Calcination is a thermal treatment process applied to various ores and solid materials to induce chemical or physical changes, such as thermal decomposition, removal of volatile components, or phase transitions. This process is typically carried out below the material's melting point and often in the absence or limited supply of air or oxygen. Common ores subjected to calcination include limestone, dolomite, and magnesite, which undergo decomposition to produce lime, magnesia, and other useful compounds. Calcination is widely used in industries to extract metals, improve material properties, or prepare materials for further processing. Rotary kilns are often employed for efficient and uniform calcination, especially for materials with particle sizes of 60 mm or less.
Key Points Explained:
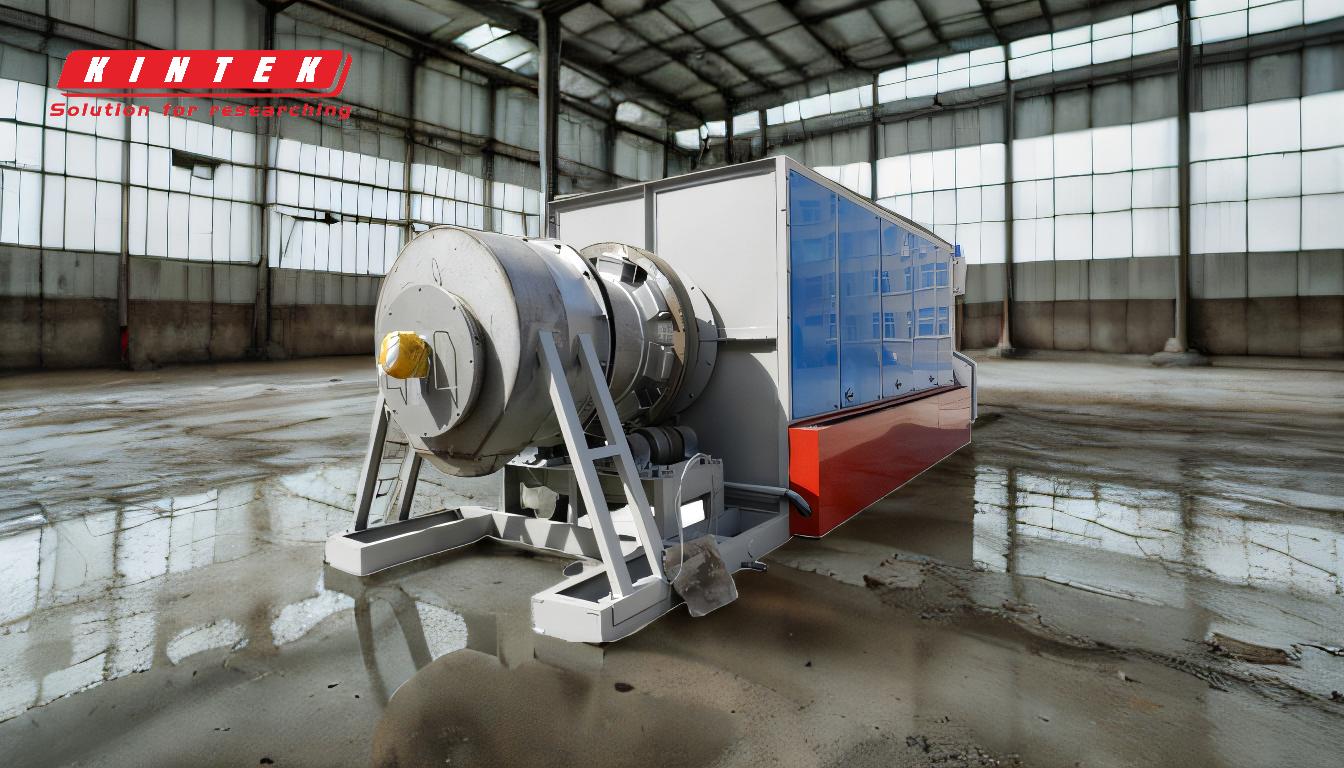
-
Definition of Calcination:
- Calcination is a heat treatment process where ores or solid materials are heated below their melting point, typically in the absence or limited supply of air or oxygen. This process induces thermal decomposition, removes volatile substances, or causes phase transitions.
-
Purpose of Calcination:
- Thermal Decomposition: Calcination breaks down compounds into simpler substances. For example, limestone (CaCO₃) decomposes into lime (CaO) and carbon dioxide (CO₂) upon heating.
- Removal of Volatiles: Volatile components, such as water or carbon dioxide, are driven off during calcination, leaving behind a purer material.
- Phase Transition: Calcination can alter the physical or chemical structure of a material, making it more suitable for further processing or use.
-
Common Ores Subjected to Calcination:
- Limestone (CaCO₃): Calcination of limestone produces lime (CaO), a key material in construction, cement production, and chemical industries.
- Dolomite (CaMg(CO₃)₂): Dolomite undergoes calcination to produce a mixture of calcium oxide (CaO) and magnesium oxide (MgO), used in refractory materials and steelmaking.
- Magnesite (MgCO₃): Calcination of magnesite yields magnesia (MgO), which is used in refractory linings, fertilizers, and environmental applications.
-
Industrial Applications:
- Metal Extraction: Calcination is often a preliminary step in extracting metals from ores, such as in the production of alumina from bauxite.
- Cement Production: Calcination of limestone is a critical step in cement manufacturing, where it is used to produce clinker.
- Refractory Materials: Calcined dolomite and magnesite are essential in producing high-temperature-resistant materials for industrial furnaces.
-
Equipment Used for Calcination:
- Rotary Kilns: These are widely used for calcination due to their ability to handle large volumes of material and provide uniform heating. They are particularly effective for materials with particle sizes of 60 mm or less.
- Static Kilns: Used for smaller-scale operations or specific materials where rotary kilns are not suitable.
-
Process Conditions:
- Temperature: Calcination typically occurs at high temperatures, often between 800°C and 1200°C, depending on the material and desired outcome.
- Atmosphere: The process is usually carried out in the absence or limited supply of air or oxygen to prevent oxidation or other unwanted reactions.
-
Examples of Calcination:
- Production of Lime: Limestone is calcined to produce lime, which is used in construction, agriculture, and chemical industries.
- Production of Magnesia: Magnesite is calcined to produce magnesia, which is used in refractory materials and environmental applications.
-
Benefits of Calcination:
- Improved Material Properties: Calcination enhances the physical and chemical properties of materials, making them more suitable for specific applications.
- Increased Purity: By removing volatile components, calcination increases the purity of the final product.
- Versatility: Calcination can be applied to a wide range of materials, making it a versatile process in various industries.
By understanding the types of ores subjected to calcination and the processes involved, purchasers and operators can make informed decisions about material selection, equipment, and process optimization to achieve desired outcomes efficiently.
Summary Table:
Aspect | Details |
---|---|
Definition | Heat treatment below melting point, often in limited air/oxygen supply. |
Purpose | Thermal decomposition, removal of volatiles, and phase transitions. |
Common Ores | Limestone, dolomite, magnesite. |
Industrial Uses | Metal extraction, cement production, refractory materials. |
Equipment | Rotary kilns (for uniform heating), static kilns (small-scale operations). |
Process Conditions | 800°C–1200°C, limited air/oxygen. |
Benefits | Improved material properties, increased purity, and versatility. |
Optimize your calcination process with expert guidance—contact us today!