Physical Vapor Deposition (PVD) is a versatile and widely used technique for applying thin films to various materials, enhancing their properties for specific applications. It is employed across multiple industries, including aerospace, semiconductors, solar energy, tool manufacturing, and biomedical fields. PVD is particularly valued for its ability to create dense, durable, and temperature-resistant coatings, making it ideal for components exposed to extreme conditions. Additionally, it is used for optical films, corrosion-resistant coatings, and decorative finishes, demonstrating its adaptability to diverse industrial needs.
Key Points Explained:
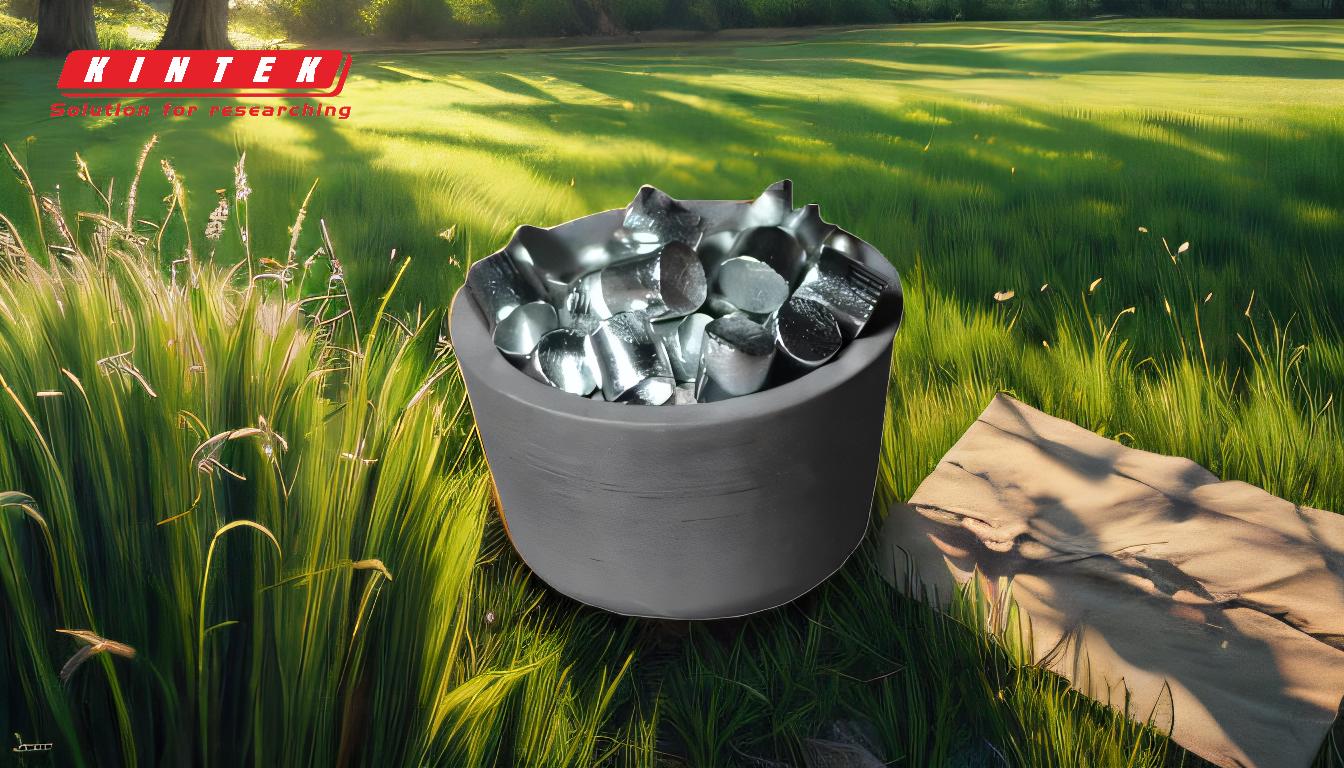
-
Aerospace Industry:
- Application: PVD is used to apply dense, temperature-resistant coatings to aerospace components.
- Purpose: These coatings enhance the durability and performance of parts exposed to extreme temperatures and harsh environments.
- Example: E-beam evaporation is a common PVD method used to deposit coatings that protect against wear, oxidation, and thermal stress.
-
Semiconductor and Electronics:
- Application: PVD is utilized in the manufacture of semiconductor devices and optical films.
- Purpose: It helps create thin films with precise mechanical, optical, and electronic properties.
- Example: Optical films for solar panels and semiconductor devices are often produced using PVD techniques like e-beam evaporation.
-
Solar Energy:
- Application: PVD is used to deposit thin films on solar panels.
- Purpose: These films improve the efficiency and durability of solar cells by enhancing light absorption and protecting against environmental damage.
- Example: Thin-film solar panels often use PVD to apply layers of materials like cadmium telluride or copper indium gallium selenide.
-
Tool Manufacturing:
- Application: PVD is employed to apply hard, corrosion-resistant coatings to cutting tools and industrial equipment.
- Purpose: These coatings extend the lifespan of tools and improve their performance in demanding applications.
- Example: Titanium nitride coatings applied via PVD are commonly used on cutting tools for metalworking.
-
Biomedical Field:
- Application: PVD is used to create biocompatible coatings for medical devices and implants.
- Purpose: These coatings enhance the performance and longevity of biomedical devices while ensuring compatibility with human tissue.
- Example: PVD coatings on orthopedic implants improve wear resistance and reduce the risk of adverse reactions.
-
Decorative Coatings:
- Application: PVD is used to apply decorative and functional coatings to consumer products.
- Purpose: These coatings provide aesthetic appeal while also offering durability and resistance to wear and corrosion.
- Example: PVD is used to create coatings on watches, jewelry, and architectural elements.
-
Food Packaging:
- Application: PVD is used to deposit thin films on materials like PET for food packaging.
- Purpose: These films provide barrier properties that protect food from moisture, oxygen, and other contaminants.
- Example: Aluminized PET film, produced using PVD, is widely used in food packaging and balloons.
By understanding these key applications, it becomes clear that PVD is a critical technology across a wide range of industries, offering solutions for enhancing material properties, improving performance, and extending the lifespan of products.
Summary Table:
Industry | Application | Purpose | Example |
---|---|---|---|
Aerospace | Dense, temperature-resistant coatings for components | Enhances durability and performance in extreme conditions | E-beam evaporation for wear, oxidation, and thermal stress protection |
Semiconductors | Thin films for semiconductor devices and optical films | Creates precise mechanical, optical, and electronic properties | Optical films for solar panels and devices using e-beam evaporation |
Solar Energy | Thin films on solar panels | Improves efficiency and durability by enhancing light absorption and environmental resistance | Cadmium telluride or copper indium gallium selenide layers |
Tool Manufacturing | Hard, corrosion-resistant coatings for cutting tools | Extends tool lifespan and improves performance in demanding applications | Titanium nitride coatings for metalworking tools |
Biomedical | Biocompatible coatings for medical devices and implants | Enhances device performance, longevity, and tissue compatibility | PVD coatings on orthopedic implants for wear resistance |
Decorative | Functional and decorative coatings for consumer products | Provides aesthetic appeal, durability, and resistance to wear and corrosion | Coatings on watches, jewelry, and architectural elements |
Food Packaging | Thin films on PET for food packaging | Protects food from moisture, oxygen, and contaminants | Aluminized PET film for food packaging and balloons |
Interested in how PVD can transform your industry? Contact us today to learn more!