The most commonly used furnaces for melting non-ferrous metals, particularly aluminum, are stationary bale-out or hydraulic tilting crucible furnaces. These furnaces are favored for their flexibility, which is essential for frequent alloy changes and extended shutdowns, as well as their relatively small footprint. They can be powered by natural gas, oil, electric resistance, or electric induction. For larger-scale operations, gas-fired or electric resistance wet bath reverberatory melters, gas-fired dry hearth furnaces, and gas-fired stack melters are also utilized. Additionally, electric resistance heated 'globar' aluminum wet bath reverberatory furnaces are preferred for applications requiring high metal quality, such as in electric motor rotor casting, due to their energy efficiency and low melt losses.
Key Points Explained:
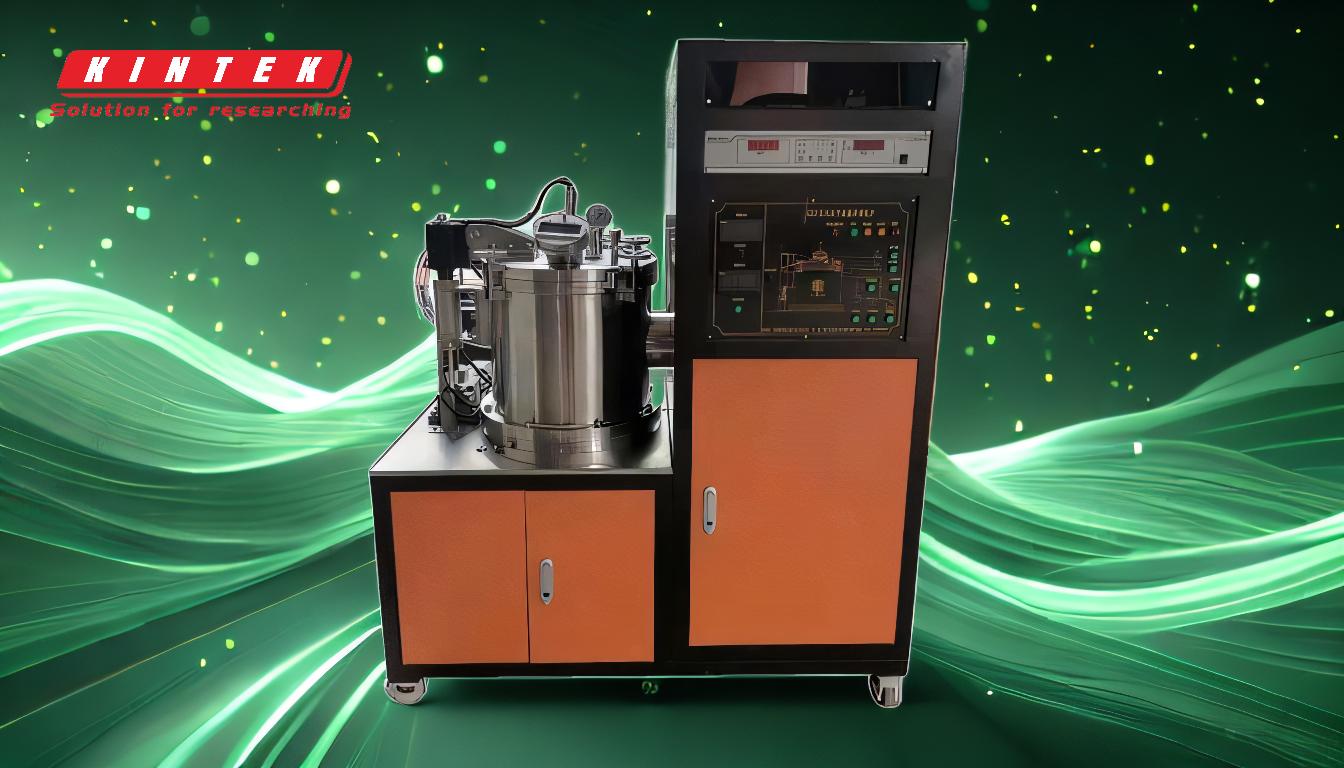
-
Stationary Bale-Out or Hydraulic Tilting Crucible Furnaces
- Flexibility: These furnaces are highly adaptable, making them ideal for foundries that frequently change alloys or experience extended shutdowns.
- Small Footprint: Their compact design is beneficial for facilities with limited space.
- Heat Sources: They can be powered by natural gas, oil, electric resistance, or electric induction, offering versatility in energy usage.
-
Larger Capacity Operations
- Gas-Fired or Electric Resistance Wet Bath Reverberatory Melters: These are used for larger-scale melting operations, providing efficient heat transfer and melting capacity.
- Gas-Fired Dry Hearth Furnaces: These furnaces are suitable for applications requiring consistent and high-quality metal output.
- Gas-Fired Stack Melters: These are designed for continuous melting processes, often used in high-volume production environments.
-
Electric Resistance Heated 'Globar' Aluminum Wet Bath Reverberatory Furnaces
- High Energy Efficiency: These furnaces achieve 60-65% energy efficiency, making them cost-effective and environmentally friendly.
- Superior Metal Quality: They produce high-quality metal, which is critical for applications like electric motor rotor casting.
- Low Melt Losses: With melt losses of less than 3%, these furnaces minimize material waste.
-
Furnace Structure
- Rectangular and Circular Designs: The structure of the furnace plays a significant role in heat transfer, melting capacity, and energy consumption. A well-designed furnace can enhance these factors, leading to more efficient operations.
-
Low-Pressure Casting Furnaces
- Pressurized Holding Furnaces: These are integrated into low-pressure casting machines and are supplied with molten aluminum from a central melting furnace.
- Central Melting Furnace Options: The central furnace can be a gas dry hearth furnace, a gas or electric tilting crucible furnace, or a gas or electric resistance wet bath reverberatory furnace.
-
Electric Arc and Induction Melting Furnaces
- Electric Arc Furnaces: These use an electric arc to generate heat, making them suitable for melting a wide range of metals.
- Induction Furnaces: These use electromagnetic induction to heat and melt metals, offering precise temperature control and energy efficiency.
In summary, the choice of furnace for melting non-ferrous metals depends on the specific requirements of the operation, including the scale of production, the need for flexibility, and the desired quality of the metal. Stationary bale-out or hydraulic tilting crucible furnaces are the most commonly used due to their versatility and compact design, while other types of furnaces are employed for larger-scale or specialized applications.
Summary Table:
Furnace Type | Key Features | Applications |
---|---|---|
Stationary Bale-Out/Tilting Crucible | Flexibility, small footprint, multiple heat sources (gas, oil, electric) | Frequent alloy changes, limited space facilities |
Gas-Fired/Electric Reverberatory Melters | Efficient heat transfer, high melting capacity | Large-scale operations |
'Globar' Aluminum Wet Bath Furnaces | 60-65% energy efficiency, high metal quality, <3% melt losses | Electric motor rotor casting, high-quality applications |
Electric Arc/Induction Furnaces | Precise temperature control, energy efficiency, wide metal compatibility | Versatile melting for various metals |
Need help choosing the right furnace for your operations? Contact our experts today for tailored solutions!