Aluminum brazing rods are widely used in joining aluminum components due to their ability to create strong, leak-proof joints. The melting temperature of aluminum brazing rods is a critical factor in determining their suitability for specific applications. Typically, these rods melt at temperatures ranging from 570°C to 620°C (1058°F to 1148°F), depending on the alloy composition. This temperature range is lower than the melting point of pure aluminum (660°C or 1220°F), ensuring that the base metal remains intact during the brazing process. The choice of brazing rod depends on the specific application, base metal, and desired joint properties. Understanding the melting temperature and alloy composition is essential for achieving optimal results in brazing operations.
Key Points Explained:
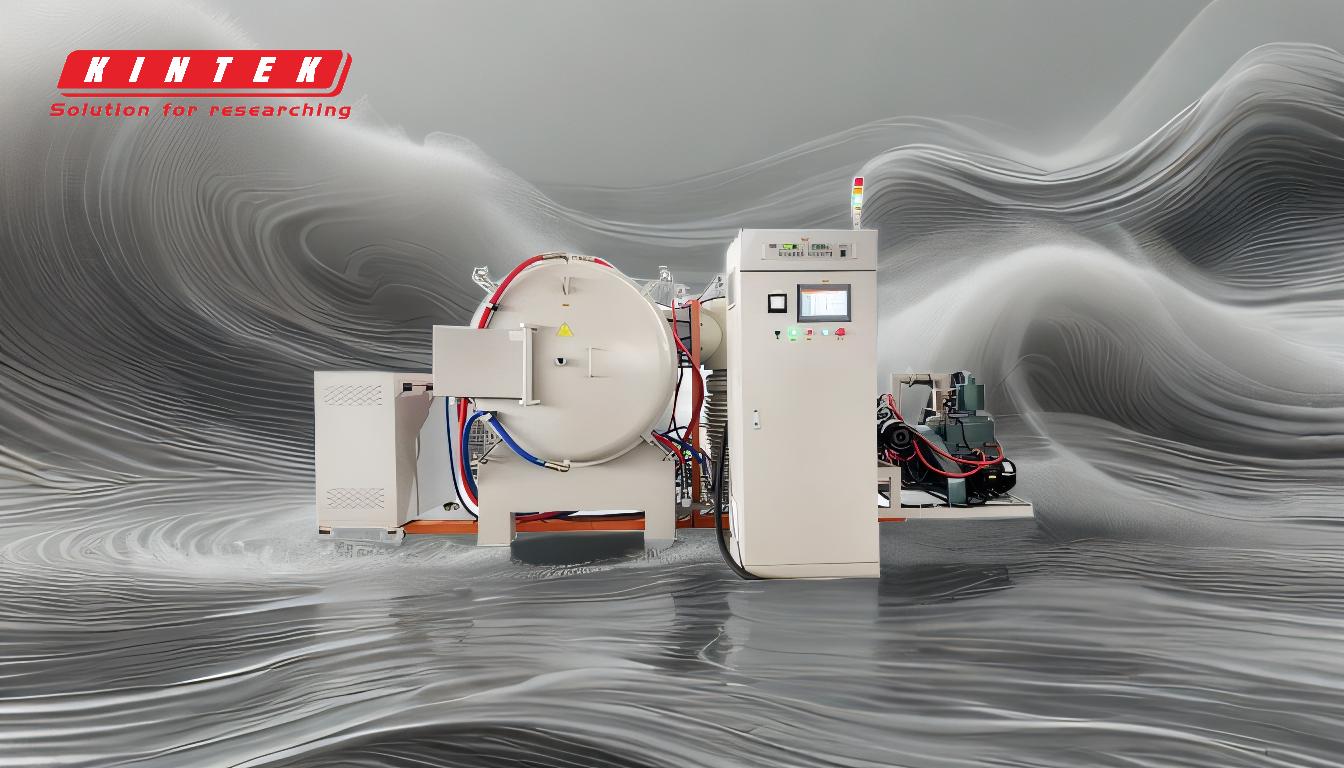
-
Melting Temperature Range of Aluminum Brazing Rods
- Aluminum brazing rods are designed to melt at temperatures between 570°C and 620°C (1058°F to 1148°F).
- This range is lower than the melting point of pure aluminum (660°C or 1220°F), ensuring that the base metal does not melt during the brazing process.
- The specific melting point depends on the alloy composition of the brazing rod, which may include elements like silicon, zinc, or copper to modify its properties.
-
Importance of Alloy Composition
- The alloy composition of the brazing rod significantly influences its melting temperature and performance.
- Common alloys used in aluminum brazing rods include:
- Al-Si (Aluminum-Silicon): These alloys typically melt at around 577°C (1070°F) and are widely used due to their excellent flow and wetting properties.
- Al-Zn (Aluminum-Zinc): These alloys have slightly higher melting temperatures and are often used for their corrosion resistance.
- Al-Cu (Aluminum-Copper): These alloys are less common but provide higher strength joints.
- The choice of alloy depends on the specific application and the properties required in the final joint.
-
Factors Affecting Brazing Temperature
- Base Metal Thickness: Thicker base metals may require higher brazing temperatures to ensure proper heat distribution.
- Joint Design: Complex joint designs may necessitate precise temperature control to achieve uniform melting and flow of the brazing material.
- Heating Method: The method of heating (e.g., torch, furnace, or induction heating) can influence the effective brazing temperature.
- Flux Usage: Fluxes are often used to lower the surface tension of the molten brazing material, facilitating better flow and adhesion. The type of flux used can also affect the required brazing temperature.
-
Applications of Aluminum Brazing Rods
- Aluminum brazing rods are used in a variety of industries, including:
- Automotive: For joining heat exchangers, radiators, and air conditioning components.
- Aerospace: For lightweight and high-strength joints in aircraft structures.
- HVAC: For assembling refrigeration and air conditioning systems.
- Electronics: For creating thermal management solutions in electronic devices.
- The melting temperature of the brazing rod must align with the thermal properties of the components being joined.
- Aluminum brazing rods are used in a variety of industries, including:
-
Best Practices for Aluminum Brazing
- Pre-Cleaning: Ensure that the base metal surfaces are clean and free of oxides or contaminants to achieve strong joints.
- Temperature Control: Use precise temperature control to avoid overheating, which can weaken the base metal or cause the brazing material to flow improperly.
- Flux Application: Apply flux evenly to promote proper wetting and flow of the brazing material.
- Cooling: Allow the joint to cool slowly to minimize thermal stress and ensure a strong bond.
By understanding the melting temperature and alloy composition of aluminum brazing rods, you can select the appropriate material and technique for your specific application, ensuring durable and reliable joints.
Summary Table:
Key Aspect | Details |
---|---|
Melting Temperature | 570°C to 620°C (1058°F to 1148°F) |
Alloy Composition | Al-Si (577°C), Al-Zn (higher melting point), Al-Cu (higher strength) |
Factors Affecting Temp | Base metal thickness, joint design, heating method, flux usage |
Applications | Automotive, aerospace, HVAC, electronics |
Best Practices | Pre-cleaning, temperature control, flux application, slow cooling |
Need help selecting the right aluminum brazing rod for your project? Contact our experts today!