Aluminum melting requires specialized furnaces designed to handle the metal's unique properties, such as its low density and high thermal conductivity. The most commonly used furnaces for melting aluminum are induction furnaces and rotary melting furnaces. Induction furnaces are highly efficient, reducing oxidation losses and producing high-purity aluminum, while rotary furnaces are versatile and ideal for recycling aluminum scrap. The choice of furnace depends on factors like production capacity, energy type, and operational requirements. Both types offer distinct advantages, such as precise temperature control, reduced emissions, and flexibility in handling different aluminum alloys or scrap forms.
Key Points Explained:
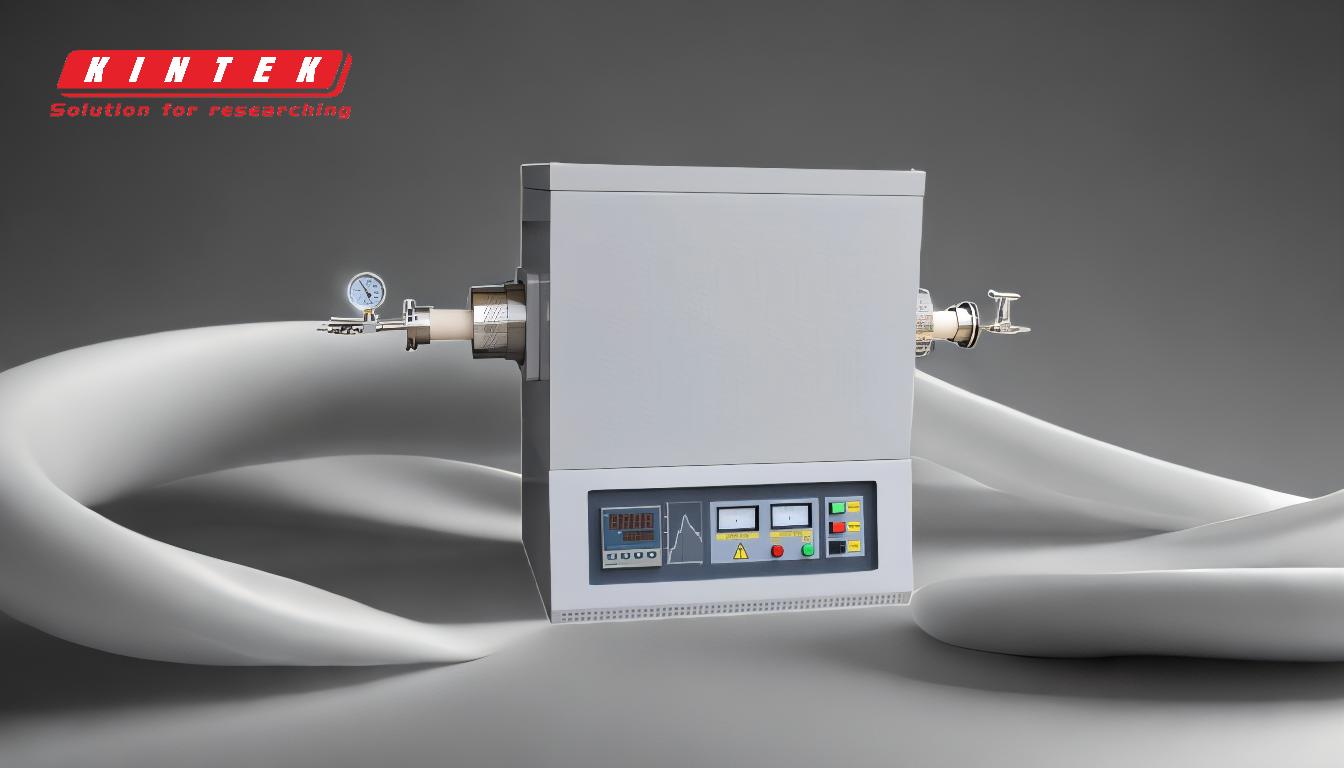
-
Induction Furnaces for Aluminum Melting:
- Induction furnaces are widely used for melting aluminum due to their efficiency, which ranges from 60% to 75%. They minimize oxidation losses and produce aluminum with high purity and uniformity.
- The heat source in an induction furnace does not directly contact the aluminum, which allows for mixed smelting of aluminum alloys.
- These furnaces use three-phase alternating current, a frequency conversion device, and a coil load to melt aluminum. Impurities rise to the surface and are removed, while pure aluminum sinks.
- Induction furnaces are quieter, produce less smoke and dust, and are more efficient than resistance furnaces or industrial frequency furnaces.
-
Rotary Melting Furnaces:
- Rotary furnaces are highly versatile and designed for recycling aluminum scrap. They are excellent for recovering all forms of scrap, making them ideal for industries focused on sustainability.
- These furnaces rotate using systems like friction drive wheels, spur rack/pinion, or chain drives, depending on the dimensions and production requirements.
- Rotary furnaces are equipped with efficient fume extraction systems, which can be fixed or tilted with the furnace. They are available with energy sources like gas, diesel, or furnace oil.
- They are lined with refractory materials and castables for superior performance and efficiency, making them suitable for forging and aluminum melting industries.
-
Factors to Consider When Choosing a Furnace:
- Capacity: Smaller furnaces (5-10 tons) are suitable for small enterprises, while larger furnaces (25 tons or more) are cost-effective for industrial use.
- Production Delivery: Some furnaces require a minimum batch size, such as 20 tonnes, with all metal from the same heat.
- Service Convenience: Dross buildup reduces furnace efficiency, so periodic cleaning is necessary. The ease of maintenance should be considered.
- Energy Type: The choice of energy (natural gas, fuel oil, diesel, or electricity) depends on availability and cost. Induction furnaces typically use electricity, while rotary furnaces can use gas or oil.
-
Advantages of Induction and Rotary Furnaces:
-
Induction Furnaces:
- High efficiency and reduced oxidation losses.
- Precise temperature control and even heat distribution.
- Ideal for producing high-purity aluminum and alloys.
-
Rotary Furnaces:
- Versatility in handling various forms of aluminum scrap.
- Efficient fume extraction and energy options.
- Suitable for large-scale industrial operations.
-
Induction Furnaces:
-
Application-Specific Considerations:
- The choice between induction and rotary furnaces depends on the desired production rate, the quality and composition of the aluminum scrap, and whether a batch or continuous mode of operation is required.
- For high-purity aluminum production, induction furnaces are preferred, while rotary furnaces are better suited for scrap recycling and large-scale operations.
-
Vacuum Melting Furnaces:
- While not explicitly mentioned in the references, vacuum melting furnaces are another option for melting aluminum, especially when high purity and minimal oxidation are critical. These furnaces operate in a vacuum environment, preventing contamination and oxidation. For more details, you can explore the topic of vacuum melting furnace.
By understanding the unique features and advantages of each furnace type, purchasers can make informed decisions based on their specific needs, such as production capacity, energy efficiency, and operational flexibility.
Summary Table:
Furnace Type | Key Features | Applications |
---|---|---|
Induction Furnace | High efficiency (60-75%), precise temperature control, minimal oxidation losses | High-purity aluminum production, alloy smelting |
Rotary Furnace | Versatile, efficient fume extraction, handles various scrap forms | Aluminum scrap recycling, large-scale operations |
Need help choosing the right furnace for your aluminum melting needs? Contact our experts today!