Induction melting is a highly efficient and versatile method for melting a wide range of metals, including steel, stainless steel, iron, copper, brass, gold, silver, aluminum, and aluminum alloys. The process is influenced by factors such as temperature, pressure, impurities, slags, and oxidants. Additionally, the energy consumption varies depending on the type of metal being melted, with cast iron, SG iron, MS/SS, and aluminum each having specific power consumption rates. Induction furnaces, particularly those using IGBT technology, are preferred for their precision, energy efficiency, and ability to handle diverse metal types.
Key Points Explained:
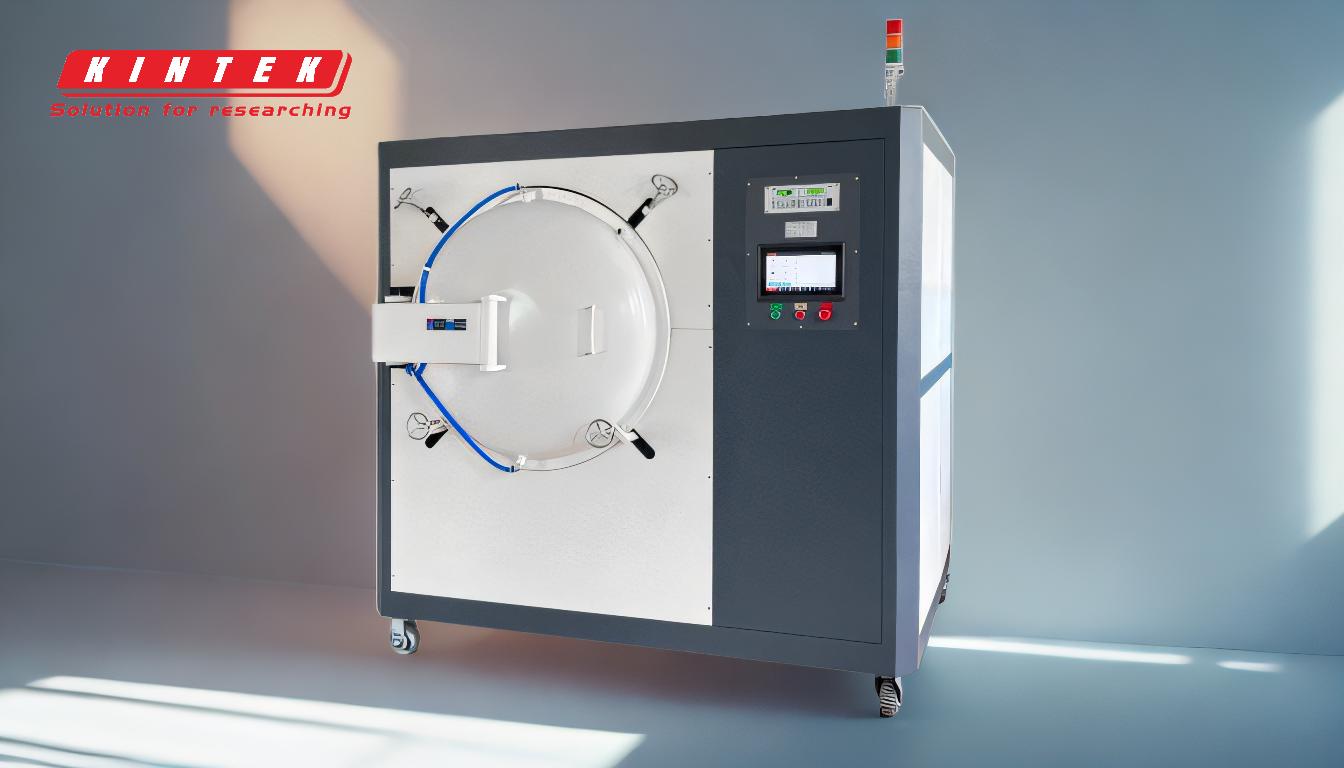
-
Metals Suitable for Induction Melting:
- Steel and Stainless Steel: Induction melting is widely used for steel and stainless steel due to its ability to achieve high temperatures and maintain precise control over the melting process.
- Iron: Both cast iron and SG iron can be efficiently melted using induction furnaces, with specific power consumption rates tailored to each type.
- Copper and Brass: These metals are commonly melted in induction furnaces due to their excellent electrical conductivity, which makes them highly responsive to induction heating.
- Precious Metals: Gold and silver can be melted using induction furnaces, which offer precise temperature control and minimal contamination, crucial for precious metal processing.
- Aluminum and Aluminum Alloys: Induction melting is also suitable for aluminum and its alloys, although the process requires careful control of temperature and atmosphere to prevent oxidation.
-
Factors Influencing the Melting Process:
- Temperature: The melting point of the metal is a critical factor. Induction furnaces can reach the high temperatures required for melting metals like steel and iron.
- Pressure: While most induction melting is done at atmospheric pressure, certain applications may require controlled pressure environments.
- Impurities and Slags: The presence of impurities and slags can affect the quality of the melted metal. Induction furnaces often include mechanisms to remove or control these elements.
- Oxidants: The presence of oxidants can lead to oxidation of the metal, which is particularly problematic for metals like aluminum. Induction furnaces can be operated in inert atmospheres to prevent oxidation.
-
Energy Consumption:
- Cast Iron: The power consumption for melting cast iron typically ranges from 550-600 kWh/ton.
- SG Iron: For SG iron, the power consumption is slightly higher, ranging from 550-650 kWh/ton.
- MS/SS (Mild Steel/Stainless Steel): The energy required for melting MS/SS is between 600-680 kWh/ton.
- Aluminum: Melting aluminum consumes the most energy, with rates ranging from 650-700 kWh/ton.
-
Advantages of IGBT Induction Furnaces:
- Precision and Control: IGBT (Insulated Gate Bipolar Transistor) technology allows for precise control over the heating process, which is crucial for melting a variety of metals with different requirements.
- Energy Efficiency: IGBT induction furnaces are known for their energy efficiency, which is particularly important given the varying power consumption rates of different metals.
- Versatility: The ability to melt a wide range of metals makes IGBT induction furnaces a versatile choice for many industrial applications.
In summary, induction melting, particularly with igbt induction furnace, is a highly effective method for melting a diverse array of metals. The process is influenced by several factors, including temperature, pressure, impurities, and oxidants, and the energy consumption varies depending on the metal type. The precision, efficiency, and versatility of IGBT induction furnaces make them a preferred choice for many metal melting applications.
Summary Table:
Metal | Key Characteristics | Power Consumption (kWh/ton) |
---|---|---|
Steel/Stainless Steel | High-temperature melting, precise control | 600-680 |
Cast Iron | Efficient melting, tailored power consumption | 550-600 |
SG Iron | Slightly higher power consumption than cast iron | 550-650 |
Copper/Brass | Excellent electrical conductivity, responsive to induction heating | N/A |
Gold/Silver | Precise temperature control, minimal contamination | N/A |
Aluminum/Alloys | Requires controlled atmosphere to prevent oxidation | 650-700 |
Ready to optimize your metal melting process? Contact us today to learn more about IGBT induction furnaces!