Laser sintering is a versatile additive manufacturing process used to create a wide range of products across multiple industries. It involves using a laser to fuse powdered materials, such as metals, polymers, or ceramics, into solid structures layer by layer. This technology is particularly valued for its ability to produce complex, high-precision components with excellent mechanical properties. Products made using laser sintering include aerospace components, medical implants, dental products, electrical and optical components, automotive parts, and custom tools. The process is also widely used in prototyping and research due to its flexibility and efficiency. Below, we explore the key applications and products in detail.
Key Points Explained:
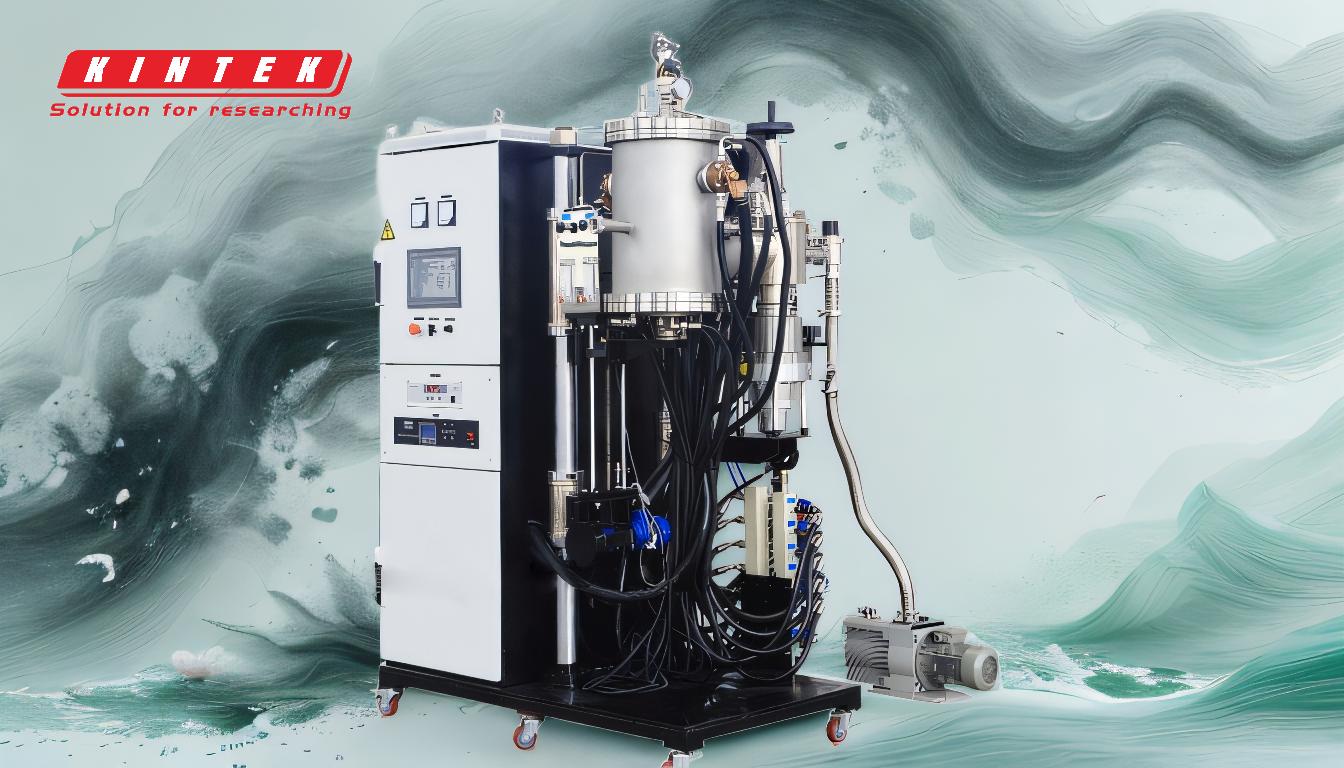
-
Aerospace Industry Applications
- Laser sintering is used to manufacture lightweight, high-strength components for aircraft and spacecraft.
- Examples include turbine blades, fuel nozzles, and structural brackets.
- The process allows for the creation of complex geometries that are difficult or impossible to achieve with traditional manufacturing methods.
- Benefits include reduced weight, improved fuel efficiency, and enhanced performance.
