PVD (Physical Vapor Deposition) and electroplating are two widely used surface coating technologies, each with its own advantages and limitations. PVD is generally considered superior in terms of durability, wear resistance, environmental safety, and aesthetic longevity. It is harder, more resistant to corrosion and UV radiation, and does not require additional protective coatings. Electroplating, while effective for certain applications, tends to degrade over time, tarnish, and release harmful chemicals. PVD is particularly favored in industries like aerospace, medical, and marine due to its robustness and environmental friendliness. However, the choice between PVD and electroplating ultimately depends on the specific application, budget, and desired properties of the coating.
Key Points Explained:
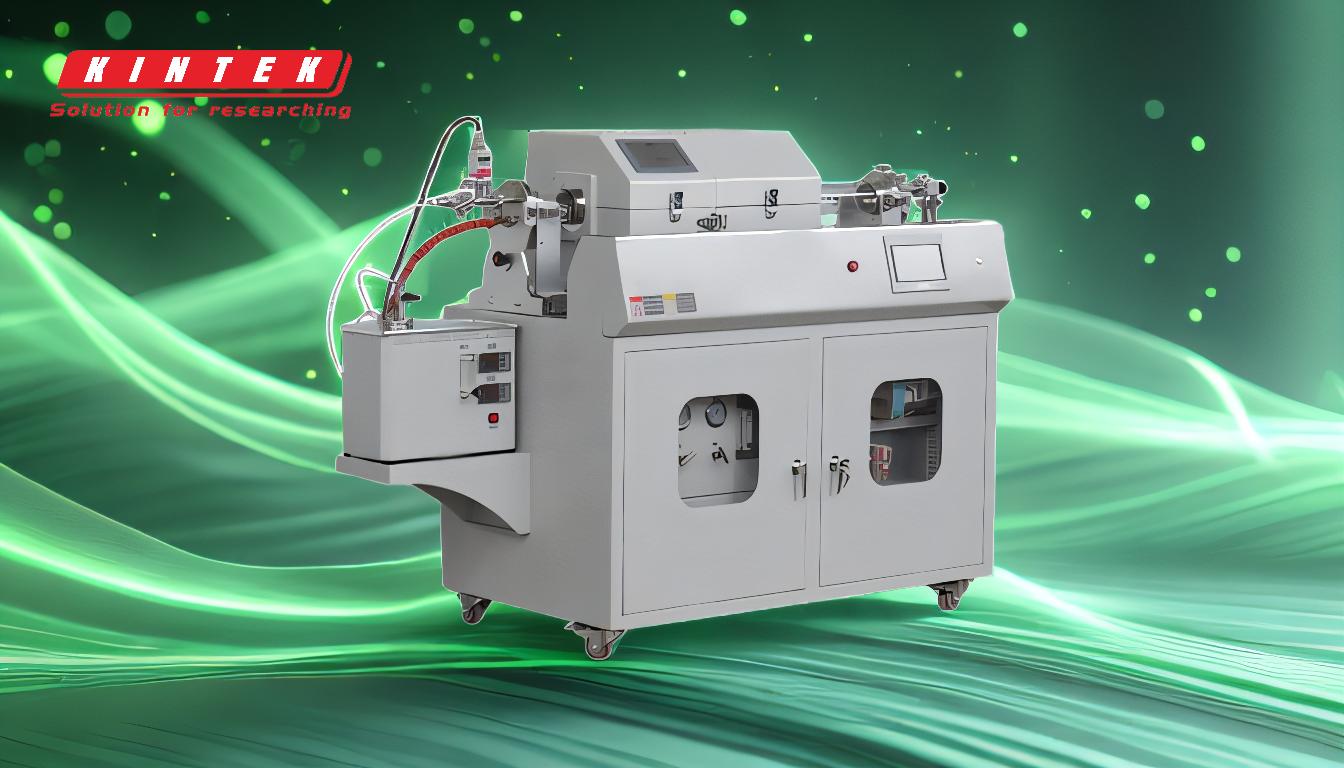
-
Durability and Wear Resistance:
- PVD coatings are significantly harder and more resistant to wear and tear compared to electroplated coatings. This makes PVD ideal for applications where the coated surface is subject to frequent abrasion or impact.
