Tungsten carbide is sintered at high temperatures to achieve its dense and homogeneous structure, which is essential for its exceptional hardness, wear resistance, and strength. The sintering process involves heating a mixture of tungsten and carbon powders in a controlled environment, typically reaching temperatures between 1,400°C and 1,600°C. This process includes several stages, such as the removal of molding agents, solid-phase sintering, liquid-phase sintering, and cooling. The liquid-phase sintering stage, in particular, is critical for achieving the desired density and mechanical properties. The use of cobalt as a binding agent further enhances the material's toughness and durability.
Key Points Explained:
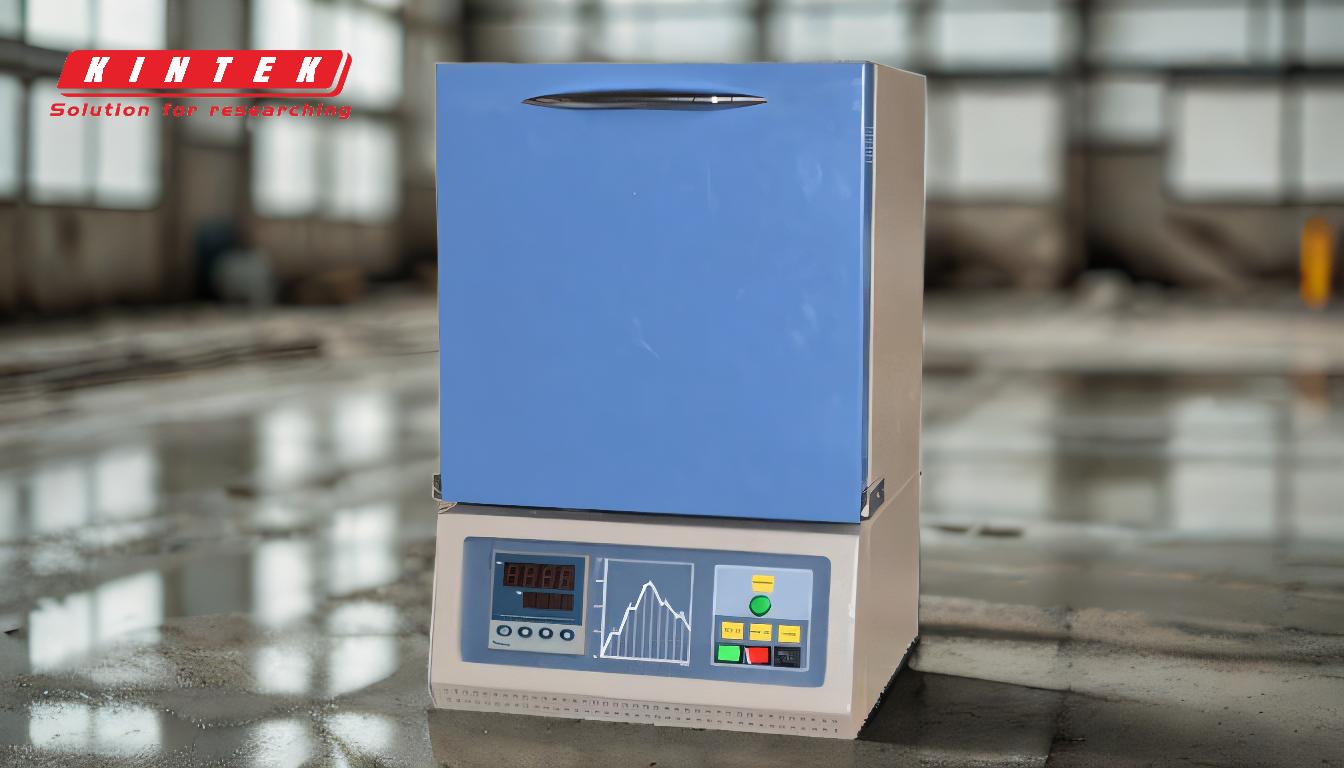
-
Sintering Temperature Range:
- Tungsten carbide is sintered at temperatures ranging from 1,400°C to 1,600°C. This high temperature is necessary to fuse the tungsten and carbon particles into a solid mass, creating a dense and homogeneous structure. The exact temperature depends on the specific composition of the material and the desired properties.
-
Stages of the Sintering Process:
- Removal of Molding Agent and Pre-Burning: This stage involves heating the green material (unsintered tungsten carbide) to remove any molding agents or binders used during the pressing stage. This step ensures that the material is clean and ready for sintering.
- Solid-Phase Sintering: During this stage, the tungsten carbide particles begin to bond at a microscopic level without melting. This process enhances the material's strength and density.
- Liquid-Phase Sintering: At this stage, the temperature is high enough to partially melt the cobalt binder, which flows and fills the gaps between the tungsten carbide particles. This results in a dense, homogeneous structure with excellent mechanical properties.
- Cooling Stage: After sintering, the material is slowly cooled to room temperature to prevent cracking and ensure uniform properties throughout the material.
-
Role of Cobalt as a Binder:
- Cobalt is commonly used as a binder in tungsten carbide sintering. It melts during the liquid-phase sintering stage, filling the voids between the tungsten carbide particles and enhancing the material's toughness and durability. The amount of cobalt used can vary depending on the desired properties of the final product.
-
Importance of Controlled Environment:
- The sintering process must be carried out in a controlled environment, typically in a vacuum or inert gas atmosphere, to prevent oxidation and contamination. This ensures the material's high quality and consistent properties.
-
Applications of Sintered Tungsten Carbide:
- Due to its high hardness, wear resistance, and strength, sintered tungsten carbide is widely used in cutting tools, drilling equipment, wear-resistant parts, and other industrial applications. Its excellent heat and corrosion resistance make it suitable for use in harsh environments.
-
Comparison with Other Materials:
- Tungsten carbide's hardness is comparable to corundum, and it can only be polished and finished using abrasives of superior hardness, such as cubic boron nitride and diamond powder. This makes it a preferred material for applications requiring extreme durability and precision.
-
Powder Metallurgy Process:
- Most tungsten carbide products are manufactured through powder metallurgy, which involves raw material preparation, milling, pressing, and sintering. This method allows for precise control over the material's composition and properties, ensuring consistent quality.
In summary, the sintering of tungsten carbide is a critical process that involves heating the material to high temperatures (1,400°C to 1,600°C) to achieve its exceptional properties. The use of cobalt as a binder and the controlled environment during sintering are essential for producing high-quality tungsten carbide products. For more information on related topics, you can explore tungsten coil.
Summary Table:
Aspect | Details |
---|---|
Sintering Temperature | 1,400°C to 1,600°C |
Stages of Sintering | Removal of molding agents, solid-phase sintering, liquid-phase sintering, cooling |
Role of Cobalt Binder | Enhances toughness and durability by filling voids during liquid-phase sintering |
Controlled Environment | Vacuum or inert gas atmosphere to prevent oxidation and contamination |
Applications | Cutting tools, drilling equipment, wear-resistant parts, industrial uses |
Comparison with Other Materials | Comparable to corundum; requires abrasives like diamond for finishing |
Need high-quality tungsten carbide products? Contact our experts today for tailored solutions!