-
Healthcare and Medical Products
- Laser sintering is widely used in the production of medical implants, such as hip and knee replacements, dental crowns, and orthodontic devices.
- The process enables the creation of custom-fit implants tailored to individual patient anatomy.
- Other medical applications include surgical tools, prosthetics, and porous structures for bone ingrowth.
- The biocompatibility of materials like titanium and cobalt-chrome makes them ideal for medical use.
-
Dental Industry Applications
- Dental products made using laser sintering include crowns, bridges, dentures, and orthodontic appliances.
- The process allows for precise customization, ensuring a perfect fit for patients.
- Materials like zirconia and cobalt-chrome are commonly used due to their durability and aesthetic properties.
- Benefits include faster production times and reduced costs compared to traditional methods.
-
Electrical and Optical Components
- Laser sintering is used to produce electrical contacts, semiconductors, and optical fibers.
- The process enhances the conductivity and performance of these components.
- Applications include sensors, connectors, and circuit boards.
- The ability to create intricate designs with high precision is a key advantage.
-
Automotive Industry Applications
- Laser sintering is used to manufacture lightweight, durable parts for vehicles, such as engine components, gears, and brackets.
- The process supports the production of complex geometries and custom designs.
- Benefits include reduced weight, improved fuel efficiency, and enhanced performance.
- It is also used for prototyping and testing new designs.
-
Industrial and Engineering Applications
- Laser sintering is used to create structural steel parts, cutting tools, and self-lubricating bearings.
- The process enhances the strength, durability, and performance of these components.
- Applications include machinery, equipment, and industrial tools.
- The ability to produce custom parts on demand is a significant advantage.
-
Prototyping and Research
- Laser sintering is widely used in prototyping due to its ability to quickly produce high-quality, functional prototypes.
- It is also used in research laboratories to develop new materials and test innovative designs.
- The process supports rapid iteration and experimentation, reducing time-to-market for new products.
- Applications include consumer products, electronics, and industrial equipment.
-
Battery Manufacturing
- Laser sintering is used to produce components for batteries, such as electrodes and separators.
- The process enhances the performance and efficiency of batteries.
- Applications include electric vehicles, portable electronics, and renewable energy storage systems.
- The ability to create precise, high-performance components is a key advantage.
-
Porous Metals and Filters
- Laser sintering is used to manufacture porous metals for filtering applications.
- These materials are used in industries such as chemical processing, water treatment, and aerospace.
- The process allows for the creation of complex, high-surface-area structures.
- Benefits include improved filtration efficiency and durability.
-
Custom and On-Demand Manufacturing
- Laser sintering enables the production of custom parts and tools on demand.
- This is particularly useful for industries that require unique or low-volume components.
- Applications include aerospace, healthcare, and automotive industries.
- The process supports just-in-time manufacturing, reducing inventory costs and lead times.
In conclusion, laser sintering is a highly versatile and valuable technology with applications across a wide range of industries. Its ability to produce complex, high-precision components with excellent mechanical properties makes it an essential tool for modern manufacturing. Whether in aerospace, healthcare, automotive, or research, laser sintering continues to drive innovation and efficiency.
Summary Table:
Industry | Applications | Benefits |
---|---|---|
Aerospace | Turbine blades, fuel nozzles, structural brackets | Lightweight, high-strength, complex geometries |
Healthcare | Medical implants, surgical tools, prosthetics | Custom-fit, biocompatible materials, faster production |
Dental | Crowns, bridges, dentures, orthodontic appliances | Precise customization, durable materials, cost-effective |
Electrical & Optical | Electrical contacts, semiconductors, optical fibers | Enhanced conductivity, high-precision designs |
Automotive | Engine components, gears, brackets | Lightweight, durable, improved fuel efficiency |
Industrial | Structural steel parts, cutting tools, bearings | Enhanced strength, durability, custom on-demand production |
Prototyping & Research | Functional prototypes, new material development | Rapid iteration, reduced time-to-market |
Battery Manufacturing | Electrodes, separators | High-performance, efficient battery components |
Porous Metals & Filters | Filtration materials for chemical processing, water treatment, aerospace | High-surface-area structures, improved filtration efficiency |
Custom Manufacturing | Unique or low-volume components for aerospace, healthcare, automotive | Just-in-time production, reduced inventory costs |
Ready to explore how laser sintering can transform your manufacturing process? Contact us today to learn more!