The choice between a blast furnace and an electric arc furnace depends on the specific needs of the operation, including the type of materials being processed, energy efficiency requirements, and the desired flexibility in production. Electric arc furnaces are highly efficient for recycling scrap metal and offer operational flexibility, making them suitable for smaller-scale or variable production demands. They heat materials directly, which can be more energy-efficient under certain conditions. However, they may lose heat through the furnace structure, impacting overall thermal efficiency. Blast furnaces, on the other hand, are typically used for large-scale, continuous production of iron from ore, offering high production rates but less flexibility and higher initial setup costs.
Key Points Explained:
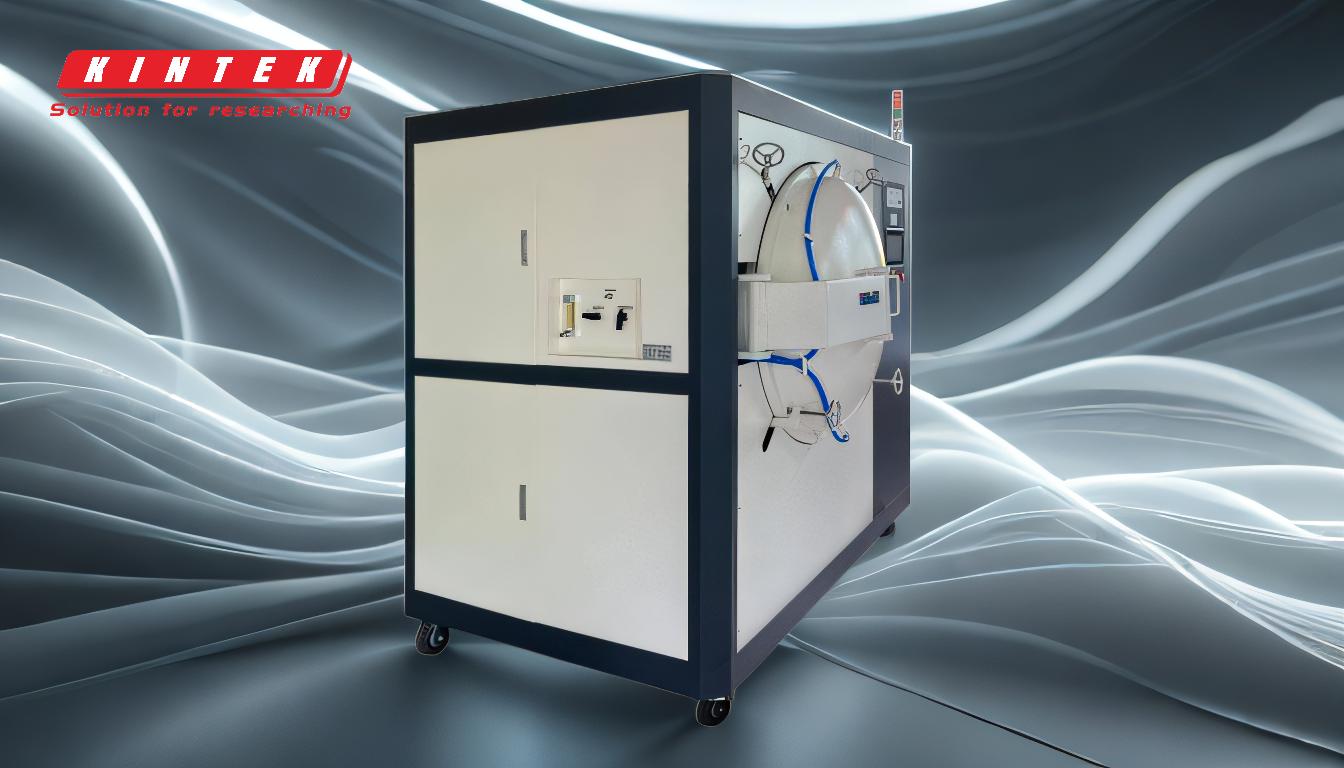
-
Material Processing Capabilities:
- Electric Arc Furnace (EAF): Excels in recycling scrap metal, capable of achieving 100% scrap metal recycling. This makes it highly suitable for operations focused on sustainability and recycling.
- Blast Furnace: Primarily used for producing iron from iron ore. It is less flexible in terms of the types of materials it can process compared to EAF.
-
Operational Flexibility:
- Electric Arc Furnace: Offers significant operational flexibility. Operators can start and stop the furnace as needed, which is beneficial for operations that do not run continuously or that need to adjust quickly to market demands.
- Blast Furnace: Generally requires continuous operation to maintain efficiency and is less adaptable to frequent starts and stops.
-
Energy Efficiency and Heating Methods:
- Electric Arc Furnace: Heats materials directly through an electric arc, which can be more energy-efficient. However, it may lose a significant amount of heat through the furnace cover and walls, which can detract from its overall thermal efficiency.
- Blast Furnace: Uses coke as a fuel and air as a blast to produce the high temperatures needed to reduce iron ore to iron. This method is highly effective for large-scale production but is generally less energy-efficient than EAF when considering the total energy lifecycle.
-
Scale and Economic Considerations:
- Electric Arc Furnace: More suitable for smaller-scale operations or those with variable production needs. The initial setup cost can be lower than that of a blast furnace, making it a viable option for smaller manufacturers.
- Blast Furnace: Economically viable for large-scale production due to its high output rates. The initial investment and operational costs are higher, but the cost per ton of iron produced can be lower at large scales.
-
Environmental Impact:
- Electric Arc Furnace: Has a lower carbon footprint when using recycled materials, contributing to reduced greenhouse gas emissions compared to traditional blast furnaces.
- Blast Furnace: Typically has a higher environmental impact due to the use of coke and the emission of carbon dioxide and other pollutants.
In conclusion, the decision between using a blast furnace or an electric arc furnace should be based on the specific requirements of the production process, including the scale of production, the type of materials being processed, and environmental considerations. Each type of furnace has its advantages and limitations, and the best choice will vary depending on the operational context.
Summary Table:
Aspect | Electric Arc Furnace (EAF) | Blast Furnace |
---|---|---|
Material Processing | Excels in recycling scrap metal; 100% scrap metal recycling | Primarily used for producing iron from ore; less material flexibility |
Operational Flexibility | High flexibility; can start/stop as needed for variable production demands | Requires continuous operation; less adaptable to frequent starts/stops |
Energy Efficiency | Direct heating via electric arc; energy-efficient but may lose heat through structure | Uses coke and air blast; less energy-efficient overall |
Scale & Economics | Suitable for smaller-scale or variable production; lower initial setup costs | Economical for large-scale production; higher initial investment and output rates |
Environmental Impact | Lower carbon footprint with recycled materials; reduced greenhouse gas emissions | Higher environmental impact due to coke usage and CO2 emissions |
Need help choosing the right furnace for your operation? Contact our experts today for personalized advice!