Annealing is a heat treatment process used to alter the physical and mechanical properties of metals, primarily to increase ductility, reduce hardness, and eliminate internal stresses. The process involves heating the metal to a specific temperature, holding it at that temperature for a certain period, and then allowing it to cool slowly. The exact temperature used for annealing depends on the type of metal and its intended application. Generally, the temperature is set just below the metal's melting point, where the crystalline structure becomes fluid but the metal remains solid. This allows defects in the material to repair themselves, resulting in a more ductile and workable metal.
Key Points Explained:
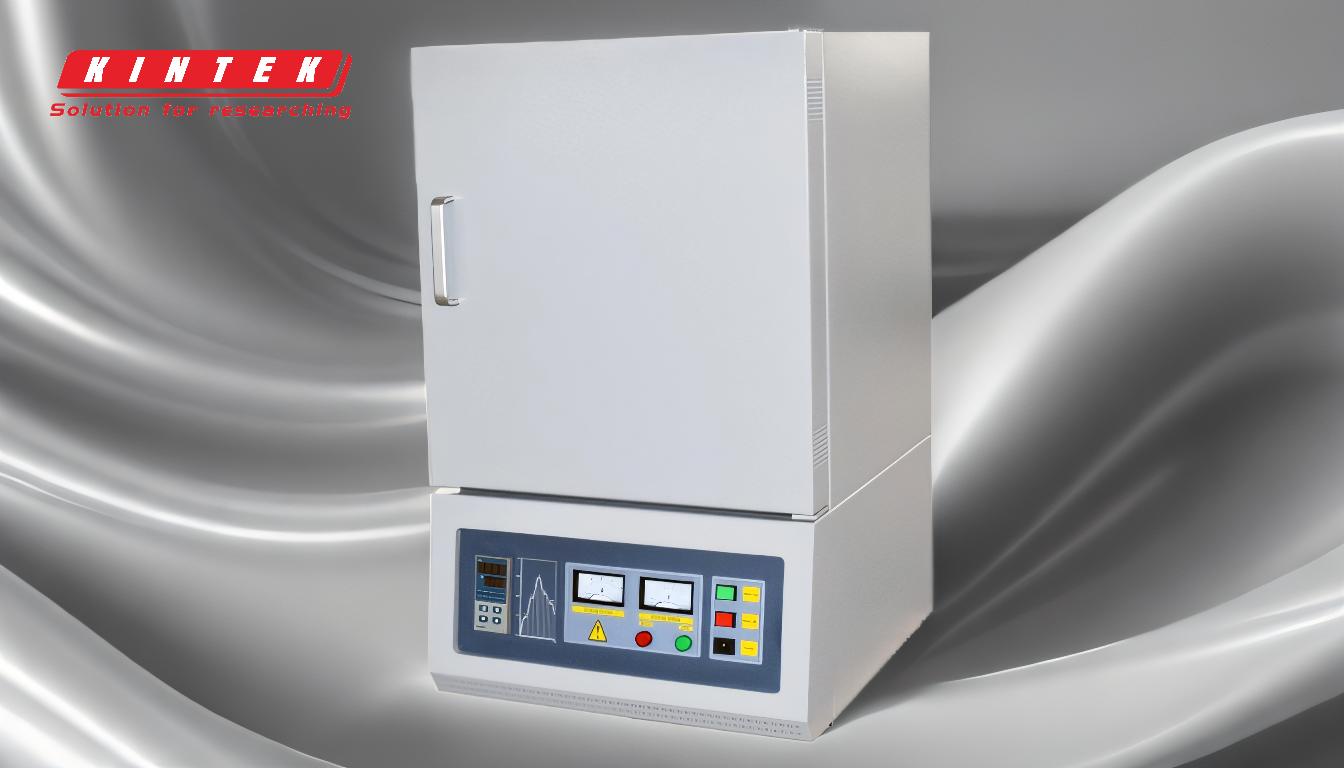
-
Purpose of Annealing:
- Annealing is primarily used to soften metals, making them more ductile and easier to work with.
- It helps in eliminating internal stresses that may have developed during previous manufacturing processes like casting, rolling, or welding.
- The process also improves the metal's machinability and prepares it for further processing or use.
-
Temperature Range for Annealing:
- The annealing temperature varies depending on the type of metal. For example:
- Steel: Typically annealed at temperatures between 700°C and 900°C (1292°F to 1652°F), depending on the carbon content and alloying elements.
- Copper: Annealed at around 400°C to 700°C (752°F to 1292°F).
- Aluminum: Annealed at temperatures between 300°C and 400°C (572°F to 752°F).
- The temperature is chosen to be just below the metal's melting point, where the crystalline structure becomes fluid but the metal remains in a solid state.
- The annealing temperature varies depending on the type of metal. For example:
-
Holding Time at Temperature:
- Once the metal reaches the desired annealing temperature, it is held at that temperature for a specific period. This holding time allows the crystalline structure to reorganize and defects to repair themselves.
- The duration of the holding time depends on the thickness and type of the metal. Thicker materials generally require longer holding times to ensure uniform heating and structural changes throughout the material.
-
Controlled Cooling:
- After the holding period, the metal is cooled slowly to room temperature. The cooling rate is crucial because rapid cooling can reintroduce stresses or cause the metal to harden again.
- Slow cooling allows the metal to achieve a more stable and ductile crystalline structure, which is the primary goal of annealing.
-
Applications of Annealing:
- Manufacturing: Annealing is widely used in the manufacturing of steel, copper, and aluminum products to improve their workability and reduce brittleness.
- Jewelry Making: Metals used in jewelry, such as gold and silver, are often annealed to make them easier to shape and form.
- Electronics: Annealing is used in the production of semiconductors and other electronic components to improve their electrical properties.
-
Importance of Temperature Control:
- Precise temperature control is essential during the annealing process. If the temperature is too low, the desired structural changes may not occur. If it is too high, the metal may melt or undergo unwanted phase transformations.
- Advanced annealing furnaces are equipped with temperature sensors and controllers to maintain the exact temperature required for the specific metal being treated.
-
Effect on Material Properties:
- Ductility: Annealing increases the ductility of the metal, making it easier to bend, stretch, or form without breaking.
- Hardness: The process reduces the hardness of the metal, which can be beneficial for further machining or shaping.
- Internal Stress Relief: Annealing helps in relieving internal stresses that may have been introduced during previous manufacturing processes, reducing the risk of cracking or warping.
In summary, the temperature used for annealing is a critical factor that depends on the type of metal and its intended application. The process involves heating the metal to a specific temperature, holding it at that temperature, and then cooling it slowly to achieve the desired material properties. Proper annealing enhances the metal's ductility, reduces hardness, and eliminates internal stresses, making it more suitable for further processing or use.
Summary Table:
Metal Type | Annealing Temperature Range |
---|---|
Steel | 700°C - 900°C (1292°F - 1652°F) |
Copper | 400°C - 700°C (752°F - 1292°F) |
Aluminum | 300°C - 400°C (572°F - 752°F) |
Need expert advice on annealing processes? Contact us today to optimize your metal treatment!