CVD (Chemical Vapor Deposition) and PVD (Physical Vapor Deposition) are both widely used techniques for depositing thin films, but they differ significantly in their processes, advantages, and limitations. CVD operates at higher pressures and temperatures, allowing for conformal coatings on complex geometries, but it can be limited by thermal constraints and the use of toxic gases. PVD, on the other hand, operates at lower temperatures and is safer, making it more suitable for temperature-sensitive materials and industrial applications like coating cutting tools. The choice between CVD and PVD depends on the specific application, material requirements, and operational constraints.
Key Points Explained:
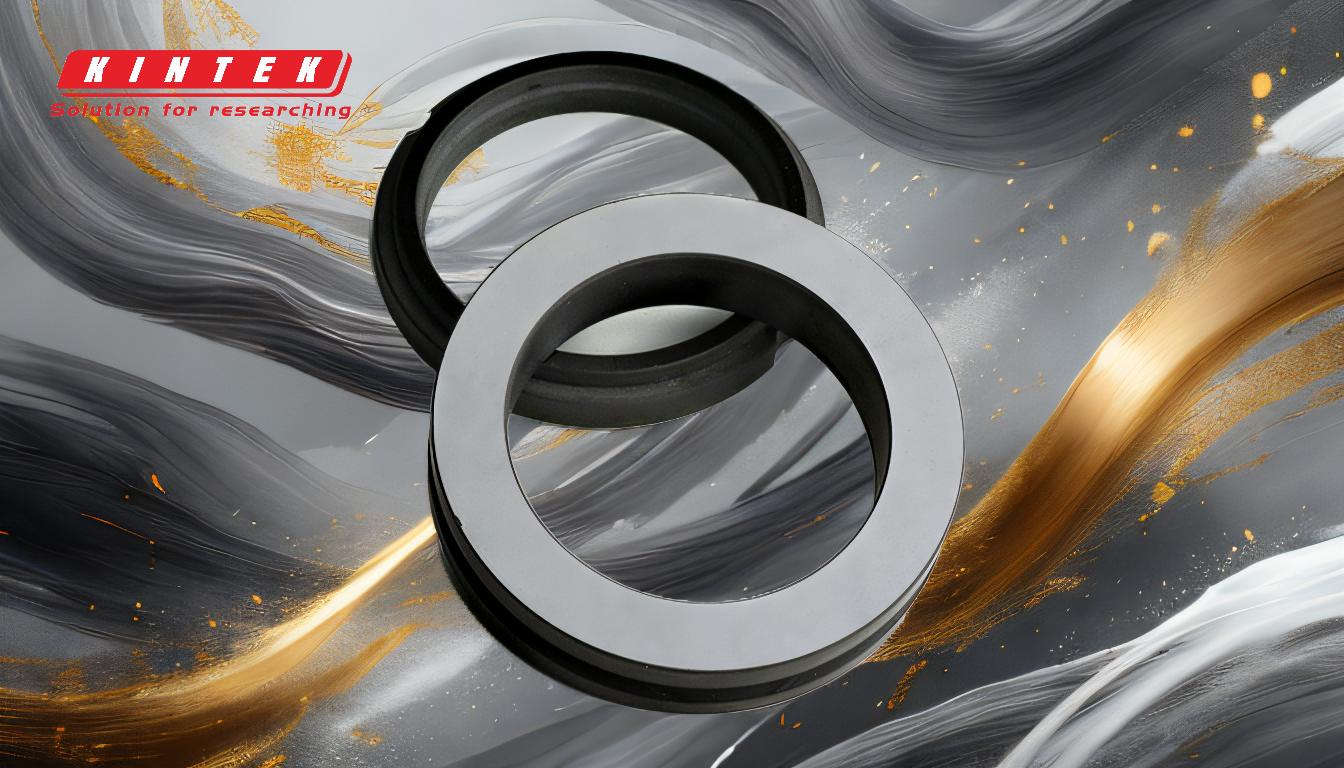
-
Process Differences:
- CVD: Involves heating a precursor to create a vapor that reacts and condenses on the substrate. It operates at higher temperatures (up to 900 °C) and pressures, which allows for conformal coatings on complex geometries.
- PVD: Involves vaporizing the material from its solid phase and condensing it on the substrate in a vacuum environment. It operates at lower temperatures, making it suitable for temperature-sensitive materials.
-
Advantages of CVD:
- Conformal Coatings: CVD can deposit films on substrates with irregular surfaces or in deep holes due to its higher pressure and laminar flow properties.
- Material Versatility: CVD can use elements that are difficult to evaporate but are available as volatile chemical compounds.
- Atmospheric Pressure: CVD can be performed at atmospheric pressure, reducing the need for high vacuum pumps.
-
Advantages of PVD:
- Lower Temperature: PVD operates at lower temperatures, making it suitable for temperature-sensitive materials and reducing energy costs.
- Environmental Friendliness: PVD is more environmentally friendly compared to processes like electroplating.
- Material Properties: PVD can deposit materials with improved properties compared to the substrate material.
-
Limitations of CVD:
- Thermal Constraints: CVD requires high temperatures, which can affect tool performance and make it unsuitable for low melting point polymers.
- Toxic Gases: CVD uses volatile chemicals that can produce harmful gases, requiring extensive gas management infrastructure.
-
Limitations of PVD:
- Line-of-Sight: PVD is limited by line-of-sight effects, making it difficult to coat deep holes or shaded areas.
- Material Waste: PVD can result in more material waste compared to CVD, which selectively coats only the heated area.
-
Industrial Applications:
- CVD: Often used for applications requiring conformal coatings, such as in the semiconductor industry.
- PVD: Preferred for industrial applications like coating cutting tools due to its lower temperature operation and safety.
In summary, the choice between CVD and PVD depends on the specific requirements of the application, including the material properties, substrate geometry, and operational constraints. Each method has its own set of advantages and limitations that must be carefully considered.
Summary Table:
Aspect | CVD | PVD |
---|---|---|
Process | Higher temperatures (up to 900 °C), conformal coatings | Lower temperatures, line-of-sight deposition |
Advantages | Conformal coatings, material versatility, atmospheric pressure | Lower temperature, environmentally friendly, improved material properties |
Limitations | Thermal constraints, toxic gases | Line-of-sight effects, material waste |
Applications | Semiconductor industry, conformal coatings | Coating cutting tools, temperature-sensitive materials |
Still unsure which method is right for your application? Contact our experts today for personalized advice!