The best metal for a crucible depends on the specific application, including the type of material being melted, the melting temperature, chemical compatibility, and operational requirements. Common crucible materials include graphite, silicon carbide, clay-graphite, and platinum, each offering unique advantages. Graphite is widely used for its high thermal conductivity and resistance to thermal shock, making it suitable for melting metals like aluminum and copper. Silicon carbide is durable and ideal for high-temperature applications, such as semiconductor production. Platinum is inert and chemically stable, making it perfect for scientific applications and precious metal refining. The choice of crucible material should align with the melting environment, ensuring resistance to corrosion, thermal stability, and compatibility with the melt.
Key Points Explained:
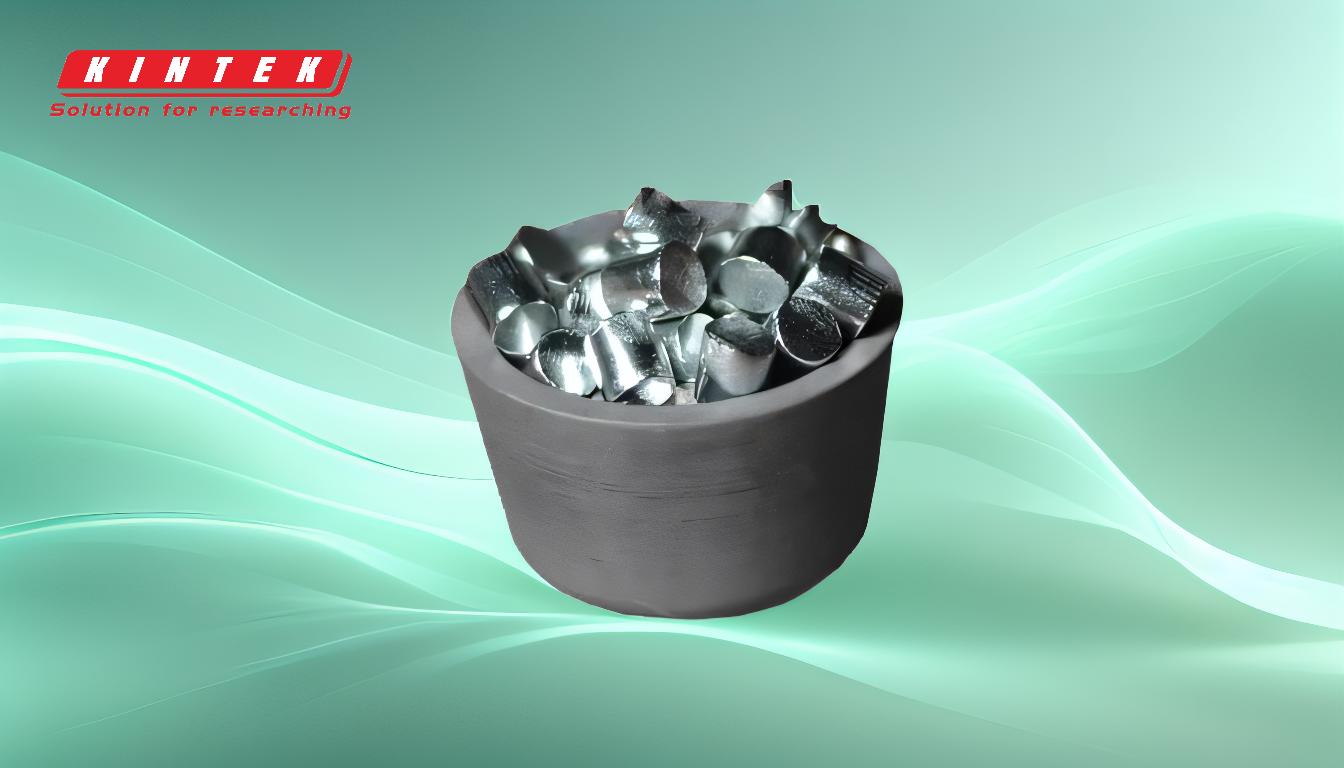
-
Application-Specific Requirements:
- The choice of crucible material depends on the specific application, such as melting, refining, or scientific analysis.
- For example, platinum is ideal for scientific applications due to its inertness, while graphite is preferred for industrial metal melting due to its thermal conductivity.
-
Material Properties:
- Graphite: High thermal conductivity, resistance to thermal shock, and affordability make it a popular choice for melting nonferrous metals like aluminum and copper.
- Silicon Carbide: Extremely durable and resistant to high temperatures, making it suitable for semiconductor production and other high-temperature applications.
- Platinum: Chemically inert and stable, ensuring no contamination in scientific experiments or precious metal refining.
- Clay-Graphite: Combines the thermal properties of graphite with the durability of clay, often used in induction furnaces.
-
Thermal and Chemical Stability:
- A crucible must withstand high temperatures without degrading or reacting with the melt.
- For example, silicon carbide and boron nitride are excellent for high-temperature vacuum furnaces due to their thermal insulation properties.
-
Resistance to Corrosion:
- Crucibles used in corrosive environments, such as aluminum melting with fluxes, require materials with high resistance to chemical attack.
- A dense material structure and protective glaze are essential to prevent corrosion and extend the crucible's lifespan.
-
Electrical Compatibility for Induction Furnaces:
- The crucible's electrical resistivity must match the operating frequency of the induction furnace.
- For lower frequency furnaces, high silicon carbide content is preferred, while higher frequency furnaces may require crucibles with high clay content.
-
Non-Wetting Properties for Precious Metals:
- Crucibles used for refining precious metals must prevent metal penetration, ensuring clean metal output.
- A dense material structure and protective glaze are critical to achieving non-wetting properties.
-
Thermal Shock Resistance:
- Materials like fused quartz are ideal for applications requiring resistance to rapid temperature changes, such as melting metals with fluctuating temperatures.
-
Cost and Availability:
- While platinum offers superior performance, its high cost limits its use to specialized applications like scientific research and precious metal refining.
- Graphite and silicon carbide are more cost-effective and widely available for industrial use.
By carefully considering these factors, the best crucible material can be selected to ensure optimal performance, durability, and cost-effectiveness for the intended application.
Summary Table:
Material | Key Properties | Best Applications |
---|---|---|
Graphite | High thermal conductivity, thermal shock resistance, affordable | Melting nonferrous metals (e.g., aluminum, copper) |
Silicon Carbide | Durable, high-temperature resistance | Semiconductor production, high-temperature uses |
Platinum | Chemically inert, stable, non-reactive | Scientific research, precious metal refining |
Clay-Graphite | Combines thermal conductivity of graphite with clay durability | Induction furnaces |
Need help selecting the perfect crucible material for your needs? Contact our experts today!