Annealing furnaces primarily use inert gases such as nitrogen (N2), argon (Ar), and helium (He) to create a protective atmosphere that prevents oxidation, decarburization, and other undesirable chemical reactions during the annealing process. High-purity inert gases (purity > 99.99%) are essential for maintaining the integrity of the material being treated. Additionally, hydrogen (H2) is used in specific applications, such as hydrogen vacuum furnaces, due to its reducing properties. The choice of gas depends on the material, process requirements, and desired outcomes, with pressure typically maintained between 0.05 to 0.07 MPa for optimal results.
Key Points Explained:
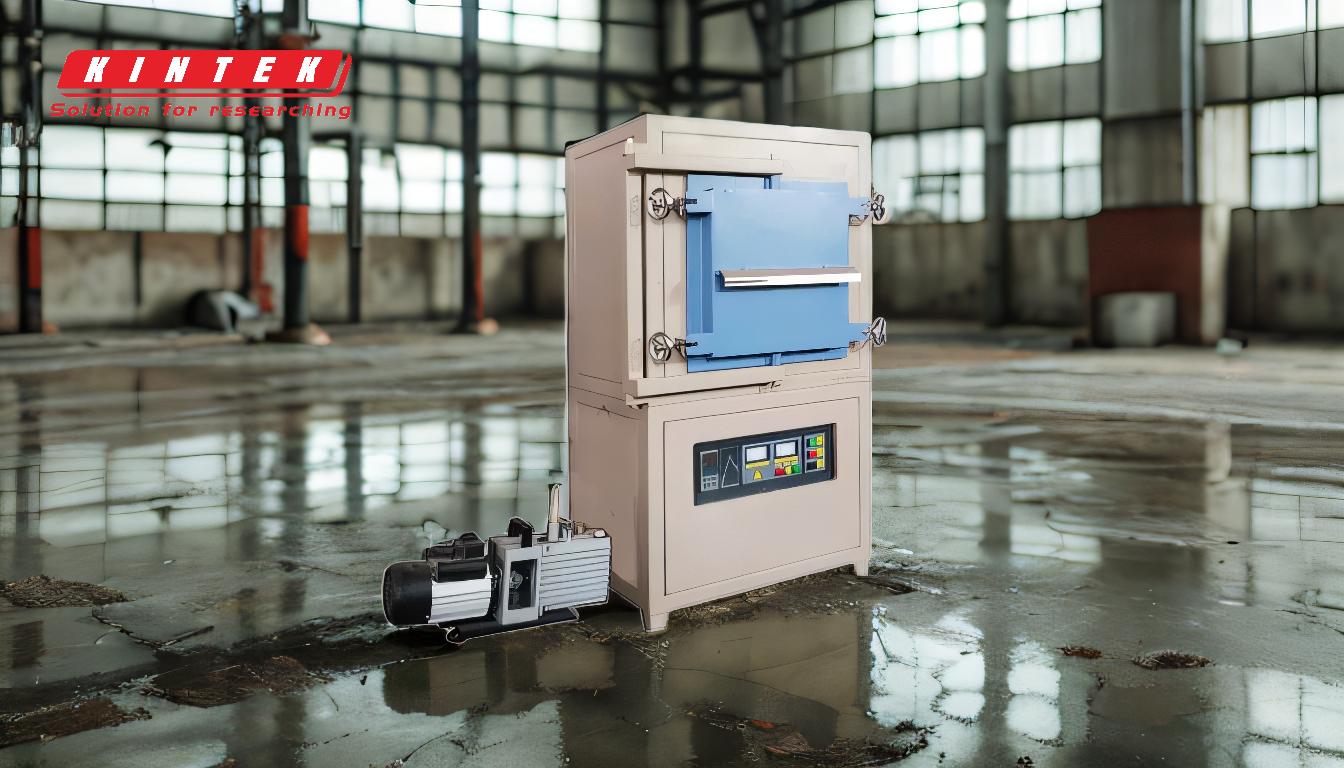
-
Primary Gases Used in Annealing Furnaces:
- Nitrogen (N2): A cost-effective and widely used inert gas that prevents oxidation and decarburization. It is suitable for most annealing processes, especially for non-reactive metals like stainless steel.
- Argon (Ar): A heavier inert gas that provides excellent protection against oxidation and is often used for annealing reactive or high-value materials like titanium and specialty alloys.
- Helium (He): A lighter inert gas with high thermal conductivity, making it suitable for processes requiring rapid heat transfer. It is less commonly used due to its higher cost.
- Hydrogen (H2): Used in hydrogen vacuum furnaces for its reducing properties, which help remove oxides from metal surfaces. It is particularly useful for annealing materials like silicon steel.
-
Importance of Gas Purity:
- High-purity inert gases (purity > 99.99%) are critical in annealing furnaces to avoid contamination and ensure consistent results. Impurities in the gas can lead to oxidation, decarburization, or other defects in the treated material.
- The purity level ensures that the protective atmosphere remains stable and effective throughout the annealing process.
-
Pressure Requirements:
- The pressure of the inert gas in the annealing furnace is typically maintained between 0.05 to 0.07 MPa. This range ensures a stable protective atmosphere while minimizing the risk of gas leakage or excessive consumption.
- Proper pressure control is essential for achieving uniform heat treatment and preventing defects in the material.
-
Role of Inert Gases in Annealing:
- Inert gases create a non-reactive environment that prevents oxidation, decarburization, and other chemical reactions during the annealing process.
- They help maintain the material's surface quality, mechanical properties, and dimensional stability.
-
Applications of Specific Gases:
- Nitrogen: Commonly used for annealing stainless steel, copper, and other non-reactive metals.
- Argon: Preferred for annealing reactive metals like titanium, zirconium, and specialty alloys.
- Hydrogen: Used in hydrogen vacuum furnaces for annealing materials requiring oxide removal, such as silicon steel.
-
Advantages of Using Inert Gases:
- Precision: Inert gases allow for precise control over the annealing process, ensuring consistent results.
- Material Integrity: They protect the material from surface defects and maintain its mechanical properties.
- Versatility: Different gases can be selected based on the material and process requirements.
-
Considerations for Gas Selection:
- Material Compatibility: The choice of gas depends on the material being annealed. For example, argon is preferred for reactive metals, while nitrogen is suitable for non-reactive metals.
- Cost: Nitrogen is more cost-effective than argon or helium, making it a popular choice for large-scale operations.
- Process Requirements: Hydrogen is used when oxide removal is necessary, while helium is chosen for processes requiring rapid heat transfer.
By understanding these key points, equipment and consumable purchasers can make informed decisions about the type of gas to use in annealing furnaces, ensuring optimal results and cost-effectiveness.
Summary Table:
Gas | Key Properties | Applications |
---|---|---|
Nitrogen (N2) | Cost-effective, prevents oxidation and decarburization | Stainless steel, copper, non-reactive metals |
Argon (Ar) | Heavy inert gas, excellent oxidation protection | Titanium, zirconium, specialty alloys |
Helium (He) | Light inert gas, high thermal conductivity | Processes requiring rapid heat transfer |
Hydrogen (H2) | Reducing properties, removes oxides | Silicon steel, hydrogen vacuum furnaces |
Need help selecting the right gas for your annealing furnace? Contact our experts today for personalized guidance!