- Electroplated coatings, while durable, often require a clear top coat that can degrade over time, leading to tarnishing and corrosion. PVD coatings do not require such additional layers, making them inherently more durable.
-
Environmental Safety:
- PVD is an environmentally friendly process that produces no harmful by-products. This is a significant advantage over electroplating, which often involves the use of toxic chemicals and can release harmful substances into the atmosphere.
- For industries and applications where environmental impact is a concern, PVD is the preferred choice due to its cleaner and safer production process.
-
Aesthetic Longevity:
- PVD coatings maintain their color and appearance over time, even under prolonged exposure to UV radiation. This makes them ideal for applications where aesthetic appeal is important, such as in consumer electronics or decorative items.
- Electroplated coatings, on the other hand, can tarnish or discolor over time, especially if the protective clear coat degrades.
-
Corrosion and Chemical Resistance:
- PVD coatings are highly resistant to corrosion, making them suitable for harsh environments, including marine applications. They also resist saltwater, scratching, and prolonged exposure to ultraviolet light.
- Electroplated coatings, while offering some level of corrosion resistance, are generally less robust and can degrade more quickly in challenging environments.
-
Temperature and Abrasion Resistance:
- PVD coatings can withstand high temperatures and provide excellent abrasion resistance, making them suitable for high-performance applications in industries like aerospace and medical devices.
- Electroplated coatings may not offer the same level of performance under extreme conditions, limiting their use in high-stress environments.
-
Uniformity and Application:
- PVD coatings are more uniform in appearance, providing a consistent finish that is difficult to achieve with electroplating. This uniformity is particularly important in precision industries where even minor imperfections can be critical.
- Electroplating can sometimes result in uneven coatings, especially on complex geometries, which can affect both the appearance and performance of the coated item.
-
Cost and Maintenance:
- While PVD coatings may have a higher initial cost, they often result in lower maintenance costs over time due to their durability and resistance to wear and corrosion.
- Electroplated coatings, while potentially cheaper upfront, may require more frequent maintenance or replacement, leading to higher long-term costs.
-
Industry Applications:
- PVD is widely used in industries that demand high performance and durability, such as aerospace, medical, and high-tech. Its ability to withstand extreme conditions makes it a preferred choice for critical applications.
- Electroplating is still used in many industries, particularly where cost is a primary concern, but it is increasingly being replaced by PVD in applications where performance and longevity are more important.
In summary, PVD is generally the better choice for applications requiring high durability, environmental safety, and aesthetic longevity, while electroplating may still be suitable for less demanding or cost-sensitive applications. The decision should be based on the specific requirements of the project, including performance needs, environmental considerations, and budget constraints.
Summary Table:
Aspect | PVD | Electroplating |
---|---|---|
Durability | Harder, more wear-resistant, no additional coatings needed. | Requires clear top coat; prone to tarnishing and corrosion. |
Environmental Safety | No harmful by-products; eco-friendly. | Uses toxic chemicals; releases harmful substances. |
Aesthetic Longevity | Maintains color and appearance under UV exposure. | Tarnishes/discolors over time. |
Corrosion Resistance | Highly resistant to corrosion and harsh environments. | Less robust; degrades faster in challenging conditions. |
Temperature Resistance | Withstands high temperatures; excellent for extreme environments. | Limited performance under high-stress conditions. |
Uniformity | Provides consistent, uniform coatings. | May result in uneven coatings on complex geometries. |
Cost | Higher initial cost but lower maintenance over time. | Cheaper upfront but higher long-term maintenance costs. |
Industry Applications | Aerospace, medical, marine, and high-tech industries. | Cost-sensitive applications where performance is less critical. |
Still unsure which coating technology is right for your project? Contact our experts today for personalized advice!