Melting is a physical process where a solid substance transitions into a liquid state due to the application of heat, pressure, or a combination of both. This transformation occurs when the internal energy of the solid increases, causing the particles to vibrate more vigorously and eventually break free from their fixed positions. The three primary factors that cause melting are temperature, pressure, and the presence of impurities. Temperature is the most common factor, as it directly affects the kinetic energy of particles. Pressure can either promote or inhibit melting depending on the substance, while impurities can lower the melting point by disrupting the orderly structure of the solid.
Key Points Explained:
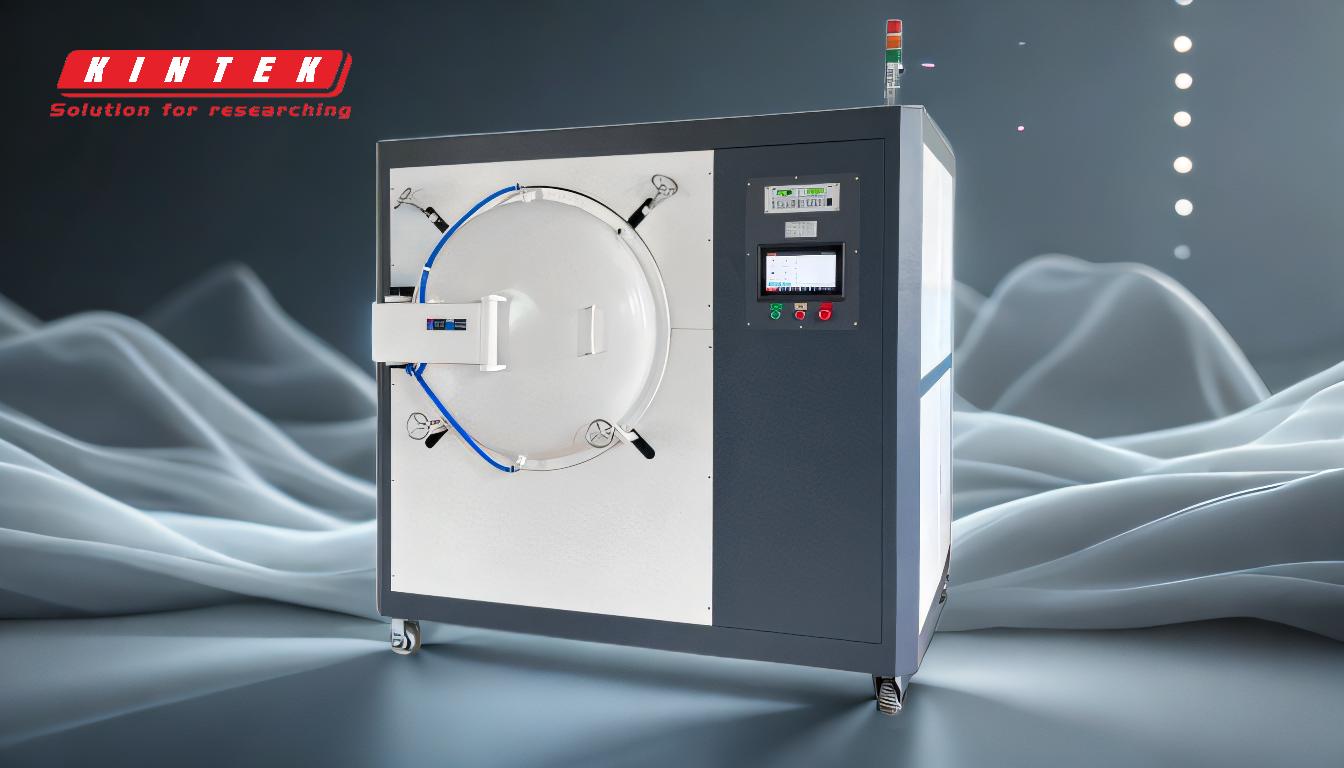
-
Temperature:
- Temperature is the most significant factor in causing melting. When heat is applied to a solid, the energy is absorbed by its particles, increasing their kinetic energy.
- As the temperature rises, the particles vibrate more intensely, eventually overcoming the intermolecular forces that hold them in a fixed lattice structure.
- The melting point is the specific temperature at which a solid becomes a liquid. For example, ice melts at 0°C (32°F) under standard atmospheric pressure.
- Different materials have different melting points due to variations in their atomic or molecular structures. For instance, metals like iron have high melting points, while organic compounds like wax have relatively low melting points.
-
Pressure:
- Pressure plays a dual role in melting. For most substances, increasing pressure raises the melting point because it compresses the solid, making it harder for particles to break free.
- However, for some materials, such as water, increasing pressure can lower the melting point. This is due to the unique behavior of water molecules, which expand upon freezing. Applying pressure counteracts this expansion, making it easier for ice to melt.
- In geological contexts, such as the Earth's mantle, high pressure combined with high temperatures can cause rocks to melt, forming magma. This process is critical in plate tectonics and volcanic activity.
-
Impurities:
- The presence of impurities in a solid can significantly affect its melting point. Impurities disrupt the orderly arrangement of particles in the solid, weakening the intermolecular forces.
- This disruption lowers the energy required to break the bonds, effectively reducing the melting point. For example, adding salt to ice lowers its melting point, which is why salt is used to de-ice roads in winter.
- In metallurgy, alloying (adding other elements to a metal) is a common technique to alter the melting point and other properties of metals. For instance, adding carbon to iron creates steel, which has a different melting point and mechanical properties compared to pure iron.
By understanding these three factors—temperature, pressure, and impurities—we can better predict and control the melting behavior of various materials, which is essential in fields like materials science, engineering, and geology.
Summary Table:
Factor | Role in Melting | Example |
---|---|---|
Temperature | Increases kinetic energy, allowing particles to break free from fixed positions. | Ice melts at 0°C (32°F) under standard pressure. |
Pressure | Can raise or lower melting point depending on the substance. | High pressure lowers ice's melting point; raises most solids' melting point. |
Impurities | Disrupts particle arrangement, lowering the melting point. | Salt lowers ice's melting point, used in de-icing roads. |
Want to learn more about how melting factors impact your projects? Contact our experts today!