Thin film deposition is a critical process in various industries, particularly in semiconductor manufacturing, optics, and energy applications. The primary methods used for thin film deposition are Physical Vapor Deposition (PVD) and Chemical Vapor Deposition (CVD). PVD involves heating a material to its boiling point and condensing the vapor onto a surface, making it suitable for materials with high melting points. CVD, on the other hand, involves chemical reactions to deposit materials, often used for materials with low melting points. Both methods have evolved to include advanced techniques like sputtering, thermal evaporation, electron beam evaporation, and atomic layer deposition (ALD), each tailored to specific material properties and application requirements.
Key Points Explained:
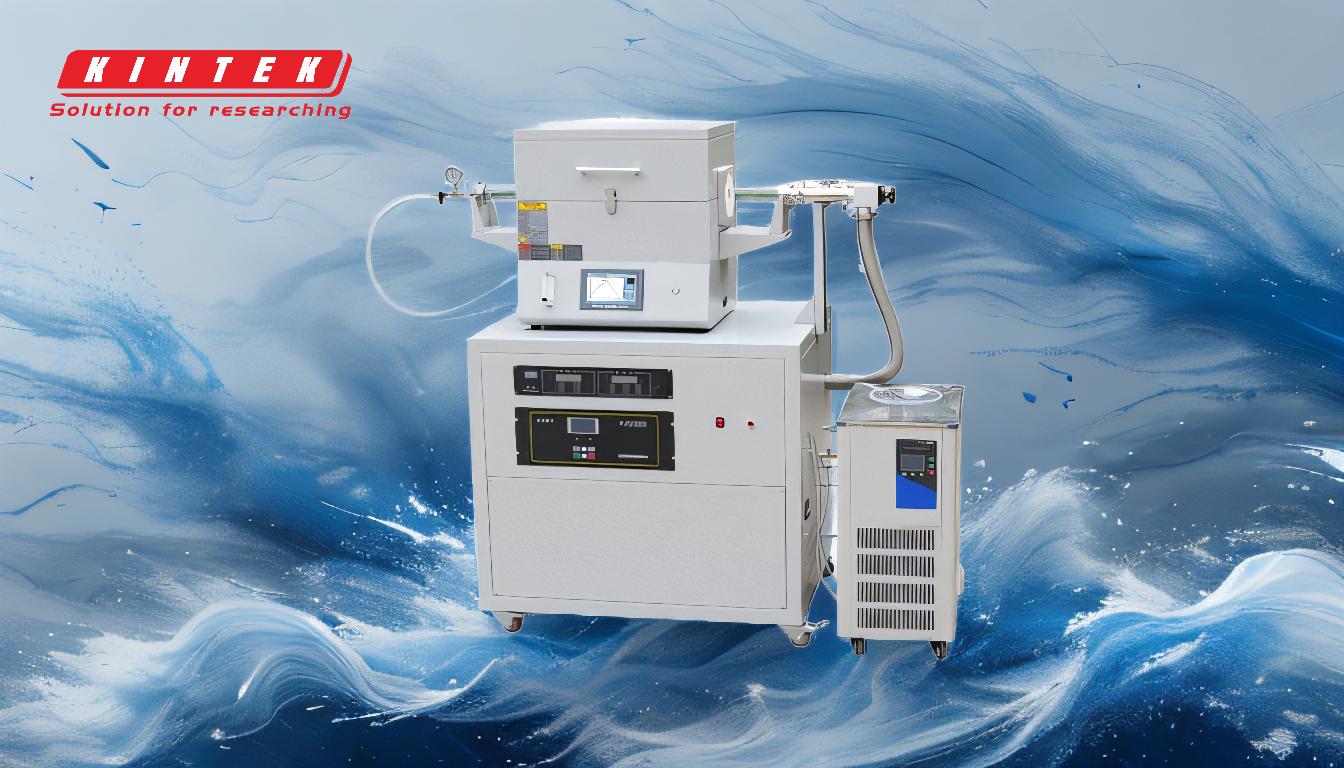
-
Physical Vapor Deposition (PVD):
- PVD is a process where materials are vaporized from a solid source and then deposited onto a substrate.
- Common PVD techniques include:
- Sputtering: A technique where atoms are ejected from a solid target material due to bombardment by energetic ions. This method is widely used for depositing metals, alloys, and compounds.
- Thermal Evaporation: Involves heating a material in a vacuum until it evaporates, then condensing it onto a substrate. This method is suitable for materials with relatively low melting points.
- Electron Beam Evaporation: Similar to thermal evaporation but uses an electron beam to heat the material, allowing for the deposition of materials with very high melting points.
-
Chemical Vapor Deposition (CVD):
- CVD involves the use of chemical reactions to deposit thin films. Precursor gases are introduced into a reaction chamber, where they react to form a solid film on the substrate.
- CVD is particularly useful for depositing materials with low melting points and is widely used in the semiconductor industry for its high precision and ability to produce uniform coatings.
- Variations of CVD include:
- Plasma-Enhanced CVD (PECVD): Uses plasma to enhance the chemical reaction, allowing for lower deposition temperatures.
- Atomic Layer Deposition (ALD): A highly controlled form of CVD where films are deposited one atomic layer at a time, providing exceptional uniformity and conformality.
-
Applications of Thin Film Deposition:
- Semiconductors: CVD is the most commonly used method in the semiconductor industry due to its ability to produce high-purity, uniform films.
- Optics: Thin films are used to create anti-reflective coatings, mirrors, and filters.
- Energy: Flexible solar cells and organic light-emitting diodes (OLEDs) rely on thin film deposition techniques to create fine layers of polymer compounds.
-
Choosing the Right Deposition Method:
- The choice of deposition method depends on the material properties and the desired film characteristics.
- PVD is generally preferred for materials with high melting points and for applications requiring high-purity coatings.
- CVD is favored for materials with low melting points and for applications requiring precise control over film composition and thickness.
-
Advanced Techniques:
- Ion Beam Deposition: Uses an ion beam to sputter material onto a substrate, offering precise control over the deposition process.
- Magnetron Sputtering: A form of sputtering that uses magnetic fields to enhance the efficiency of the deposition process, commonly used for depositing metals and alloys.
- Electron Beam Evaporation: Ideal for depositing materials with very high melting points, such as refractory metals and ceramics.
In summary, thin film deposition is a versatile and essential process with a wide range of applications. The choice between PVD and CVD, and their respective techniques, depends on the specific requirements of the material and the application. Advances in deposition technology continue to expand the possibilities for creating high-performance thin films in various industries.
Summary Table:
Method | Description | Techniques | Applications |
---|---|---|---|
Physical Vapor Deposition (PVD) | Vaporizes materials from a solid source and deposits them onto a substrate. | Sputtering, Thermal Evaporation, Electron Beam Evaporation | High-purity coatings, metals, alloys, and high-melting-point materials. |
Chemical Vapor Deposition (CVD) | Uses chemical reactions to deposit thin films from precursor gases. | Plasma-Enhanced CVD (PECVD), Atomic Layer Deposition (ALD) | Semiconductors, low-melting-point materials, uniform and precise coatings. |
Advanced Techniques | Enhanced methods for specific material properties and applications. | Ion Beam Deposition, Magnetron Sputtering, Electron Beam Evaporation | Refractory metals, ceramics, and high-performance thin films. |
Discover the best thin film deposition method for your needs—contact our experts today!