBD-PECVD | Large-area coatings, polymer films | |
MWECR-PECVD | Advanced electronics, optics |
Learn how PECVD can revolutionize your thin-film applications—contact our experts today!