Steel typically liquefies (melts) at temperatures around 1,370 degrees Celsius (2,498 degrees Fahrenheit). This melting point can vary slightly depending on the specific composition of the steel, as different alloying elements can influence the temperature at which it transitions from solid to liquid. Achieving this temperature requires specialized equipment, such as high-quality induction melting furnaces, which are capable of generating and maintaining the extreme heat necessary for melting steel. Understanding the precise melting point is crucial for industries that work with steel, as it ensures proper processing and quality control during manufacturing.
Key Points Explained:
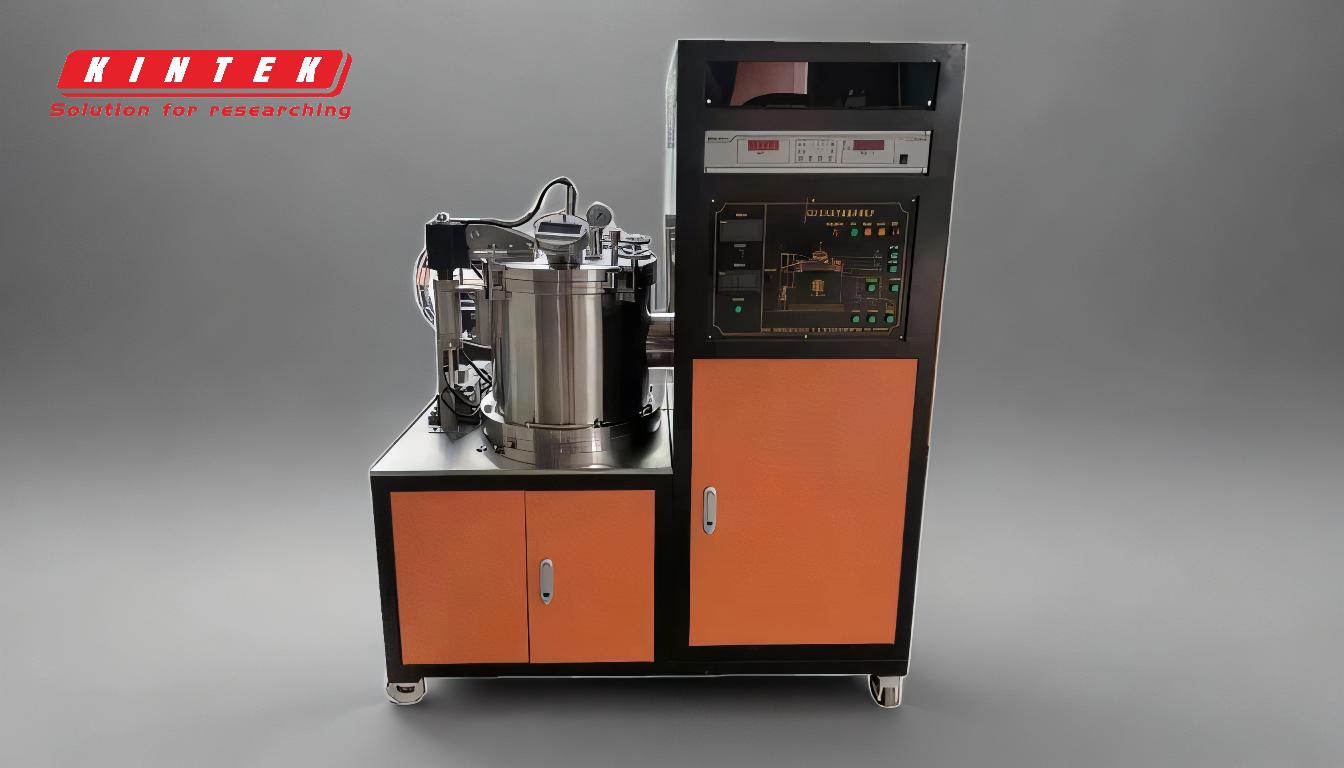
-
Melting Point of Steel:
- Steel generally melts at approximately 1,370 degrees Celsius (2,498 degrees Fahrenheit). This temperature is a benchmark for most steel compositions, but it can vary slightly depending on the specific alloy.
- The melting point is the temperature at which steel transitions from a solid to a liquid state, a critical factor in processes like casting, forging, and welding.
-
Factors Influencing the Melting Point:
-
Alloy Composition: Steel is an alloy primarily composed of iron and carbon, but it often includes other elements like manganese, nickel, chromium, and vanadium. These alloying elements can raise or lower the melting point slightly.
- For example, stainless steel, which contains chromium and nickel, may have a slightly different melting range compared to carbon steel.
- Carbon Content: Higher carbon content generally lowers the melting point of steel. For instance, high-carbon steels melt at slightly lower temperatures than low-carbon steels.
-
Alloy Composition: Steel is an alloy primarily composed of iron and carbon, but it often includes other elements like manganese, nickel, chromium, and vanadium. These alloying elements can raise or lower the melting point slightly.
-
Equipment Required for Melting Steel:
- To achieve the high temperatures needed to melt steel, specialized equipment is required. One of the most common tools is the induction melting furnace.
- Induction Furnaces: These furnaces use electromagnetic induction to generate heat, allowing for precise temperature control and efficient melting. They are capable of reaching temperatures well above 1,370 degrees Celsius, making them ideal for steel melting.
- Other methods include arc furnaces and blast furnaces, which are also used in industrial settings for melting steel.
- To achieve the high temperatures needed to melt steel, specialized equipment is required. One of the most common tools is the induction melting furnace.
-
Importance of Knowing the Melting Point:
- Understanding the melting point of steel is essential for industries involved in manufacturing, construction, and metalworking.
- Quality Control: Ensuring the correct melting temperature helps maintain the structural integrity and desired properties of the steel.
- Process Optimization: Knowing the precise temperature allows for efficient energy use and prevents overheating or underheating, which can lead to defects in the final product.
- Understanding the melting point of steel is essential for industries involved in manufacturing, construction, and metalworking.
-
Practical Applications:
- Casting: In foundries, steel is melted and poured into molds to create complex shapes and components.
- Welding: During welding, localized melting of steel is required to join pieces together.
- Forging: Steel is heated to near its melting point to make it malleable for shaping.
-
Safety Considerations:
- Working with molten steel requires strict safety protocols due to the extreme temperatures involved.
- Protective gear, such as heat-resistant clothing, gloves, and face shields, is essential.
- Proper ventilation and fire safety measures must be in place to handle the intense heat and potential hazards.
- Working with molten steel requires strict safety protocols due to the extreme temperatures involved.
By understanding the melting point of steel and the factors that influence it, industries can ensure efficient and safe processing of this versatile material.
Summary Table:
Aspect | Details |
---|---|
Melting Point | ~1,370°C (2,498°F) |
Influencing Factors | Alloy composition, carbon content |
Equipment | Induction furnaces, arc furnaces, blast furnaces |
Applications | Casting, welding, forging |
Safety Measures | Heat-resistant gear, proper ventilation, fire safety protocols |
Need expert advice on steel processing? Contact us today for tailored solutions!